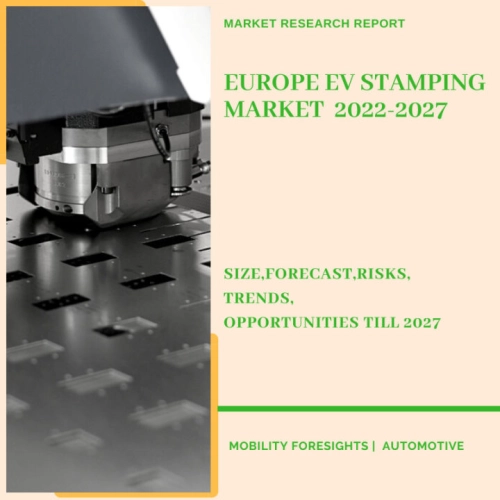
- Get in Touch with Us
Last Updated: Apr 25, 2025 | Study Period: 2022-2027
EVs require battery packs that are constructed from arrangements of smaller individual batteries. Manufacturers construct enclosures that can contain the batteries securely and safely using stamping techniques.
Traditional automobiles frequently include stainless steel parts, which can increase the vehicle's weight and drag. Lightweight components are advantageous for electric vehicles because they improve energy efficiency, and manufacturers may produce such components using aluminium stamping.
Due to the less energy-intensive tooling requirements for aluminium parts, the production process for electric vehicles can be more energy-efficient overall. With growing emphasis on energy-efficient parts, equipment, and assemblies, stamped items can become even more intricate.
Busbars are a feature of EVs that distribute current from the battery pack to various electrical topologies and subassemblies. The vehicle's engine, communication systems, windows, sunroofs, anti-lock brakes, remote controls, and sensors are among these subassemblies and individual applications.
Busbars and individual assemblies are precisely fabricated using stamping techniques.
The proliferation of electric vehicles is outpacing the installation of charging infrastructure, which, according to the European Automobile Manufacturers' Association, or ACEA, might jeopardise the European Union's emissions objective. Soon, new public charging stations must be created weekly to make up the deficit.
The ACEA estimates that over the previous five years, plug-in car sales in Europe have multiplied ten-fold. The number of public charge points increased within the same time period.
The Europe EV Stamping Market accounted for $XX Billion in 2021 and is anticipated to reach $XX Billion by 2026, registering a CAGR of XX% from 2022 to 2027.
Sl no | Topic |
1 | Market Segmentation |
2 | Scope of the report |
3 | Abbreviations |
4 | Research Methodology |
5 | Executive Summary |
6 | Introduction |
7 | Insights from Industry stakeholders |
8 | Cost breakdown of Product by sub-components and average profit margin |
9 | Disruptive innovation in the Industry |
10 | Technology trends in the Industry |
11 | Consumer trends in the industry |
12 | Recent Production Milestones |
13 | Component Manufacturing in US, EU and China |
14 | COVID-19 impact on overall market |
15 | COVID-19 impact on Production of components |
16 | COVID-19 impact on Point of sale |
17 | Market Segmentation, Dynamics and Forecast by Geography, 2022-2027 |
18 | Market Segmentation, Dynamics and Forecast by Product Type, 2022-2027 |
19 | Market Segmentation, Dynamics and Forecast by Application, 2022-2027 |
20 | Market Segmentation, Dynamics and Forecast by End use, 2022-2027 |
21 | Product installation rate by OEM, 2022 |
22 | Incline/Decline in Average B-2-B selling price in past 5 years |
23 | Competition from substitute products |
24 | Gross margin and average profitability of suppliers |
25 | New product development in past 12 months |
26 | M&A in past 12 months |
27 | Growth strategy of leading players |
28 | Market share of vendors, 2022 |
29 | Company Profiles |
30 | Unmet needs and opportunity for new suppliers |
31 | Conclusion |
32 | Appendix |