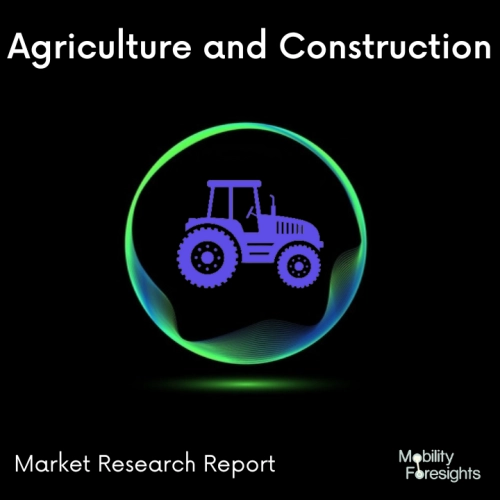
- Get in Touch with Us
Last Updated: Apr 25, 2025 | Study Period: 2024-2030
The European Cement industry accounted for xx Metric tons/year of cement capacity with production of cement ranging from xx Metric tons/year in 2019 and is further forecasted to reach about xx Mt/year by 2025 at a CAGR of xx%.
Cement is obtained by grinding cement clinker and, in some cases, supplementing it with additions. Spain, Italy, Germany, France and Poland are the largest producers of cement clinkers in the EU.Before the pandemic, the industry was not operating at full capacity; with the global economic slowdown, plants were expected to see further drops in utilization rates. While companies are likely to finish committed expansions that were delayed due to lockdowns, and start new projects beyond 2021 depending on the pace of economic recovery.
As countries began to reopen post-pandemic, consumption of cement and concrete is expected to gradually recover, fueled by economic growth, urbanization, and population growth, especially in emerging markets.The industry's biggest challenges and opportunities are going to be seen in the longer-term.
To survive and flourish, companies in Europe will need to prioritize sustainability and raise their environmental standards as governments, investors, and the general public increasingly are pushing companies to reduce their carbon footprint.Cement companies that prioritize sustainability are likely to emerge as the leaders in the next cycle.Many companies are already taking significant measures towards decarbonization.
The European Cement industry (EU 28) accounted for XX Metric tons/year of cement capacity with production of cement ranging from 176.5 Metric tons/year in 2023 and is further forecasted to reach about xx Mt/year by 2030 at a CAGR of 2.2%.
Out of 65 markets that have produced quarterly data for H1 2021, 25 had recorded year-on-year (Y-o-Y) growth in that period, including the most major companies established and manufacturing cement in the EU Nations i.e., Heidelberg Cement, Cemex and Lafarge Holcim Cement.
Cement is obtained by grinding cement clinker and, in some cases, supplementing it with additions. Spain, Italy, Germany, France and Poland are the largest producers of cement clinkers in the EU. Before the pandemic, the industry was not operating at full capacity; with the global economic slowdown, plants were expected to see further drops in utilization rates.
As countries began to reopen post-pandemic, consumption of cement and concrete is expected to gradually recover, fueled by economic growth, urbanization, and population growth, especially in emerging markets. The industryâs biggest challenges and opportunities are going to be seen in the longer-term.
To survive and flourish, companies in Europe will need to prioritize sustainability and raise their environmental standards as governments, investors, and the general public increasingly are pushing companies to reduce their carbon footprint. Cement companies that prioritize sustainability are likely to emerge as the leaders in the next cycle.Many companies are already taking significant measures towards decarbonization.
The European cement industry is facing substantial operational and investment costs, due to stricter environmental regulations.Similarly, labour, raw material extraction, and fuel costs are also on the rise. It is expected that European governments will continue to introduce new legislation to curb carbon emissions further. To comply with the new regulations, the European cement industry is expected to continue to upgrade their technologies as well as use alternative fuels, such as biomass, fly ash, blast furnace slag etc.
The UK is facing rising operational costs due to reducing carbon dioxide emissions, as the country adopted stringent regulations to reduce carbon dioxide emission by 57% until 2030. Cement is one of the industries which would need to reduce emission further to comply with the government regulations. However, this will require additional investment and would result in high production costs.
In Europe, Turkey is the largest country in terms of cement production. Residential construction is increasing on the back of government projects of affordable housing schemes. At the same time, infrastructure spending is also expanding. Under Turkeyâs Vision 2023, the government planned to build 70,000 km of roads network and 20,000 km of the railway network. There are other various government projects under private-public partnerships including bridges, airports, tunnels, railway stations, etc.
Moreover, energy projects and healthcare projects are also underway. Overall, the Turkish demand for cement is expected to remain elevated during the forthcoming years.
The Cleantech Scale-up Coalition was established by Ecocem, an Irish company that specialises in low-carbon cement, in collaboration with seven other European businesses. Breakthrough Energy is a supporter of the coalition, which seeks to assist Europe in becoming "climate-neutral, energy-autonomous, and industrially competitive.To usher in "a new era of climate and industrial leadership for Europe," according to the Cleantech Scale-up Coalition.
It is based on the idea that Europe has most of the technologies it needs to achieve net zero emissions, but is having trouble industrialising and scaling them up.
The coalition is made up of businesses whose goods and services range from electrifying transportation to recycling materials and batteries to decarbonizing industry and energy with renewable hydrogen and scalable low-carbon cement. Its founding members are:
The two largest cement producers and the three largest glass producers in Portugal, who together account for 10% of the nation's industrial carbon emissions, announced that they have joined a new consortium to build a green hydrogen plant.
The Nazare Green Hydrogen Valley (NGHV) consortium, which also includes the glass manufacturers BA Glass, Crisal, and Vidrala, is headed by Portugal-based Rega Energy, a producer of renewable gas. The consortium will build a green hydrogen power plant with a 40 megawatt (MW) initial installed capacity that could eventually reach 600 MW.
The consortium also includes the water provider Aguas do Centro Litoral (ACL) and the distributor of natural gas GGND.The electrolysis plant will use solar energy to separate water into hydrogen and oxygen after receiving waste water from ACL.
In the Berlin-Brandenburg region, eight of Cemex's 14 ready-mix concrete plants have previously undergone conversions to deliver concrete with recycled aggregates. These plants are technically equipped to produce and supply concrete with recycled aggregates.The concretes with recycled aggregates for the Berlin metropolitan market are a component of Cemex's Vertua® product family, which includes ready-mix concretes, cements, aggregates, and admixtures. Vertua® is a global brand for products with sustainable qualities.
Additionally, Cemex introduced Regenera, a company that offers circularity solutions, in early 2023. Regenera provides a wide variety of customised services, such as waste management, recycling, and co-processing.
The Alkern Group, the French market leader in the prefabrication of concrete elements for low-carbon construction technologies, and Hoffmann Green Cement have announced the signing of a deal for the supply of their decarbonated cements. Alkern Group has chosen Hoffmann Green Cement to supply it with 0% clinker cement to replace its conventional cement supply for a portion of its products marketed in France in order to take its environmentally responsible approach even further.
In order to achieve our shared aims of zero net carbon emissions by 2050, Hoffmann's cement will enable Alkern to achieve its goal of reducing carbon emissions from its product offering and producing very low carbon product ranges in the market.
The Carbon Neutral Alliance, founded by CEMEX and its partners, intends to speed the development of breakthrough technologies that will transform CEMEX's Rudersdorf plant into the world's first carbon-neutral cement factory.The Carbon Neutral Alliance is a collaboration of over 20 business and public organisations committed to climate change innovation.
A waste heat recovery project, as well as the development of renewable energy generation, are among the technologies being introduced at Rudersdorf.In addition, CEMEX plans to create sustainable aviation fuel on-site as a result of its collaboration with Sasol and ENERTRAG.
The Carbon Neutral Alliance's experience and knowledge will be invaluable to CEMEX as it works to decarbonize the cement manufacturing process at its facilities around the world.
The largest concrete maker in Denmark, IBF, and Biomason, a North Carolina-based biotechnology company, have announced a new agreement to produce ultra-low carbon concrete materials for Europe and to transition IBF's portfolio to a zero carbon footprint utilising biocement technology.
The manufacturing relationship establishes IBF as a pioneer in the quest to decarbonize the Danish concrete industry and kickstarts Biomason's demand-driven commercial deployment throughout Europe.
The joint venture will initially concentrate on producing Biomason bioLITH precast concrete goods at the IBF site in Ikast, Denmark, which will act as the main production for European orders.
The first stage of a staged strategy to switch IBF's own concrete product lines to biocement ingredients is the production of bioLITH tile, which has one of the lowest carbon footprints on the market.
On behalf of the KGAL ESPF 4 renewable energy fund, KGAL Investment Management has entered into long-term power purchase agreements (PPAs) with Lafarge Cement Polska for the Krasin and Rywald onshore wind farms.
The two wind farms will provide Lafarge with about 230 GWh/yr of renewable electricity when they are combined. DWF Poland Jamka and PwC provided legal counsel to KGAL throughout the contract discussions.
Gebr. Pfeiffer and CBMI establish a powerful partnership. To provide effective plants for combined clay grinding and calcination, two well-known cement industry businesses enter into a collaboration arrangement.
In order to reduce CO2 emissions and so help to slow down global warming, the use of clinker alternatives in the cement industry is becoming more and more important.
For these integrated production lines, CBMI Construction Co., Ltd. serves as an experienced general contractor and Gebr. Pfeiffer SE serves as the expert in highly effective drying and grinding technology. Gebr.
The fact that this agreement once again affirms the long-standing collaboration that has already resulted in countless successful projects in the cement industry makes both partners happy.
The cement industry in Europe has witnessed several noteworthy partnership acquisitions in recent years as companies strive to strengthen their market presence, expand their geographical reach, and enhance operational efficiencies.
One notable example is the acquisition of Italcementi by HeidelbergCement.Italcementi was one of the largest cement producers in Europe.
The acquisition allowed HeidelbergCement, already a leading player in the industry, to further consolidate its position and expand its presence in key European markets.
This partnership acquisition provided HeidelbergCement with a broader product portfolio, access to new customers, and synergies in terms of production capacity and operational efficiency.
Another significant acquisition took place when CRH plc acquired certain assets from LafargeHolcim in Europe.
The acquisition included cement plants and grinding facilities located in France, Germany, Hungary, Slovakia, and the United Kingdom.
This partnership allowed CRH to strengthen its position in the European cement market and enhance its regional footprint. It provided CRH with increased production capacity, a wider customer base, and operational synergies.
Furthermore, Cementir Holding acquired CCB Group's operations in France and Belgium. The acquisition expanded Cementir's presence in Western Europe and reinforced its position in the white cement market.
Cementir was able to enhance its production capabilities and geographic coverage through this partnership acquisition, thereby strengthening its market position and serving a broader customer base.
Additionally, HeidelbergCement completed the acquisition of a 45% stake in the Italcementi subsidiary, Italcementi Participations.
This acquisition allowed HeidelbergCement to further consolidate its position in the European cement industry and optimize its operations.
It provided HeidelbergCement with increased control over Italcementi's assets and enabled the realization of synergies between the two companies.
Moreover, CRH has been actively pursuing partnership acquisitions in the European cement market. In recent years, CRH has acquired cement plants and related assets in various countries, including Germany, France, and Spain.
These acquisitions have allowed CRH to strengthen its regional presence, expand its production capacity, and leverage operational efficiencies.
As the demand for cement and construction materials continues to evolve, we can expect further partnership acquisitions in the European cement sector.
A novel low-carbon cement being developed by Cem'In'Eu is based on the locally produced pozzolan, a natural raw material.The French cement manufacturer wants to significantly reduce the percentage of clinker and, as a result, the cement's carbon footprint.
When it comes to lowering the overall carbon footprint of the cements made by Cem'In'Eu, both in bulk and in bags, the usage of pozzolan has a significant leveraging effect.
A long-term supply agreement has allowed Cem'In'Eu to ensure its pozzolan supply, which is necessary for the production of its low-carbon cement, without running the risk of the supply chain being disrupted.Today, Hoffmann Green Cement Technologies announced the introduction of H-IONA, its newest low-carbon innovation.
With a carbon footprint of less than 150 kilos per metric tonne, this new cement's production emits six times less CO2 than conventional Portland cement and is integrated into the current production unit.
Hoffmann Green Cement has created an innovative specific activation system that allows it to produce this heating-free technology at its fully automated 4.0 industrial site while conserving natural resources by recycling byproducts of industry.
This technology builds on the technologies already perfected by the Company, most notably H-UKR.The main ingredients in this cement are calcium sulphate and pulverised furnace slag. The first low-carbon cement to receive CE certification is H-IONA.
With an emphasis on cement solutions and related goods, Cementbouw is a well-known company in the construction and infrastructure sector. The Cementbouw company, with its headquarters in Europe, is well-known within the construction sector for its high-quality products and dedication to environmentally friendly techniques. Cementbouw, which was established several decades ago, has developed into a significant participant in the cement and building materials markets.
The company's primary goal is to meet the varied needs of its clients, who can range from small-scale infrastructure projects to independent builders, by offering creative and dependable solutions.
Each cement-based product in Cementbouw's portfolio is designed to meet a particular need in the building industry. The emphasis on sustainability placed by Cementbouw is one of its distinctive qualities.
The company has engaged in research and development to produce environmentally friendly cement formulations since it is aware of the environmental difficulties involved with cement production.
These formulas are designed to use less energy and produce less carbon emissions. By doing this, Cementbouw displays its dedication to positively advancing the global movement for sustainable building techniques.
Cementbouw's strict quality control procedures demonstrate its dedication to excellence. In order to guarantee that its goods meet or surpass regulatory requirements, the company abides by strict industry standards.
Customers that depend on Cementbouw's goods for their building projects appreciate the company's commitment to quality. In addition to its product offerings, Cementbouw places a high priority on working with and supporting its clients.
The business treasures the ties it has built with its clients through time and works hard to comprehend their particular requirements. Cementbouw consistently enhances its goods and services by having open discussions and actively soliciting feedback.
The influence of Cementbouw goes beyond its goods and services. The business appreciates its place in the communities it serves and takes part in a number of community improvement projects. Cementbouw aims to be a good corporate citizen by encouraging educational initiatives pertaining to building and supporting local infrastructure projects. Cementbouw continues to be at the front edge of innovation as the construction sector changes.
Cemexa is a popular option among contractors, builders, and engineers because of its reputation for dependability and constant performance. Its composition guarantees the best strength, workability, and durability, all of which are essential for the accomplishment of building projects.
Cemexa contributes to the overall integrity and endurance of the built environment whether it is employed in concrete foundations, structural elements, or finishing touches. Cemexa's flexibility to adapt to many applications is one of its distinguishing qualities.
It can be applied to many other types of construction techniques, such as conventional casting, precast components, and ready-mix concrete. No matter how complicated or large the job is, this adaptability makes it simpler and more efficient. Cemexa is a product of LafargeHolcim's dedication to environmentally friendly building.
Cemexa is not an exception to the company's significant attention on minimizing environmental effect. Cemexa works to reduce the amount of carbon emissions and energy used in its manufacturing through improvements in production methods and material sourcing.
This is consistent with LafargeHolcim's commitment to resource management accountability and sustainable practices. Cemexa represents LafargeHolcim's commitment to innovation, quality, and the development of the construction sector. It is more than just a product.
S No | Company Name | Development |
---|---|---|
1 | CEMBUREAU | The European Cement Association (CEMBUREAU) releases a new Carbon Neutrality Roadmap that outlines its goal of achieving net zero emissions throughout the cement and concrete value chain. |
In order to attain zero net emissions,CEMBUREAU'sCarbon Neutrality Roadmap examines how CO2 emissions might be decreased by intervening at each stage of the value chain, including clinker, cement, concrete, construction, and (re)carbonation.
It quantifies each technology's contribution to reducing CO2 emissions and offers specific political and technological suggestions in support of this goal.A pan-European CO2 transportation and storage network is being developed as part of it. a level playing field with regard to carbon emissions, regulatory stability, and a bold plan for industrial change.
S No | Company Name | Development |
---|---|---|
1 | ESFC Investment Group | The European economy greatly depends on investments in the cement sector because so many other businesses rely on it. The competitiveness of European cement factories would decline as a result of increased pressure on businesses to meet EU climate goals, and imports of cement from nations that are less concerned about CO2 emissions would rise. |
The second most used substance in the world, after water, is concrete, the most popular building material formed from cement, aggregates, and water.European cement manufacturers and investors are keenly monitoring geopolitical developments and economic shifts in the EU, which could have an impact on the sector's growth during the next ten years.
S No | Company Name | Development |
---|---|---|
1 | CEMBUREAU, BIBM and EFCA and ERMCO | Heading along the value chain, the industry seeks to lower its overall CO2 emissions by a specific percentage for cement. For this reason, Concrete Europe a new umbrella organization was formed by the union of the four European associations that represent the concrete industry and its value chain: BIBM (the Federation of the European Precast Concrete Industry), CEMBUREAU (the European Cement Association), EFCA (the European Federation of Concrete Admixtures Associations), and ERMCO (the European Ready Mixed Concrete Organization). |
2 | CHRYSO and Hoffmann Green Cement Technologies | CHRYSO (Saint-Gobain Construction Chemicals) announces the creation of an ultra-low carbon concrete solution based on the novel admixture CHRYSO EnviroMix ULC 5500, created especially for Hoffmann Green Cement Technologies' H-UKR type cement. |
At each stage of theCEMBUREAUâscement and concrete supply chain, the Roadmap emphasizes initiatives and suggested regulatory frameworks to attain carbon neutrality.
The construction ecosystem transition pathway and the whole life carbon road map, which were published by the European Commission, have had an impact on the built environment in Europe.
The European Concrete Platform and The Concrete Initiative have been replaced by the new organization. All EU associations involved in the concrete value chain are eligible to join.
TheCHRYSOandHoffmann Green Cement TechnologiesR&D teams have once again worked together on the development of ultra-low carbon concrete, with the elaboration of an admixture dedicated to the use of the H-UKR cement developed by Hoffmann Green Cement Technologies, following a first successful co-development on the H-EVA technology (0% clinker decarbonized clay concrete) with Bouygues Construction.
FusioVrac cement, which has a CO2 footprint 18% smaller than standard cement, has been introduced by Cem'In'EU's Rhône cement factory in Portes-lès-Valence. FusioVrac is a low-carbon cement that uses pozzolan, a naturally occurring substance derived from volcanic rocks in the area, in place of some of the clinker. According to CemIn Eu general manager Fabien Charbonnel, the new cement provides "the same performance while adhering to the same standards as the other products currently on the market.
FusioVrac, which presently accounts for about 80% of French cement usage, will be produced in large quantities. Because quantifying one's carbon footprint will soon be required by law, there will be a greater need for this type of cement. "Gradually they will switch to building permits which will have to respect the RE, new regulations, so this product will be sought after," says the author.
In order to produce ECOPlanet green cement, which has a 50% lower CO2 footprint than normal cement (CEM I), Holcim launched the first calcined clay cement operation in Europe at its Saint-Pierre-la-Cour factory in France.Up to 500,000 tonnes of low-carbon cement will be produced annually by this cutting-edge production line, which is a world first and powered by Holcim's patented proximA Tech technology.
Calcined clay is produced in an incredibly efficient and practically carbon-free manner due to the company's sustainable operations, which are powered by waste heat recovery systems and alternative fuels made entirely of biomass.Their effort to decarbonize construction has reached another significant turning point with the debut of the first calcined clay cement production line in Europe.
By advancing their ECOPlanet line of low-carbon cement, they are scaling up their calcined clay cements throughout all areas, making low-carbon construction feasible on a large scale.This initiative is a part of Holcim's plan to use a variety of low-emission building materials, such as calcined clay and construction and demolition debris, to decarbonize construction throughout Europe.
As a part of the "France Relance" programme, which invests in extensive decarbonization and energy efficiency programmes in France, it received financial backing from the French government.
At its Rugby cement plant, CEMEX announced the opening of a new Climafuel unit. In terms of decarbonization, CEMEX in Europe is at the forefront of the sector. By the end, CEMEX is anticipated to reduce carbon emissions in Europe by 40%, putting it on track to meet its target of a 55% reduction by 2030, which is in line with the European Union's decarbonization objective.
The cornerstone to CEMEX's efforts to decarbonize operations as part of its Future in Action strategy and global commitment to create net-zero CO2 concrete is reducing the usage of fossil fuels at its cement facilities.The construction of a new Climafuel facility by CEMEX at its Rugby Cement Plant is an important step towards the company's decarbonization goals.
The majority of EU cement producers operate on a global level, giving them access to global best practice and technology. Raw materials are extracted mainly onsite, which avoids transportation costs and environmental damage.
Mexico-based Cemex has announced the suspension of production at all of its plants in Panama and those of its Colombian subsidiary Cemex Latam Holdings from 25 March 2020. It may resume certain activities on or before 13 April 2020.
US-based company GCP Applied Technologies has received a European patent for increasing the efficiency of cement grinding by using sustainable raw materials.
Heidelberg Cement has limited the amount of net investments to around â¬1.2 billion per year. Net investments refer to the balance of investment and divestment in the area of property, plant and equipment.
Slno | Topic |
1 | Market Segmentation |
2 | Executive Summary |
3 | Average B2B Price of Cement - 2023 |
4 | Global Cement Producers -2023 |
5 | Cement Plants in Europe |
6 | Cement Production in Europe 2024-2023 |
7 | Europe Cement Supply Chain |
8 | Impact of Russia-Ukraine war on Europe Cement Market |
9 | Major Market Drives in Europe Cement Market |
10 | Cement Exports in Europe 2024-2023 |
11 | Competition materials to cement in Europe |
12 | New Innovations By Major Players in the Cement Market |
13 | Initiatives by European Suppliers towards low-carbon concrete production |
14 | Infrastructure pipeline in Europe |
15 | Key Trends in Europe Cement Market |
16 | Market Size ,Dynamics and Forecast By Type |
17 | Market Size ,Dynamics and Forecast By Geography |
18 | Market Size ,Dynamics and Forecast By End Use |
19 | Competitive Landscape |
20 | Market share of major vendors - 2023 |
21 | Growth Strategy of Major Players |
22 | M&A in Past Few Years |
23 | Company Profiles |
24 | Unmet needs and Market Opportunity for new vendors |
25 | Conclusion |