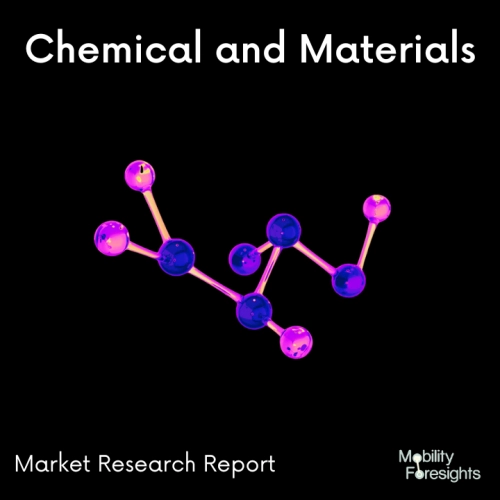
- Get in Touch with Us
Last Updated: Apr 25, 2025 | Study Period: 2024-2030
In order to maintain a firm connection between the electrode and the contacts of a lithium-ion battery (LIB), binder materials are in charge of holding the active material particles within the electrode together, fabrication of dry electrodes using a composite binder.
The use of a binder made of PTFE and a combination of PVDF, PEO, and CMC is covered by the patent. Dry electrode is a new idea and technology in the battery business that reinvents electrode production as a "powder to film" path.
The Global Dry Electrode Binder market accounted for $XX Billion in 2023 and is anticipated to reach $XX Billion by 2030, registering a CAGR of XX% from 2024 to 2030.
AM Batteries offers a dry electrode technology that has the ability to change the game in attaining these objectives with distinct steps towards mass production. The production of lithium-ion batteries must be done quickly and with high quality, which is a challenge if one wants to reach the requisite capacities and capabilities.
Complexity characterises the existing LIBs manufacturing standard. To sum up, the procedure starts with a slurry solution made by combining cathode (or anode) active powder, polymer binder, and conductive additives in a wet solvent.
This solution is then "poured" onto the current collectors to coat them. The combination undergoes multiple rounds of drying to get rid of the solvent, and then it goes through a lot of further processing to turn it into battery electrodes (calendering, slitting, vacuum drying, etc.).
However, the costs connected with wet-slurry coating, notably the drying of the N-Methylpyrrolidone (NMP) solvent, are by far the highest.
In addition to the solvent's intrinsic toxicity, which necessitates operational costs and safety risks that are equally resource-intensive, the capital investment is enormous and drying equipment may be up to 80 metres long. A vital component of the solution to reducing the price of lithium batteries is dry electrodes, one of many.
They at TDK Ventures have chosen to concentrate their strategy on this manufacturing element, especially dry-electrode technologies, because of the enormous potential these technologies offer to enhance and promote the shift to sustainable energy.
Sl no | Topic |
1 | Market Segmentation |
2 | Scope of the report |
3 | Abbreviations |
4 | Research Methodology |
5 | Executive Summary |
6 | Introdauction |
7 | Insights from Industry stakeholders |
8 | Cost breakdown of Product by sub-components and average profit margin |
9 | Disruptive innovation in theIndustry |
10 | Technology trends in the Industry |
11 | Consumer trends in the industry |
12 | Recent Production Milestones |
13 | Component Manufacturing in US, EU and China |
14 | COVID-19 impact on overall market |
15 | COVID-19 impact on Production of components |
16 | COVID-19 impact on Point of sale |
17 | Market Segmentation, Dynamics and Forecast by Geography, 2024-2030 |
18 | Market Segmentation, Dynamics and Forecast by Product Type, 2024-2030 |
19 | Market Segmentation, Dynamics and Forecast by Application, 2024-2030 |
20 | Market Segmentation, Dynamics and Forecast by End use, 2024-2030 |
21 | Product installation rate by OEM, 2023 |
22 | Incline/Decline in Average B-2-B selling price in past 5 years |
23 | Competition from substitute products |
24 | Gross margin and average profitability of suppliers |
25 | New product development in past 12 months |
26 | M&A in past 12 months |
27 | Growth strategy of leading players |
28 | Market share of vendors, 2023 |
29 | Company Profiles |
30 | Unmet needs and opportunity for new suppliers |
31 | Conclusion |
32 | Appendix |