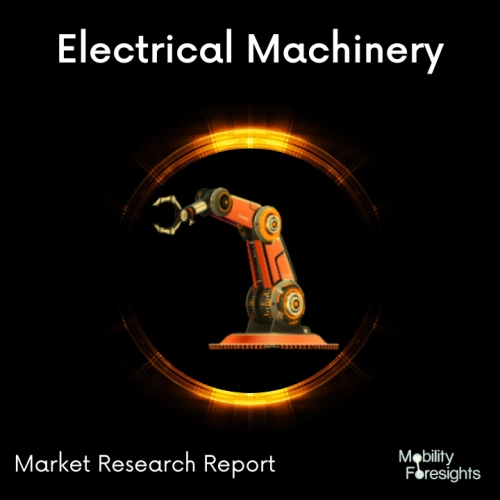
- Get in Touch with Us
Last Updated: Apr 25, 2025 | Study Period: 2024-2030
An essential element in industrial facilities is the direct drive fan motors. In today's industrial plants, fans and their motors have become crucial components.
Fan motors are utilized for a variety of purposes, including warehouse ventilation, cooling of cold shops, and simple fresh air intake.
The several fans that are accessible scarcely differ in terms of operation; rather, they do so in terms of application and application area.
It is obvious that a fan for cooling systems must adhere to different standards than a fan for air conditioning systems.
Control and energy efficiency should be given more consideration. The energy consumption is decreased in response to new restrictions, such as frequency inverters, and the life of the fan motors is also extended.
The manufacturing of fan motors is fairly straightforward. They are made up of a fan wheel attached to the accompanying shaft of an electric motor, either synchronous or asynchronous, and the connections for the lines.
However, DC motors are employed (e.g. in computers or in a car). Every motor has a stator, which houses the revolving rotor and is encircled by pole pieces.
The fan motors come in a wide variety of styles and sizes that greatly differ from one another. The location and efficiency of the engines are the cause of this.
The complexity of the structure must increase as the performance level does.
The most efficient method of controlling fan motors is through frequency inverters. Only AC and DC motors may use this since the inverter alters the frequency, which in turn regulates the speed.
The start-up and braking procedure can be optimally handled with the help of special programs. It is possible to avoid this overloading and unneeded wear and strain, which will lower the need for maintenance and maintenance costs.
Flexible inverters are an essential and long-lasting piece of technology that is virtually solely employed for control in modern plants.
The Global Direct Drive Fan Motors market accounted for $XX Billion in 2021 and is anticipated to reach $XX Billion by 2030, registering a CAGR of XX% from 2024 to 2030.
For the Aero 39M commercial air handler, Carrier is happy to offer a Direct drive fan motors option with an electronically commutated motor (ECM).
Customers can increase the system's energy efficiency by choosing the new ECM fan option. This upgrade adds yet another improvement to the recently redesigned 39M commercial air handler product range, which now provides clients with additional functionality and greater flexibility.
Carrier is a component of UTC Climate, Controls & Security, a division of United Technologies Corp., and is a global leader in high-tech heating, cooling, and refrigeration solutions (NYSE: UTX).
Electronically commutated AC motors often use less energy than variable-frequency drive AC motors and are more efficient than today's premium efficiency motors.
When the rotor's position is known, onboard electronics generate an electrical pulse that actuates the motor windings.
These electronics regulate the motor's speed and input power so that it can effectively deliver the right amount of airflow based on building demand.
Because the motor has a built-in variable-speed control, there is no need for an additional speed controller, which reduces cost, airway length, and weight.
Carrier is always introducing new technologically sophisticated choices that let clients save energy with smaller, more affordable units.
Sl no | Topic |
1 | Market Segmentation |
2 | Scope of the report |
3 | Abbreviations |
4 | Research Methodology |
5 | Executive Summary |
6 | Introduction |
7 | Insights from Industry stakeholders |
8 | Cost breakdown of Product by sub-components and average profit margin |
9 | Disruptive innovation in the Industry |
10 | Technology trends in the Industry |
11 | Consumer trends in the industry |
12 | Recent Production Milestones |
13 | Component Manufacturing in US, EU and China |
14 | COVID-19 impact on overall market |
15 | COVID-19 impact on Production of components |
16 | COVID-19 impact on Point of sale |
17 | Market Segmentation, Dynamics and Forecast by Geography, 2024-2030 |
18 | Market Segmentation, Dynamics and Forecast by Product Type, 2024-2030 |
19 | Market Segmentation, Dynamics and Forecast by Application, 2024-2030 |
20 | Market Segmentation, Dynamics and Forecast by End use, 2024-2030 |
21 | Product installation rate by OEM, 2023 |
22 | Incline/Decline in Average B-2-B selling price in past 5 years |
23 | Competition from substitute products |
24 | Gross margin and average profitability of suppliers |
25 | New product development in past 12 months |
26 | M&A in past 12 months |
27 | Growth strategy of leading players |
28 | Market share of vendors, 2023 |
29 | Company Profiles |
30 | Unmet needs and opportunity for new suppliers |
31 | Conclusion |
32 | Appendix |