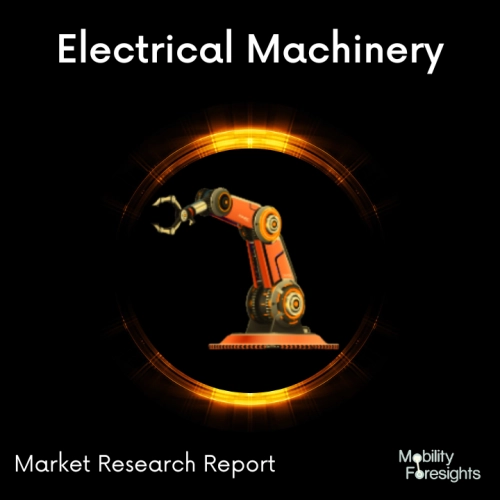
- Get in Touch with Us
Last Updated: Apr 25, 2025 | Study Period: 2024-2030
An incredibly tiny pump called the Electro-Osmotic Pump (EO pump) uses electroendosmosis. Because it has no mechanically moving parts, neither pulsation nor operating noise are produced when it is in use.
In a family of pumps known as electroosmotic pumps (EOPs), fluid is forced through a capillary or other porous medium while being subjected to an electric field.
The discovery of novel materials with high electroosmotic flow rates at low voltages is the focus of current EOP research.
A basic electrokinetic process known as electroosmosis involves the movement of a bulk solution up against a charged solid surface while being affected by an electric field.
Due to the deprotonation of silanol groups in the case of CE, the capillary inner wall typically bears negative charges.
The Global Electro-osmotic Micropump market accounted for $XX Billion in 2023 and is anticipated to reach $XX Billion by 2030, registering a CAGR of XX% from 2024 to 2030.
It is demonstrated that a high-pressure electro-osmotic (EO) micro-pump made using the sol-gel method may be useful as a fluid-driving component for chip-scale analytical systems.
Within the 100 m inner diameter (i.d.) fused-silica capillary of the micro-pump, a silica monolithic matrix with a morphology of micron-scaled through pores was created.
Due to the monolith's direct capillary wall connection, frits with significant pressure loss are not required. With no mechanical parts, this pump propels liquid solution using electro-osmotic flow.
The cathode chamber's Nafion housing design maximises pressure build-up by preventing flow leakage into the electrode reservoir from the flow channel.
Additionally, it removes electrolytic bubble interference from the flow channels while simultaneously supplying ionic channels for current penetration.
Since the monolith is made of silica, it can withstand swelling and shrinking issues when employed with a variety of fluids, especially organic solvents like acetonitrile and methanol.
For deionized water at 6 kV applied voltage, the 100 m i.d. monolithic pump can provide a maximum flow rate and pressure of 2.9 L/min and 3 atm, respectively.
These findings suggest that the pump is capable of delivering the necessary pressure and flow for micro- and miniature total-analysis systems (TAS).
The data for various operating fluids and voltages are collapsed using a straightforward universal pressure pump curve.
Sl no | Topic |
1 | Market Segmentation |
2 | Scope of the report |
3 | Abbreviations |
4 | Research Methodology |
5 | Executive Summary |
6 | Introduction |
7 | Insights from Industry stakeholders |
8 | Cost breakdown of Product by sub-components and average profit margin |
9 | Disruptive innovation in the Industry |
10 | Technology trends in the Industry |
11 | Consumer trends in the industry |
12 | Recent Production Milestones |
13 | Component Manufacturing in US, EU and China |
14 | COVID-19 impact on overall market |
15 | COVID-19 impact on Production of components |
16 | COVID-19 impact on Point of sale |
17 | Market Segmentation, Dynamics and Forecast by Geography, 2024-2030 |
18 | Market Segmentation, Dynamics and Forecast by Product Type, 2024-2030 |
19 | Market Segmentation, Dynamics and Forecast by Application, 2024-2030 |
20 | Market Segmentation, Dynamics and Forecast by End use, 2024-2030 |
21 | Product installation rate by OEM, 2023 |
22 | Incline/Decline in Average B-2-B selling price in past 5 years |
23 | Competition from substitute products |
24 | Gross margin and average profitability of suppliers |
25 | New product development in past 12 months |
26 | M&A in past 12 months |
27 | Growth strategy of leading players |
28 | Market share of vendors, 2023 |
29 | Company Profiles |
30 | Unmet needs and opportunity for new suppliers |
31 | Conclusion |
32 | Appendix |