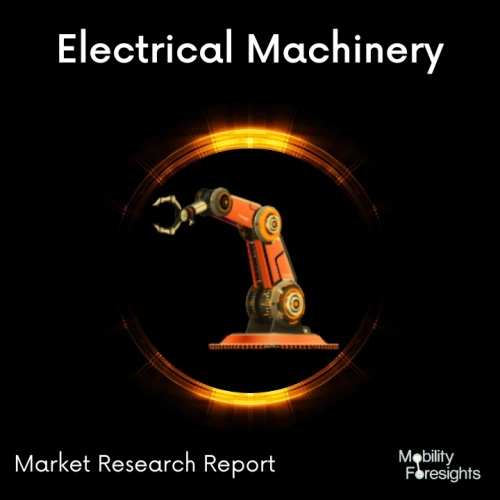
- Get in Touch with Us
Last Updated: Apr 25, 2025 | Study Period: 2024-2030
The steam system is shielded from corrosive gas effects by deaeration. By lowering the concentration of dissolved oxygen and carbon dioxide to a point where corrosion is minimal, it is able to do this.
The removal of air from a fluidized bed is known as deaeration. Thermal deaeration is typically used to remove oxygen. Deaeration is used to eliminate 95% of the dissolved oxygen before it reaches the pumps.
When air has combined with or dissolved in a substance, it must be removed by the deaeration process. Deaeration improves the quality and reduces contamination of liquids, soils, and foods. It also removes oxygen from liquid-filled vessels to slow down corrosion.
Deaerators work on the basis of Henry's Law of Partial Pressure, a physical chemistry theory that states that the amount of dissolved gas in a liquid is inversely related to the partial pressure above that liquid.
A deaerator raises the temperature of the water in a plant to increase thermal efficiency while reducing dissolved gases, mainly oxygen, to a low level. Deaerators also provide feedwater storage and ideal suction for boiler feedwater pumps.
Deaeration removes oxygen and other gases that cannot condense. Internal therapies include blowdown and chemical additives. The different external treatments given to the boiler water are reinforced by the addition of chemicals such as oxygen scavengers, hydroxides, phosphates, polymers, chelates, and amines.
The Global Deaeration Machine market accounted for $XX Billion in 2023 and is anticipated to reach $XX Billion by 2030, registering a CAGR of XX% from 2024 to 2030.
The ESC Center Deaerator Modern boiler water protection and control include mechanical and chemical deaeration. The best and highest quality feed water for boiler use is provided via deaeration in conjunction with additional external treatment measures.
The dissolved gases oxygen, carbon dioxide, and ammonia are the most frequent causes of corrosion in boiler systems. Oxygen is the most aggressive of these.
One cannot overstate how crucial it is to take oxygen out of the equation as a cause of pitting and iron accumulation. This gas can seriously impair corrosion even in low quantities.
Makeup water significantly increases the amount of oxygen in the body. The condensate return system is another source of oxygen that might enter the feed water system.
Direct air leakage from pumps' suction sides, vacuum systems, the breathing action of closed condensate receiving tanks, open condensate receiving tanks, and leakage of non-deuterated water used for condensate pump seal and/or quench water are all potential return line sources. Good housekeeping is a crucial component of the preventative approach with all of these sources.
The process of removing oxygen and other corrosive gases from feed water begins with mechanical deaeration. Deaeration also removes free carbon dioxide, whereas mixed carbon dioxide is discharged with the steam in the boiler and dissolves in the condensate thereafter.
This can lead to more corrosion issues. This discussion on the deaerator will focus on lowering the oxygen content of the feed water because dissolved oxygen is a persistent danger to the integrity of boiler tubes.
The tray type and the spray type of deaerators are the two main varieties. In both situations, a steam atmosphere is sprayed with cold makeup water to remove the majority of the gas.
Sl no | Topic |
1 | Market Segmentation |
2 | Scope of the report |
3 | Abbreviations |
4 | Research Methodology |
5 | Executive Summary |
6 | Introduction |
7 | Insights from Industry stakeholders |
8 | Cost breakdown of Product by sub-components and average profit margin |
9 | Disruptive innovation in the Industry |
10 | Technology trends in the Industry |
11 | Consumer trends in the industry |
12 | Recent Production Milestones |
13 | Component Manufacturing in US, EU and China |
14 | COVID-19 impact on overall market |
15 | COVID-19 impact on Production of components |
16 | COVID-19 impact on Point of sale |
17 | Market Segmentation, Dynamics and Forecast by Geography, 2024-2030 |
18 | Market Segmentation, Dynamics and Forecast by Product Type, 2024-2030 |
19 | Market Segmentation, Dynamics and Forecast by Application, 2024-2030 |
20 | Market Segmentation, Dynamics and Forecast by End use, 2024-2030 |
21 | Product installation rate by OEM, 2023 |
22 | Incline/Decline in Average B-2-B selling price in past 5 years |
23 | Competition from substitute products |
24 | Gross margin and average profitability of suppliers |
25 | New product development in past 12 months |
26 | M&A in past 12 months |
27 | Growth strategy of leading players |
28 | Market share of vendors, 2023 |
29 | Company Profiles |
30 | Unmet needs and opportunity for new suppliers |
31 | Conclusion |
32 | Appendix |