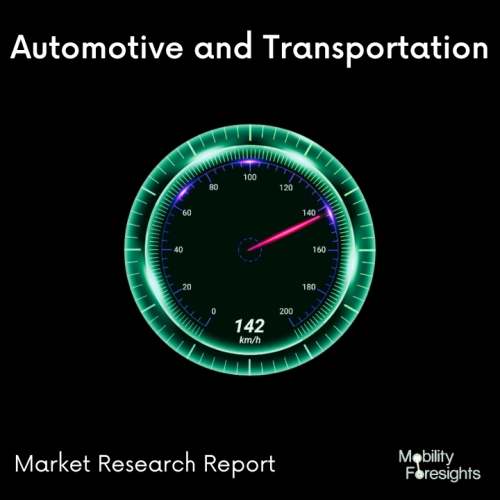
- Get in Touch with Us
Last Updated: Apr 25, 2025 | Study Period: 2024-2030
Composites in the automotive industry are made up of two or more materials that have differing qualities. Because the constituent elements in an automobile composite are unique and do not combine, they are not considered mixes or solutions. The attributes of a composite comprising two components are commonly better than the independent materials' characteristics.
The Europe Automotive Composites Market employs polymeric materials, which offer weight savings while retaining other desirable characteristics such as structural rigidity.Polymeric materials frequently use non-renewable sources such as petroleum and require a lot of energy to manufacture.
S No | Overview of Development | Development Detailing | Region of Development | Possible Future Outcomes |
1 | Kordsa expands to the Europe Automotive Composites market with new composite technologies investment | Microtex Composites Srl is acquired by Kordsa, adding super-luxury automobile and racing to its portfolio. | Europe | This would enhance better Technological Controls |
2 | Tenneco introduces advanced hybrid friction material composites for OE customers | To address evolving powertrain needs, an innovative composite material combines braking performance and comfort into a single idea. | Europe | This would enhance better Technological Controls |
3 | Teijin to acquire Benet Automotive to expand European automotive business | Teijin Limited has agreed to buy Benet Automotive s.r.o. (Benet), a major Czech automotive composite and component provider. | Europe | This would enhance better Technological Controls |
4 | EU Companies Collaborate to Bring Next-Gen Composites to E-Mobility Sector | The commercial development of medium-volume niche applications based on advanced composites will be the focus of German consultancy AMAC and Holland's PontisEngineering. | Europe | This would enhance better Technological Controls |
5 | Teijin Automotive Technologies Expanding Composites Footprint in China to Meet Growing Demand for EVs | Teijin Automotive Technologies is aggressively expanding its position as a global leader in automotive composite applications with the start-up of the second plant and the development of the third facility. | Europe | This would enhance better Technological Controls |
The European automotive Composites Market was valued at $XX Billion in 2023 and is projected to reach $XX Billion by 2030, reflecting a compound annual growth rate (CAGR) of XX% from 2024 to 2030.
Teijin Ltd., a Tokyo-based chemical corporation, is buying Inapal Plasticos SA, a Portuguese automotive composite supplier, following other recent automotive-related acquisitions. Teijin Holdings Netherlands B.V., the Teijin Group's holding company in the Netherlands, will purchase Inapal's shares.
The deal's details have not been revealed. Inapal is a Tier One provider of composite components to the automotive and heavy truck industries, with headquarters in Leca do Balio, Porto, Portugal. Class A body panels, structural, and underbody components are among the company's capabilities, which include sheet molding compound (SMC), carbon fiber SMC, pre-preg compression molding (PCM), direct long fiber thermoplastic (D-LFT), and glass mat thermoplastic (GMT).
Jaguar, Land Rover, BMW, Mercedes, Volkswagen, and Bentley are among the European OEM clients served by the company's two manufacturing centers in Portugal.
Inapal also offers components to the heating and cooling industry, as well as passenger seating components to the bus and rail industries, in addition to its automotive and heavy truck operations. Theybecame a Tier One provider of high-performance composites to the worldwide automotive sector after acquiring Continental Structural Plastics in Michigan.Now that we've acquired Inapal, we'll be able to keep our commitment to stakeholders and grow our technology globally, particularly in Europe.
New Epoxy Resin System for SMC Manufacturing of Automotive Composites Introduced by Hexion Inc. The new product, EPIKOTE TM Resin TRAC 06605/EPIKURETM Curing Agent TRAC 06608, can be utilized to create lightweight semi-structural and structural automotive composite parts, including floors, electrical vehicle battery enclosures, spare wheel tubs, seat structures, hood inners, and more.
When coupled with glass and carbon fibers, Hexion's SMC epoxy system produces parts with superior mechanical qualities to those created with conventional unsaturated polyester (UP) or vinyl ester (VE) SMC resin systems.According to VDA 278, Hexion's epoxy SMC system produces much fewer volatile organic compounds (VOCs) than either standard or low VOC vinyl esters, with emissions considerably below global exposure guidelines.
Organic emissions for molded compounds in automobiles are governed by the VDA 278 recommendation. To meet European working standards, there is no need to monitor worker styrene exposure because Hexion's epoxy SMC system is styrene-free.Additional capital investment is frequently not necessary because the new epoxy system is compatible with tools used for other types of SMC (UP and VE).
"This new specialty epoxy product line will help their customers manufacture high-performance composite parts via high-volume SMC production with reduced scrap and relatively low labor costs.It completes the whole range of compression molding products, which also includes resin transfer molding (RTM), liquid compression molding (LCM), and prepreg molding.
The manufacture of more automobiles and the rising demand for lightweight materials to increase fuel efficiency and cut greenhouse gas emissions are the main development drivers for this industry.New regulations established by the European Union mandate that light commercial vehicles must achieve CO2 emissions targets of 147 g/km, or 43.3 mpg, for light trucks, and 95 g/km for passenger cars.
Incorporating lightweight materials, such as composites, is greatly aided by the European Commission's plan to raise the region's fuel economy regulations.
The market penetration of thermoplastic and carbon composites is rising, and these new trends have a direct impact on the dynamics of the sector. The most significant resin type categories in the European automotive composites market include polypropylene (PP) composites, polybutylene terephthalate (PBT) composites, polyamide (PA) composites, vinyl ester composites, polyester composites, phenolic composites, and others.
By value and volume of consumption, PP composites are anticipated to maintain their dominance. The attributes that drive the demand for PA composites in the automotive industry include high resistance to abrasion, low friction properties, electrical resistance, heat resistance, and superior chemical resistance. Glass fiber composites are anticipated to continue to be the most popular type of fiber in composites; however, carbon fiber composites are anticipated to expand at the fastest rate during the anticipated time frame.
Polymer nanocomposites, like thermoplastic polymers and strengthened glass, have gained importance in recent years for automakers, prompting them to seek out better, stronger, and lightweight elements for the production of vehicle units.The market is likely to be driven by factors such as rising demand for lightweight materials from the automobile sector and a growing focus on fuel efficiency.
The high cost of carbon fiber composites and glass fiber combinations, on the other hand, is impeding market expansion. The use of such composites in low-cost automobiles might dramatically raise their pricing. Toray Industries Inc. is a prominent developer of the latest integrated technologies focusing on better smarter composites focused on the spectrum of automotive improvisation integration for the future.
The Thermoplastic elastomer solutions provide high-performance automotive applications in a variety of forms to fit your design demands and processing possibilities.Toray Amber Tool epoxy manufacturing prepregs are indeed the mainstream technology, with an unparalleled reputation for dependability and a superb aesthetic surface finish.
Exel Composites provides technical breakthroughs that allow the diagnostic of unwanted accidental instances wherein the technology of Drying formworks may be made using the HiTape in a completely automated lay-up, analogous to the AFP and ATL techniques often used for UD prepregs.
HiTapenarrow breadth accuracy offers it complete control over the automated dry prototype process â and that's a waste-free procedure, even for complicated constructions, because the components are precisely positioned where they're needed.It has a very high Compression After Impact (CAI) efficiency, which is a true advance in unidirectional graphene-reinforcing infusion methods.
1 | Market Segmentation |
2 | Scope of the report |
3 | Abbreviations |
4 | Research Methodology |
5 | Executive Summary |
6 | Introduction |
7 | Insights from Industry stakeholders |
8 | Cost breakdown of Product by sub-components and average profit margin |
9 | Disruptive innovation in theIndustry |
10 | Technology trends in the Industry |
11 | Consumer trends in the industry |
12 | Recent Production Milestones |
13 | Component Manufacturing in US, EU and China |
14 | COVID-19 impact on overall market |
15 | COVID-19 impact on Production of components |
16 | COVID-19 impact on Point of sale |
17 | Market Segmentation, Dynamics and Forecast by Geography, 2024-2030 |
18 | Market Segmentation, Dynamics and Forecast by Product Type, 2024-2030 |
19 | Market Segmentation, Dynamics and Forecast by Application, 2024-2030 |
20 | Market Segmentation, Dynamics and Forecast by End use, 2024-2030 |
21 | Product installation rate by OEM, 2023 |
22 | Incline/Decline in Average B-2-B selling price in past 5 years |
23 | Competition from substitute products |
24 | Gross margin and average profitability of suppliers |
25 | New product development in past 12 months |
26 | M&A in past 12 months |
27 | Growth strategy of leading players |
28 | Market share of vendors, 2023 |
29 | Company Profiles |
30 | Unmet needs and opportunity for new suppliers |
31 | Conclusion |
32 | Appendix |