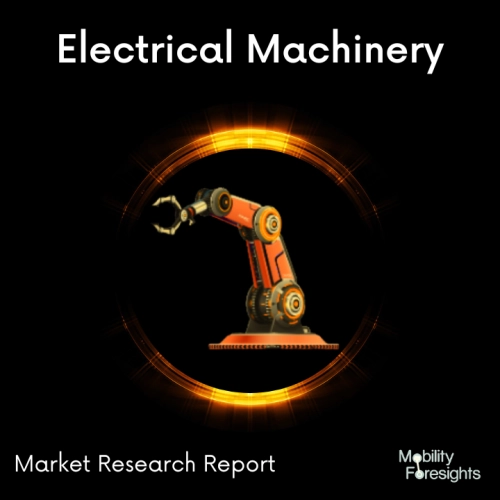
- Get in Touch with Us
Last Updated: Apr 26, 2025 | Study Period: 2024-2030
A three-dimensional inspection system is a machine that uses three-dimensional imaging technology to inspect objects for defects, flaws, and other irregularities. It is used in a variety of industries such as automotive, aerospace, medical and consumer goods. The system works by taking a series of two-dimensional images of an object, and combining them to form a three-dimensional image.
This image is then analyzed to locate any flaws or defects. Three-dimensional inspection systems are capable of detecting very small flaws and defects that may not be visible to the naked eye.
The 3D inspection system has several advantages over traditional methods of inspection such as visual inspection and manual inspection. It is much faster and more efficient, and can provide more detailed and accurate results. It is also less labour-intensive, meaning it can be used in a wider range of applications.
The 3D inspection system can be used for a variety of tasks, such as measuring, inspecting, and analyzing objects. It can be used to detect defects, flaws, and other irregularities in manufactured parts, as well as to identify and evaluate the shape and size of components. It can also be used to measure the surface roughness of components, and to compare parts against a reference model.
The 3D inspection system is a powerful and versatile tool that can be used in a variety of industries to ensure quality control and improve product reliability. Its accuracy and speed make it an invaluable tool for any manufacturing process.
The Global Dimensional inspection system market accounted for $XX Billion in 2023 and is anticipated to reach $XX Billion by 2030, registering a CAGR of XX% from 2024 to 2030.
Three-dimensional inspection systems are an important technology used in manufacturing and engineering. They are used to ensure that parts and components are manufactured and assembled to precise specifications.
Three-dimensional inspection systems use a variety of technologies to measure the size, shape, and position of components and parts. These include 3D scanners, optical comparators, coordinate measuring machines, and other non-contact measuring devices.
These systems provide precise measurements that are then used to compare the dimensions of the parts and components to their design specifications.
Over the past few years, several companies have launched new 3D inspection systems. These include Nikon Metrology, Hexagon, FARO Technologies, and Creaform. Nikon Metrologyâs systems use laser scanners and white light scanners to measure and inspect parts and components.
Hexagonâs systems use optical comparators and coordinate measuring machines. FARO Technologiesâ systems use portable coordinate measuring machines and laser trackers. Creaformâs systems use 3D scanners and optical comparators.
All of these companies offer various types of 3D inspection systems that are suitable for a wide range of applications. They can be used to measure and inspect parts for automotive, aerospace, medical, and other industries. These systems can be used to inspect parts for accuracy, consistency, and conformance to specifications.
In conclusion, 3D inspection systems are an important technology used in manufacturing and engineering. Several companies have launched new systems that use a variety of technologies to measure and inspect parts. These systems are used to ensure that parts and components are manufactured and assembled to precise specifications.
Sl no | Topic |
1 | Market Segmentation |
2 | Scope of the report |
3 | Abbreviations |
4 | Research Methodology |
5 | Executive Summary |
6 | Introdauction |
7 | Insights from Industry stakeholders |
8 | Cost breakdown of Product by sub-components and average profit margin |
9 | Disruptive innovation in theIndustry |
10 | Technology trends in the Industry |
11 | Consumer trends in the industry |
12 | Recent Production Milestones |
13 | Component Manufacturing in US, EU and China |
14 | COVID-19 impact on overall market |
15 | COVID-19 impact on Production of components |
16 | COVID-19 impact on Point of sale |
17 | Market Segmentation, Dynamics and Forecast by Geography, 2024-2030 |
18 | Market Segmentation, Dynamics and Forecast by Product Type, 2024-2030 |
19 | Market Segmentation, Dynamics and Forecast by Application, 2024-2030 |
20 | Market Segmentation, Dynamics and Forecast by End use, 2024-2030 |
21 | Product installation rate by OEM, 2023 |
22 | Incline/Decline in Average B-2-B selling price in past 5 years |
23 | Competition from substitute products |
24 | Gross margin and average profitability of suppliers |
25 | New product development in past 12 months |
26 | M&A in past 12 months |
27 | Growth strategy of leading players |
28 | Market share of vendors, 2023 |
29 | Company Profiles |
30 | Unmet needs and opportunity for new suppliers |
31 | Conclusion |
32 | Appendix |