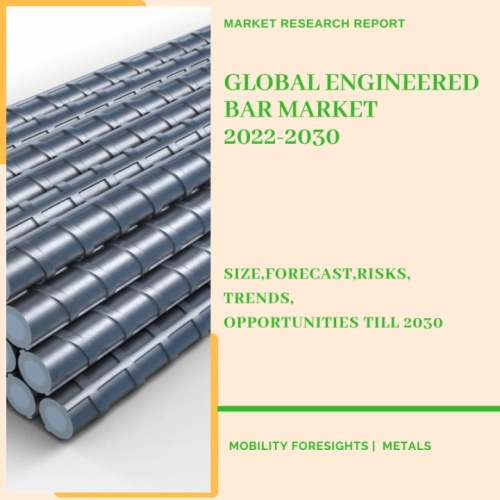
- Get in Touch with Us
Last Updated: Apr 26, 2025 | Study Period: 2022-2030
Engineered bar products are produced in cutting-edge steel facilities and put through thorough testing to ensure they surpass industry standards for quality and fulfil customers' exact specifications. They are designed for the most demanding applications.
Vacuum degassing can be used to increase cleanliness by removing hydrogen, oxygen, and nitrogen, ensure steel is produced to consistent and narrow chemical specification ranges, improve capability to produce low-carbon grades, and improve temperature control during continuous casting, depending on the needs of the customer for engineered bars.
The ladles are brought to the continuous caster after refinement and alloying, where the molten steel runs through a ceramic tube while being encased in argon gas to maintain cleanliness.
Cold-finish processing could be necessary when strength, dimension, and surface are crucial.
The Global engineered bar market accounted for $XX Billion in 2021 and is anticipated to reach $XX Billion by 2030, registering a CAGR of XX% from 2022 to 2030.
The Board of Directors of Nucor Corporation recently gave the go-ahead for a project to modernise the company's engineered bar mill in Nebraska so that it may better serve the automotive industry and continue to satisfy the demands of its customers for the highest-quality goods.
A new reheat furnace, a new intermediate mill, and a coil inspection and trimming station are all part of the renovation project.
This investment will strengthen Nucor's position as a market leader in engineered bar and rod and is a part of their larger commercial strategy to align their product mix with customer demand now and in the future.
When these improvements are finished, Nucor Steel Nebraska will be better able to produce engineered bars and coils with better surface quality and less decarburization, which are needed to satisfy high-end engineered bar automotive applications.
Sl no | Topic |
1 | Market Segmentation |
2 | Scope of the report |
3 | Abbreviations |
4 | Research Methodology |
5 | Executive Summary |
6 | Introduction |
7 | Insights from Industry stakeholders |
8 | Cost breakdown of Product by sub-components and average profit margin |
9 | Disruptive innovation in the Industry |
10 | Technology trends in the Industry |
11 | Consumer trends in the industry |
12 | Recent Production Milestones |
13 | Component Manufacturing in US, EU and China |
14 | COVID-19 impact on overall market |
15 | COVID-19 impact on Production of components |
16 | COVID-19 impact on Point of sale |
17 | Market Segmentation, Dynamics and Forecast by Geography, 2022-2030 |
18 | Market Segmentation, Dynamics and Forecast by Product Type, 2022-2030 |
19 | Market Segmentation, Dynamics and Forecast by Application, 2022-2030 |
20 | Market Segmentation, Dynamics and Forecast by End use, 2022-2030 |
21 | Product installation rate by OEM, 2022 |
22 | Incline/Decline in Average B-2-B selling price in past 5 years |
23 | Competition from substitute products |
24 | Gross margin and average profitability of suppliers |
25 | New product development in past 12 months |
26 | M&A in past 12 months |
27 | Growth strategy of leading players |
28 | Market share of vendors, 2022 |
29 | Company Profiles |
30 | Unmet needs and opportunity for new suppliers |
31 | Conclusion |
32 | Appendix |