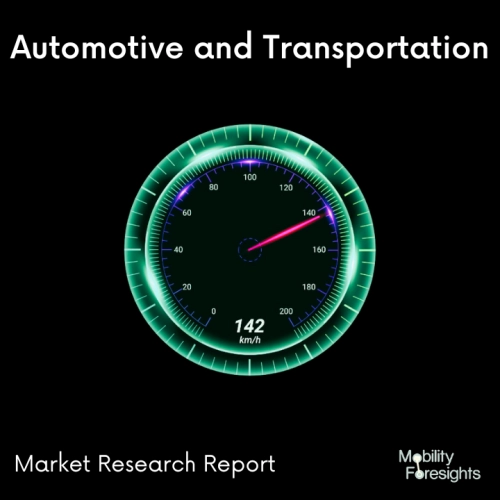
- Get in Touch with Us
Last Updated: Apr 25, 2025 | Study Period: 2024-2030
A vehicle is made up of around 39 different types of basic plastics and polymers. Polypropylene, polyurethane, polyamides, and PVC account for more than 70% of the plastic used in vehicles. In recent years, plastic has become one of the most important elements required for the structure, performance, and safety of cars.
EV Plastics are focused upon the better aimed approach of having the light weighting and mechanical efficiency across the various specifications analysed and enhanced at various points of time within the Electric vehicles at all times.
Since their inception, plastic materials have been used to replace rare and non-renewable resources such as tortoise shell, ivory, and animal bones. Plastics have altered the globe since then, giving safety, hygiene, comfort, and well-being to our civilization.
Today, resource-efficient plastics can be found in an almost limitless number of goods and uses, allowing us to conserve energy, CO2 emissions, water, and even food.They contribute to circularity, health and safety, and climate change mitigation. Without a question, plastics have influenced our lives and will continue to do so in the future.
S No | Overview of Development | Development Detailing | Region of Development | Possible Future Outcomes |
1 | ZUV Electric involved in first of its kind 3D printed plastic based tricycle manufacturing | EOOS has developed a prototype for a "zero-emissions utility vehicle", or ZUV, which can be 3D-printed locally rather than having to be shipped around the world. The tricycle is made from 70 kilograms of plastic packaging waste sourced from supermarkets. | USA | This would enhance better EV Technologies and production |
2 | Fisker Inc. has made its paving way into the EV plastics integration into interiors of EVs | It has launched most recently, The fully electric Ocean SUV gets its name from the use of recycled plastics throughout the vehicle's interior. Most of the interior materials are made from plastic waste collected from the ocean that would otherwise become pollution and hazards for marine life, including plastic bottles and fishing nets. | USA | This would help in better presence and social responsibility on increased levels of requirements |
3 | Solvay has recently launched the technologically advanced plastics into varied levels of EV Integrations | Solvay has launched a new grade of KetaSpire PEEK (polyetheretherketone), KT-850 SCF 30, for precision brake system and e-mobility electronic pump components. The new KT-850 SCF 30 grade enables further metal replacement by improving the flow characteristics of the material and the surface finish of parts. | EU | This would improve its presence and production capability of new generation plastic usability system |
Since the 1950s, plastics have offered lightweight, affordable solutions for both aesthetic and structural automotive applications, in some cases replacing steel as the material of choice in automobile engineering and construction. In recent years, the rise in plastic use has been driven by fuel efficiency trends and, as a result, decreased greenhouse gas emissions.
Plastics' high absorption qualities also allow the vehicle to satisfy tighter safety requirements, while the use of engineering plastics allows for the reduction of the bulk of parts used in cars due to their greater design flexibility. When analysing the automotive forecast and related polymer demand, the advent and quick expansion of electrically driven road cars has become a crucial topic to address.
While the global total number of electric vehicles (EVs) remains modest, vehicle fleet electrification has gained significant traction in recent years.
The recent growth in use of plastics such as polypropylene (PP) and polyurethane (PU) has been somewhat countered by the reduction in consumption of engineering plastics, with PP and PU accounting for almost half of overall plastic consumption in cars.
Engineering plastics consumption is anticipated to drop due to a lower need for these plastics in under-the-hood applications for electric cars, since high temperature resistance of engineering polymers is not required to the same extent as with internal combustion engines. Instead, polyamides will be utilised in EV battery mounts and housings.
The Global Electric Vehicle Plastics Market can be segmented into following categories for further analysis.
EVs need to be covered and casted as required within the requirements of the transitions efficiency and mechanical efforts to have better properties emerged as part of EV adaptability being to the highest with a proper EV plastic integrated into the EV as required within the various components.
The most recent technological addition into the EV sector has been the Carbon Reinforced Plastics being added into the varied levels of components of EVs around the global market of operations.
This material is 30 percent to 50 percent lighter than glass and metal, and is even more durable in some cases, making cars more efficient.
In the most recent move, US Department of Energy has proposed that for every 10% weight reduction in a vehicle increases fuel efficiency by 8%, potentially saving consumers $5,000 in gasoline over the life of the vehicle. Lighter cars have a greater range between charges with EVs.
There has been a rather broader perspective of operational plastics integrated into the EVs within the Battery management systems ( BMS ) to have better efficiency and technical specifications improvised.
The plastic honeycombs used for crumple zones are now keeping batteries safe in EVs, which have more vulnerable impact absorption characteristics. In comparison to humans, which can withstand a gravitational force (G force) of 80, electric batteries can only withstand a G force of 60, making polymers essential for the long-term viability of costly batteries.
Plastic's position in automotive vehicle design and manufacture has never been more important, with rigorous laws and changing consumer habits driving demand for more cheap, lightweight, and fuel-efficient automobiles. Fuel efficiency has become one of the most important features in electric vehicle design due to the rising fuel prices and stricter environmental regulations.
Reliant Plastics has been one of the major leaders in the electric vehicle plastics considering their high resistance and light weighting-based design emphasis in the electric vehicle design analysis and integration. It has recently brought upon the Advanced Composites into action within the industry at varied levels and component requirements.
Due to its high heat tolerance (in excess of 300° Celsius) and chemical resistance and inherent lubricity, it is an ideal resin for lighter-weight components that would typically be made of metal.
BASF has also been working upon the various requirements of EV based specific plastics to be brought into complete intervention in the global market for better adaptability. It has recently introduced new product requirements under the plastics technology for EVs. The moulding compounds are available unreinforced, reinforced with glass fibres or minerals and also reinforced with long-glass fibres for special applications. Ultramid is noted for its high mechanical strength, stiffness, and thermal stability.
In addition, Ultramid offers good toughness at low temperatures, favourable sliding friction behaviour and can be processed without any problems.
A brand-new "EVOLVE" product range of plastics for electric vehicles has been created by Dow Technologies. The thermoplastic elastomers (TPEs), engineering plastics, and adhesive products in the EVOLVE product series have been created especially for usage in electric vehicles.
The advantages of EVOLVE TPEs for internal parts like instrument panels, door trims, and dashboard covers include increased sturdiness, improved weatherability, and improved haptics. Additionally, because of these materials' high degree of adaptability, producers can modify certain aspects of their performance and design.
A variety of engineering polymers, such as polycarbonates, polyamides, and polyesters, which give excellent strength, rigidity, and heat protection, are also part of the EVOLVE product line in addition to TPEs.
These components, including battery casings, electric motors, and power circuitry, are perfect candidates for use with these materials as structural elements. Dow Technologies has also created a variety of adhesive solutions, such as two-part epoxies and acrylics, as well as hot-melt adhesives, to guarantee trustworthy adhesion between these plastic components.
The surfaces that these products adhere to well include metals, other polymers, and composites. Overall, the Dow Technologies EVOLVE product line provides a full range of options for businesses seeking to develop and create outstanding performance plastics parts for electric vehicles.
Under the brand name "Thermylene," Asahi Kasei, a well-known international chemical firm, provides a variety of high-performance plastics for EVs. Thermodynamics, weight reduction, and safety are just a few of the particular demands that these materials are made to satisfy for EVs.
Thermylene P11, a high-performance polypropylene (PP) resin with exceptional heat protection, little warpage, and decent flowability, is one of the main items in the Thermylene line-up. Battery containers, connections, and junction boxes are just a few of the EV parts that use this substance.
Thermylene P9, a glass-reinforced PP resin with high stiffness and strength and great heat protection, is another crucial substance. This substance is frequently found in EV battery cells, where it aids in weight reduction and enhances temperature control.
Under the Thermylene name, Asahi Kasei also provides a variety of other materials, such as polyphenylene oxide (PPO) and polyamide (PA) polymers, which provide excellent heat resistance and dimensional stability as well as excellent chemical resistance and durability.
Asahi Kasei's Thermylene brand offers a variety of high-performance plastics that are appropriate for the particular needs of electric vehicles, assisting to lighten the vehicle's load, better thermal control, and increase protection.
Sl no | Topic |
1 | Market Segmentation |
2 | Scope of the report |
3 | Abbreviations |
4 | Research Methodology |
5 | Executive Summary |
6 | Introduction |
7 | Insights from Industry stakeholders |
8 | Cost breakdown of Product by sub-components and average profit margin |
9 | Disruptive innovation in the Industry |
10 | Technology trends in the Industry |
11 | Consumer trends in the industry |
12 | Recent Production Milestones |
13 | Component Manufacturing in US, EU and China |
14 | COVID-19 impact on overall market |
15 | COVID-19 impact on Production of components |
16 | COVID-19 impact on Point of sale |
17 | Market Segmentation, Dynamics and Forecast by Geography, 2024-2030 |
18 | Market Segmentation, Dynamics and Forecast by Product Type, 2024-2030 |
19 | Market Segmentation, Dynamics and Forecast by Application, 2024-2030 |
20 | Market Segmentation, Dynamics and Forecast by End use, 2024-2030 |
21 | Product installation rate by OEM, 2023 |
22 | Incline/Decline in Average B-2-B selling price in past 5 years |
23 | Competition from substitute products |
24 | Gross margin and average profitability of suppliers |
25 | New product development in past 12 months |
26 | M&A in past 12 months |
27 | Growth strategy of leading players |
28 | Market share of vendors, 2023 |
29 | Company Profiles |
30 | Unmet needs and opportunity for new suppliers |
31 | Conclusion |
32 | Appendix |