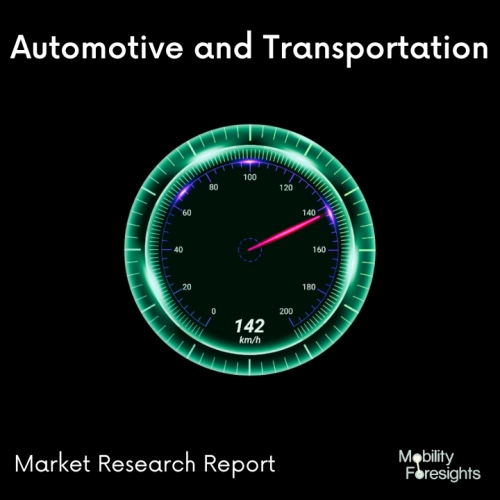
- Get in Touch with Us
Last Updated: Apr 25, 2025 | Study Period: 2024-2030
The most important, expensive, and delicate part of an electric vehicle is the battery. Automakers anticipate that the battery will be between 30 and 50 percent of the entire cost of an electric vehicle. Global automakers are developing plans to increase manufacturing capacity and supply infrastructure.
The battery poses a difficult design challenge to both manufacturers and material suppliers since it sits at the point where the powertrain and structural parts meet. Maximum protection for the vital component of an electric car is the first priority. The battery must be corrosion- and crash-proof, electromagnetically insulated, and cooled, among other complicated criteria.
The freshly created steel design of the Electrify battery housing offers great performance. A frame, connection profile, upper and lower support arms, an underride guard, and a cover make up the enclosure. It is practically weight neutral when compared to aluminium and is offered in a large selection of patented designs.
The electrify battery housing is evidence that safety, fire protection, and lightweighting can all be incorporated while still achieving significant cost reductions.
The hotspots change from the use phase to the production phase when comparing the life-cycle environmental effect of electric vehicles to internal combustion engine vehicles. Steel is the most environmentally responsible material for battery housings, according to life cycle analyses.
The Global EV battery fire-resistant steel housing market accountedfor $XX Billion in 2023 and is anticipated to reach $XX Billion by 2030, registering a CAGR of XX% from 2024 to 2030.
The space envelope for the battery modules must be as large as feasible, and the battery housing must also adhere to specifications for mechanical loading and sealing.
A deep-drawn shell made of stainless steel can be used to create a geometrically straightforward battery housing. The benefit of this method over using fabricated structures constructed from low-alloyed steels or extruded aluminium profiles is in its sealing and simpler manufacturing.
Deep-drawn battery bottom shells also reduce container space requirements significantly. Moreover, there is no requirement for welding-related production stages in the battery "clean room." Costs of production are decreased because thermal distortion is eliminated and cleaning requirements are decreased.
Complex design and engineering issues arise throughout the development of EVs, particularly with regard to battery housings. The battery modules need to be shielded from environmental factors such deformation, corrosion, severe temperatures, and stone chips in order to avoid thermal collapse.
Yet, they must also permit simple maintenance and replacement access. Fulfilling crash criteria is a difficult task as well, especially in situations when there is little room for penetration, like with side and underfloor intrusion. Effective thermal management is also required to maintain batteries at the appropriate operating temperature for maximum range.
A crucial requirement for the safety of electric vehicles is the prevention of fire in the battery housing. Battery fires cannot be put out, hence passengers must be safeguarded by the housing in the case of a fire. A steel battery casing provides crucial minutes for passengers and other accident participants in the event of a fire.
The steel's fusion point The outstanding safety reserves of steel are demonstrated in fire tests where the temperature of the steel battery housing cover rarely rises even after 20 minutes. In comparison, in the fire test, aluminium takes just 15 seconds to reach its melting temperature of 610°C. The material gives way after 30 seconds, leaving the passenger cell completely exposed to the flames.
Sl no | Topic |
1 | Market Segmentation |
2 | Scope of the report |
3 | Abbreviations |
4 | Research Methodology |
5 | Executive Summary |
6 | Introduction |
7 | Insights from Industry stakeholders |
8 | Cost breakdown of Product by sub-components and average profit margin |
9 | Disruptive innovation in the Industry |
10 | Technology trends in the Industry |
11 | Consumer trends in the industry |
12 | Recent Production Milestones |
13 | Component Manufacturing in US, EU and China |
14 | COVID-19 impact on overall market |
15 | COVID-19 impact on Production of components |
16 | COVID-19 impact on Point of sale |
17 | Market Segmentation, Dynamics and Forecast by Geography, 2024-2030 |
18 | Market Segmentation, Dynamics and Forecast by Product Type, 2024-2030 |
19 | Market Segmentation, Dynamics and Forecast by Application, 2024-2030 |
20 | Market Segmentation, Dynamics and Forecast by End use, 2024-2030 |
21 | Product installation rate by OEM, 2023 |
22 | Incline/Decline in Average B-2-B selling price in past 5 years |
23 | Competition from substitute products |
24 | Gross margin and average profitability of suppliers |
25 | New product development in past 12 months |
26 | M&A in past 12 months |
27 | Growth strategy of leading players |
28 | Market share of vendors, 2023 |
29 | Company Profiles |
30 | Unmet needs and opportunity for new suppliers |
31 | Conclusion |
32 | Appendix |