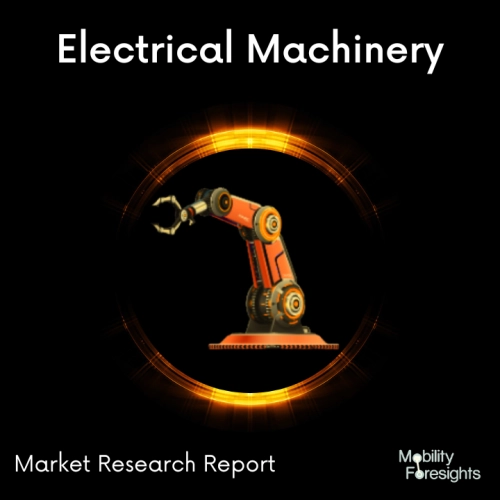
- Get in Touch with Us
Last Updated: Apr 25, 2025 | Study Period: 2023-2030
Thermal electric actuator, it is for remote control of system flow, heat (cold) device, suited for radiator, underfloor heating, and the temperature control of the central air conditioner, and the control of room temperature.
To regulate the closing and opening of pipes through manifold valves, electrothermal actuators are mostly utilised in underfloor heating systems.
It is utilised primarily in the electric drive section of the electrothermal actuator of the manifold branch valve, tiny valve, and dynamic balance valve.
Noiseless operation and a straightforward, rapid, and simple installation and disassembly process characterise the nut connection.
The Global Electric Thermal Actuator market accounted for $XX Billion in 2022 and is anticipated to reach $XX Billion by 2030, registering a CAGR of XX% from 2023 to 2030.
The developments in deep X-ray lithography allowed for the creation of miniature electric thermal actuators. The balance between the thermal energy produced by an electrical current and the heat dissipation through the surroundings or the substrate is the foundation of electrothermal actuation.
The hot-and-cold-arm, chevron, and bimorph designs are the three traditional forms of electrothermal actuators covered in this article. Electrothermal actuators can be made using simple fabrication techniques that are compatible with Integrated Circuits (IC) and MEMS production processes.
The majority of actuators work within the typical IC voltage range, making it simple to integrate electrothermal actuators with IC devices and use them in the same fabrication process.
Additionally, sensory feedback is applied for regulated operation.The electrothermal actuators are a valuable component for MEMS because Electrothermal actuators can potentially create significant forces and displacements while using a relatively low driving voltage.
Electrothermal actuators can be used in a variety of environments, including air, vacuum, dusty environments, liquid media, and SEM electron beam environments (scanning electron microscopy).
However, because of the lengthy time constants of the thermal processes, these actuators typically exhibit slow switching speeds. However, it was also shown that high-frequency thermal actuation was viable.
For resonance mode actuation in microcantilever-based sensing and probing applications, the electrothermal excitation approach has also grown in popularity.
These MEMS resonators have demonstrated a high quality factor and a broad tuning frequency range. For force feedback, electrothermal actuation is simply coupled with a piezoresistive or piezoelectric sensor.
Sl no | Topic |
1 | Market Segmentation |
2 | Scope of the report |
3 | Abbreviations |
4 | Research Methodology |
5 | Executive Summary |
6 | Introduction |
7 | Insights from Industry stakeholders |
8 | Cost breakdown of Product by sub-components and average profit margin |
9 | Disruptive innovation in the Industry |
10 | Technology trends in the Industry |
11 | Consumer trends in the industry |
12 | Recent Production Milestones |
13 | Component Manufacturing in US, EU and China |
14 | COVID-19 impact on overall market |
15 | COVID-19 impact on Production of components |
16 | COVID-19 impact on Point of sale |
17 | Market Segmentation, Dynamics and Forecast by Geography, 2023-2030 |
18 | Market Segmentation, Dynamics and Forecast by Product Type, 2023-2030 |
19 | Market Segmentation, Dynamics and Forecast by Application, 2023-2030 |
20 | Market Segmentation, Dynamics and Forecast by End use, 2023-2030 |
21 | Product installation rate by OEM, 2023 |
22 | Incline/Decline in Average B-2-B selling price in past 5 years |
23 | Competition from substitute products |
24 | Gross margin and average profitability of suppliers |
25 | New product development in past 12 months |
26 | M&A in past 12 months |
27 | Growth strategy of leading players |
28 | Market share of vendors, 2023 |
29 | Company Profiles |
30 | Unmet needs and opportunity for new suppliers |
31 | Conclusion |
32 | Appendix |