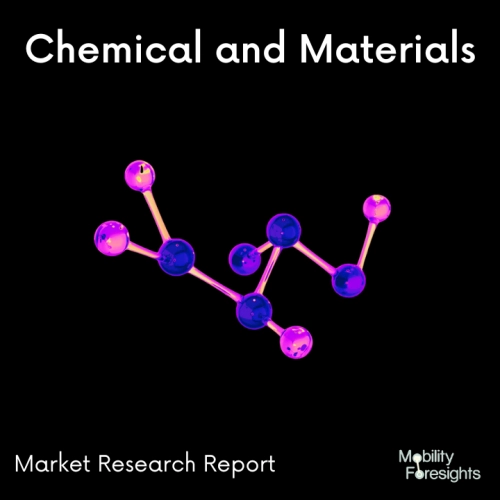
- Get in Touch with Us
Last Updated: Apr 25, 2025 | Study Period: 2024-2030
Long fiber thermoplastic (LFT) composites provide great impact resistance, superior specific modulus and strength, as well as additional benefits such as simple processing, recyclability, and superior corrosion resistance.
The Global Direct long fiber thermoplastic (D-LFT) market accounted for $XX Billion in 2023 and is anticipated to reach $XX Billion by 2030, registering a CAGR of XX% from 2024 to 2030.
In automotive and other durables, LFT-D thrives. Teijin Automotive Technologies recently completed the installation of its tenth LFT-D (long-fiber thermoplastic direct compounding) system at its location in Sarepta, Louisiana.
Engineering manager adds that utilization of LFT-D technology continues to expand in this market sector and that Teijin requires the additional capacity after being given a new production schedule for the endgate cover of a light-duty pickup truck by an automobile OEM.
The final designed charge length is formed by passing the extrudate through an inline cutting station. It then moves onto a heated conveyor that has a retractable canopy to help maintain the melt temperature of the material.
The charge is placed on the mold surface for final processing either robotically or manually, all while being synchronized to the molding cycle of a Dieffenbacher 2500-ton compression press.
Dieffenbacher LFT-D lines have been used by Teijin Automotive Technologies, a new business entity that encompasses the former Continental Structural Plastics, for twenty years.
While Teijin Automotive is largely recognised as a manufacturer of thermoset composite materials and molded components, LFT-D is steadily expanding in the construction, trucking, leisure, and automotive industries.
Despite LFT-reputation D's as a lightweight, semi-structural material, its use in exterior appearance applications has increased as a result of new process developments.
Sl no | Topic |
1 | Market Segmentation |
2 | Scope of the report |
3 | Abbreviations |
4 | Research Methodology |
5 | Executive Summary |
6 | Introduction |
7 | Insights from Industry stakeholders |
8 | Cost breakdown of Product by sub-components and average profit margin |
9 | Disruptive innovation in the Industry |
10 | Technology trends in the Industry |
11 | Consumer trends in the industry |
12 | Recent Production Milestones |
13 | Component Manufacturing in US, EU and China |
14 | COVID-19 impact on overall market |
15 | COVID-19 impact on Production of components |
16 | COVID-19 impact on Point of sale |
17 | Market Segmentation, Dynamics and Forecast by Geography, 2024-2030 |
18 | Market Segmentation, Dynamics and Forecast by Product Type, 2024-2030 |
19 | Market Segmentation, Dynamics and Forecast by Application, 2024-2030 |
20 | Market Segmentation, Dynamics and Forecast by End use, 2024-2030 |
21 | Product installation rate by OEM, 2023 |
22 | Incline/Decline in Average B-2-B selling price in past 5 years |
23 | Competition from substitute products |
24 | Gross margin and average profitability of suppliers |
25 | New product development in past 12 months |
26 | M&A in past 12 months |
27 | Growth strategy of leading players |
28 | Market share of vendors, 2023 |
29 | Company Profiles |
30 | Unmet needs and opportunity for new suppliers |
31 | Conclusion |
32 | Appendix |