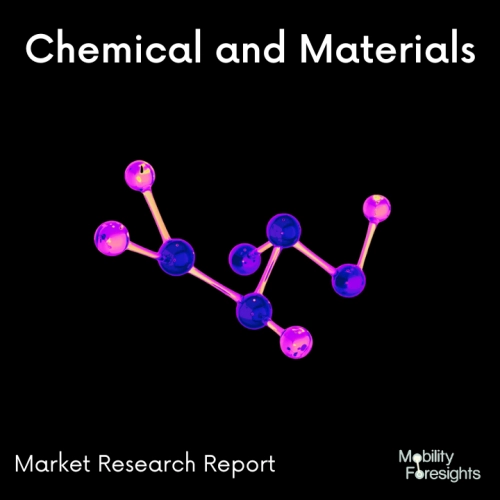
- Get in Touch with Us
Last Updated: Apr 25, 2025 | Study Period: 2024-2030
A form of protective coating known as epoxy asphalt coating blends epoxy resin with asphalt components. In order to offer a long-lasting and high-performing surface for roads, bridges, parking lots, and other transportation applications, it is largely employed in infrastructure and construction projects.
The following steps are commonly included in the epoxy asphalt coating process:
Surface cleaning: To ensure appropriate adhesion of the coating, the substrate, such as a concrete or asphalt surface, is cleaned and prepped. This can entail clearing away any loose objects, filling in any holes or fractures, and smoothing down the surface.
Application of epoxy resin: The prepared surface is covered with a primer layer of epoxy resin. The successive layers adhere better thanks to the primer's aid in bonding.
Preparation of the asphalt mixture: A hot mix asphalt (HMA) or warm mix asphalt (WMA) formulation is made by heating the asphalt and mixing it with aggregates and other ingredients. Depending on the project requirements and the environment, the precise mixture composition may change.
Application of epoxy asphalt coating: Before applying the hot or warm asphalt mixture, the prepared epoxy resin is spread over the primer layer. By serving as a binder, the epoxy resin improves the cohesion and adherence of the asphalt layers.
Compaction and curing: To attain the required density and smoothness, the coated surface is compressed using rollers or other compaction equipment. The epoxy resin goes through a chemical process called curing that makes the coating stronger and harder.
The advantages of epoxy asphalt coating are as follows:
Epoxy asphalt coatings offer great resistance to high traffic volumes, UV rays, chemicals, and abrasion. They can survive extreme weather, temperature changes, and mechanical pressures, extending the coated surface's useful life.
Improved adhesion: The epoxy resin in the coating strengthens the bond between the asphalt layers and the substrate, lowering the chance of delamination and boosting structural integrity all around.
Epoxy asphalt coatings aid to provide a barrier that helps stop water infiltration, shielding the underlying structure from moisture-related damage such as cracking, spalling, and corrosion.
The surface that is smooth and even: Epoxy asphalt coatings help create a surface that is smooth and level, decreasing friction and enhancing vehicle ride quality. They can also lessen noise levels brought on by tire contact with the road.
Epoxy asphalt coatings may be applied effectively, enabling quicker project completion. Quick installation and maintenance. They also need little maintenance during their lifetime, which saves money and minimizes downtime for repairs.
Epoxy asphalt coatings are frequently used on heavy-duty surfaces including roads, airport runways, ports, and industrial buildings where a dependable and long-lasting surface is needed. They provide a practical way to increase the lifespan of current infrastructure or build new surfaces with better performance qualities.
The Global Epoxy Asphalt Coating Market accounted for $XX Billion in 2023 and is anticipated to reach $XX Billion by 2030, registering a CAGR of XX% from 2024 to 2030.
Coating Materials for waterborne, high solids, UV/EB, and powder formulations are available from Arkema in a variety of forms. The Company will address continuing activities focusing on sustainability, legal compliance, improved performance, new uses, and much more while introducing a number of new products.
Arkema Among the initiatives on the show are:
Using CELOCOR® AF opaque polymers and ENCOR® 317 vinyl acrylic resin to lessen the reliance on TiO2 in decorative paints.
Using SYNAQUA® 4856 alkyd, SYNAQUA® 4804 alkyd, COAPUR® HEUR thickeners, CRAYVALLAC® additives, and SARTOMER® Serbia UV Specialty resins, the usage of biobased content can be increased.
Utilizing PVDF resins from Kynar Aquatec® to meet SSPC Paint 47 Standards
Using a broad toolkit of SYNOCURE® acrylic polyols and NISO products, SYNOLAC® alkyds and polyesters, CRAYAMID® reactive polyamides, SYNAQUA® and ENCOR® waterborne solutions, and UNITHANE® modified alkyds, protective and marine coatings can be made more durable and have their VOC levels reduced.
Sl no | Topic |
1 | Market Segmentation |
2 | Scope of the report |
3 | Abbreviations |
4 | Research Methodology |
5 | Executive Summary |
6 | Introduction |
7 | Insights from Industry stakeholders |
8 | Cost breakdown of Product by sub-components and average profit margin |
9 | Disruptive innovation in the Industry |
10 | Technology trends in the Industry |
11 | Consumer trends in the industry |
12 | Recent Production Milestones |
13 | Component Manufacturing in US, EU and China |
14 | COVID-19 impact on overall market |
15 | COVID-19 impact on Production of components |
16 | COVID-19 impact on Point of sale |
17 | Market Segmentation, Dynamics and Forecast by Geography, 2024-2030 |
18 | Market Segmentation, Dynamics and Forecast by Product Type, 2024-2030 |
19 | Market Segmentation, Dynamics and Forecast by Application, 2024-2030 |
20 | Market Segmentation, Dynamics and Forecast by End use, 2024-2030 |
21 | Product installation rate by OEM, 2023 |
22 | Incline/Decline in Average B-2-B selling price in past 5 years |
23 | Competition from substitute products |
24 | Gross margin and average profitability of suppliers |
25 | New product development in past 12 months |
26 | M&A in past 12 months |
27 | Growth strategy of leading players |
28 | Market share of vendors, 2023 |
29 | Company Profiles |
30 | Unmet needs and opportunity for new suppliers |
31 | Conclusion |
32 | Appendix |