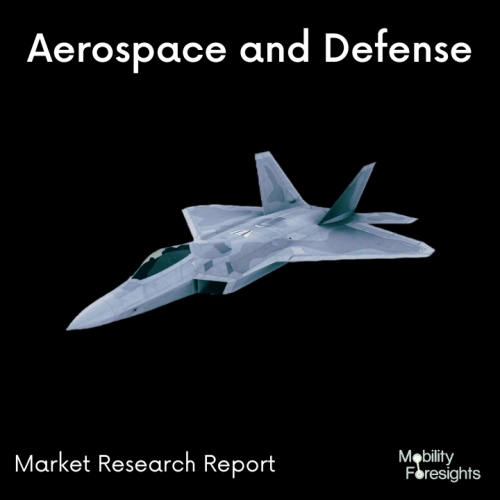
- Get in Touch with Us
Last Updated: Apr 25, 2025 | Study Period: 2024-2030
Increasing environmental awareness and expected growth in air traffic over the next decades drive the need for the development of new technologies in the aviation industry. To meet established emission and noise reductions, all-electric aircraft are a promising technology. Most concepts for electric aircraft components rely on fibre-reinforced polymer (FRP) composites to create load-bearing material.
As a result of its high strength-to-weight ratio and anti-corrosive characteristic, carbon fibre composites are widely employed in aerospace and aeronautical applications. When it comes to wing and fuselage construction, engine and fan components, and flooring and interior sections of aeroplanes, carbon fibre composite materials are frequently used. Its usage in aerospace applications is also being driven by advancements in carbon fibre composite manufacturing technologies.
Newest introductions include graphene nanoribbons films utilised in ice protection systems, as well as conductive composites with integrated conductive fibres like graphene and carbon nanotubes designed to transport lightning currents.
S No | Overview of Development | Development Detailing | Region of Development | Possible Future Outcomes |
1 | Bye Aerospace, L3Harris Technologies team develop all-electric multi-mission composite aircraft | global aerospace and defense company L3Harris Technologies (Melbourne, Fla., U.S.) and Bye Aerospace (Denver, Colo., U.S.) signed an agreement to develop an all-electric, multi-mission aircraft through modification of the recently announced eFlyer 800 to provide intelligence, surveillance and reconnaissance (ISR) capabilities for domestic and international ISR mission operators with composite materials. | USA | This would enhance better Technologies and Shuttle production |
2 | Toray to supply materials for all-electric aircraft | the all-electric, vertical take-off and landing aircraft could help increase regional air mobility, thus reducing traffic congestion, noise, and air pollution in crowded cities. The Lilium jet can take up to four passengers and its pilot up to 300 km in less than 60 minutes. Its fuselage, wings, rotor vanes, and other structural components will be made of carbon fibre composite materials | USA | This would enhance better Technologies and Shuttle production |
SI No | Timeline | Developments |
1 | Q2-2021 | GE Aviation and Safran S A are collaborating to develop composites, additive manufacturing and hybrid electric engines technologies for the CFM RISE (Revolutionary Innovation for Sustainable Engines) program to reduce CO2 emissions. |
2 | Q1-2021 | Bye Aerospace made a contract with Composite Universal Group(CUG) to assemble the composite materials and carbon fibers for eFlyer 2 electric aircraft's major components supplied by Toray Composite Materials America. |
3 | Q1-2021 | Composite One acquired the Process materials business from the Solvay composite materials global business and rebranded as Aerovac to become a leading manufacturer and supplier of advanced composite materials. |
4 | Q1-2021 | Europe funded in a SORCERER (Structural power composites for future civil aircraft) project by the collaboration between four European universities to develop multifunctional clever composite materials which carries the mechanical load as well as stores electrical energy to supply power for cabin and all required systems. |
In recent decades, the aircraft industry has shifted from using metals to using composites. In order to produce more fuel-efficient aircraft, manufacturers have turned to lighter, more efficient goods, which also support laws and changing views about aviation's influence on the environment, leading to an increase in the use of composites. Design, certification and manufacturing efficiencies as well as improvements in the cost and quality of production systems have been major facilitators in realising these potential and allowing the composite sector to grow.
Composites materials are critical to UK aerospace and to the industryâs future success in whole aircraft, aerostructures, propulsion and systems markets due their ability to provide high-quality solutions for a range of products. It is essential for the UK to understand future requirements and support development of technologies and enabling capabilities in composites.
High performance aircraft with long range point to point capabilities are also needed, both for wide body and narrow body aircraft alike In order to satisfy these demands, composites are essential It's possible that the UK's aerospace supply chain could benefit from new and updated platform development programmes across aircraft segments, and the UK's composites sector will play a key role in this by supplying high performance, smart mobility solutions for electric aircraft.
Materials composites are widely utilised in aeroplane interiors and exteriors. Composites' low weight and high-tensile strength enhance fuel economy and decrease maintenance costs, while also allowing OEMs to comply with the strict environmental requirements imposed in Europe and North America. Airframe constructions for new aircraft from major manufacturers like Boeing, such as their 787, 777X and A350XWB models, use a considerable proportion of carbon fibre composites (around 50% of structural weight).
The Global Electric Aircraft Composite Material market can be segmented into following categories for further analysis.
SI No | Timeline | Company | Developments |
1 | Q4-2021 | Eviation | Israel based electric aircraft startup Eviation unveiled its new commuter aircraft Alice, the plane is built with 95% composite materials and also with some innovative features, it will officially be available in 2023. |
2 | Q3-2021 | Toray Industries | Joby Aviation, an aerospace company from California backed by Uber, is partnered with Toray Industries for carbon fiber composite materials to implement fast and affordable electric aircraft. |
3 | Q3-2021 | Diamond Aircraft | Diamond Aircraft to develop an all electric airplane by converting its existing model DA40 series to battery powered, four seater, composite materials plane. |
4 | Q2-2021 | Bye Aerospace & L3Harris Technologies | Bye Aerospace is partnered with L3Harris Technologies to collaboratively develop an all electric aircraft eFlyer 800 with an agreement. The eFlyer 800 comes with a low profile and lightweight airframe uses advanced composite materials. |
In recent years, the interest in full or hybrid electric power for aeroplanes has risen as a result of the automobile industry and current mainstream developments in transportation. The interest in full or hybrid Batteries, according to several scientific and popular publications, offer a clean new world with low environmental impact.
There have been a number of envisioned applications planned over a controlled amount of scientific technologies and advancements. With the most recent technological development being in the usage of carbon fibre composites to give in better strength-to-weight ratio compared to aluminium alloys. It provisions the lowest possible airframe weight is of critical importance for an all-electric aircraft. As part of the MAXIM project, advanced and cost-effective materials and production solutions for large aerospace and automotive composite structures will be developed. A state-of-the-art carbon non-crimp fabric development machine and lab equipment for research into this technology will be installed at Hexcel's Leicester facility.
A key feature of the Advance motor design for the electric aircraft has been the CTI (carbon/titanium) fan blades, which will consume 20 percent less fuel while emitting 20 percent less CO2 compared to Trent engines of the first generation. The CTI fan blades and associated composite engine casings could reduce aircraft weight by up to 1,500lb per aircraft, which is the equivalent of carrying seven more passengers.
SI No | Timeline | Company | Developments |
1 | Q4-2021 | Toray Industries | Japan headquartered Toray Industries supplies advanced composite materials for aircrafts, automobile and aerospace has acquired prepreg business SK chemicals for 30 billion KRW. |
2 | Q1-2021 | Solvay Industries | Solvay Industries to supply composite and adhesive technologies for UK aerospace manufacturer Vertical Aerospace company's eVTOL flagship aircraft VA-1X, which is a passenger air-taxi programme of emission free flights. |
3 | Q1-2021 | Huntsman Corporation | Huntsman Corporation acquired Gabriel Performance Products, who specialised in the manufacture of chemicals, additives, adhesives and composites. |
4 | Q2-2021 | DuPont Solutions | DuPont Solutions set up a new adhesive manufacturing unit at East China with an investment of $30 million, the plant will produce Betatech, Betamate and Betaforce TC adhesive technologies for lightweight applications and vehicle electrification. |
Boeing, Airbus, and Bombardier have been using composite materials for decades, first in non-safety critical applications, and more recently in fundamental structures, such as fuselage and wing structures. As the aerospace market continues to grow, the UK composites industry has a number of possibilities to develop products and technology for existing and future platforms. Composite materials are becoming increasingly sophisticated and suitable for use in a wide range of aircraft applications.
Hexcel Corporation has been one of the pioneering companies in terms of its technological development towards better mobility of composite materials to have more construction capabilities and efficiencies. The most recent development has been Hexcel's Acousti-Cap technology in which a permeable cap material is individually embedded into each honeycomb cell to create an acoustic septum. This technology is a leading contributor to the reduction of the area of acceptable noise contour of the 737 MAX engine by 40% over the legacy 737 NG, without any weight penalty.
DuPont has also been part of the recent development in the field of composite materials-based aircraft propulsion requirements. It has brought in the DuPont⢠Nomex® and Kevlar® honeycomb composites and DuPont⢠Kevlar® fibre in other forms helps provide lightweight strength, stiffness, toughness, corrosion resistance and other attributes. Stiff, thin Nomex® sheet structures are used to help make strong, yet lightweight, honeycomb sandwich composite found in aircraft parts such flooring panels, interior walls, storage bins, exterior control surfaces, engine nacelles, and tail booms.
Sl no | Topic |
1 | Market Segmentation |
2 | Scope of the report |
3 | Abbreviations |
4 | Research Methodology |
5 | Executive Summary |
6 | Introduction |
7 | Insights from Industry stakeholders |
8 | Cost breakdown of Product by sub-components and average profit margin |
9 | Disruptive innovation in the Industry |
10 | Technology trends in the Industry |
11 | Consumer trends in the industry |
12 | Recent Production Milestones |
13 | Component Manufacturing in US, EU and China |
14 | COVID-19 impact on overall market |
15 | COVID-19 impact on Production of components |
16 | COVID-19 impact on Point of sale |
17 | Market Segmentation, Dynamics and Forecast by Geography, 2024-2030 |
18 | Market Segmentation, Dynamics and Forecast by Product Type, 2024-2030 |
19 | Market Segmentation, Dynamics and Forecast by Application, 2024-2030 |
20 | Market Segmentation, Dynamics and Forecast by End use, 2024-2030 |
21 | Product installation rate by OEM, 2023 |
22 | Incline/Decline in Average B-2-B selling price in past 5 years |
23 | Competition from substitute products |
24 | Gross margin and average profitability of suppliers |
25 | New product development in past 12 months |
26 | M&A in past 12 months |
27 | Growth strategy of leading players |
28 | Market share of vendors, 2023 |
29 | Company Profiles |
30 | Unmet needs and opportunity for new suppliers |
31 | Conclusion |
32 | Appendix |