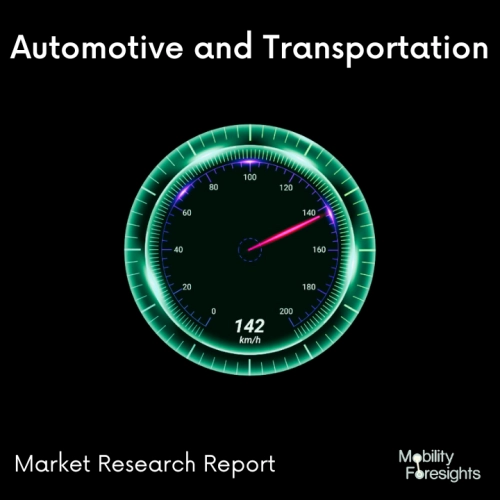
- Get in Touch with Us
Last Updated: Apr 25, 2025 | Study Period: 2024-2030
Copper C110 is used to make solid copper bus bars. It goes through stamping, CNC bending, final treatment, and insulation during processing.
The busbar finish might be bare copper, tin plating, nickel plating and silver plating. PVC, PE heat shrink tube, epoxy powder coating, and PA12 are all acceptable forms of insulation. They are frequently utilized in electric vehicle battery packs, electric forklifts, charging heaps, and energy storage systems.
Solid metal bars called busbars are used to transport current. Busbars, which are usually composed of copper or aluminum, are more durable and flat than cables but up to 70% shorter in height.
Additionally, compared to cables with the same cross-sectional area, they may carry higher current. Busbars are an important part of the electrical architectures of upcoming automobiles due to their advantages for some high-voltage connections in electric vehicles (EVs).
The paucity of room in modern automobiles is the primary factor influencing the introduction of busbars. Power and data lines are necessary for each sensor, actuator, and electric/electronic component in a vehicle, as well as all of the packaging space they require.
Busbars' lower-profile routing allows for the usage of other electrical components because they do not sit as high as cables do.
Additionally, they can be bent at angles more precisely and tightly than a cable can, closely conforming to vehicle profiles. The requirement for mechanized assembly is the second factor.
Even though a lot of vehicle assembly is now automated, wiring installation is still mostly a manual process. It can be exceedingly challenging for a robotic arm to grip a wiring harness and install it properly in a car due to the flexibility that has made cabling so commonplace.
In comparison, moving a rigid busbar into place is significantly simpler for a robot. Given that EVs operate at high power and potentially expose assembly workers to strong electric currents, automated assembly is less expensive from a labor perspective, it enables improved quality, and it is also safer.
The Global EV Copper busbars Market accountedfor $XX Billion in 2023 and is anticipated to reach $XX Billion by 2030, registering a CAGR of XX% from 2024 to 2030.
Due to their superior conductivity, high thermal conductivity, and strong mechanical qualities, copper busbars are frequently used in vehicle electrical systems. Busbars are frequently used to distribute power to several electrical systems, including the battery, alternator, and others, in vehicles.
Due to its excellent electrical conductivity, which enables effective power transfer and minimal power losses, copper is the perfect material for busbars. The strong thermal conductivity of copper also aids in the removal of heat produced by the electrical system.
To connect high-voltage and low-voltage equipment, EG Electronics offers a wide variety of busbars that are frequently used in electric power distribution. They are typically non-insulated, but we have a wide variety to fulfil application requirements.
They are important in every jut manually or with the aid of a copper row bending machine, making the cabin and making installation action or power distribution box. The high-softness copper used in the flexible busbar is produced using a unique technique. For any twisting or bending, it can be easy for engineers.
Sl no | Topic |
1 | Market Segmentation |
2 | Scope of the report |
3 | Abbreviations |
4 | Research Methodology |
5 | Executive Summary |
6 | Introduction |
7 | Insights from Industry stakeholders |
8 | Cost breakdown of Product by sub-components and average profit margin |
9 | Disruptive innovation in the Industry |
10 | Technology trends in the Industry |
11 | Consumer trends in the industry |
12 | Recent Production Milestones |
13 | Component Manufacturing in US, EU and China |
14 | COVID-19 impact on overall market |
15 | COVID-19 impact on Production of components |
16 | COVID-19 impact on Point of sale |
17 | Market Segmentation, Dynamics and Forecast by Geography, 2024-2030 |
18 | Market Segmentation, Dynamics and Forecast by Product Type, 2024-2030 |
19 | Market Segmentation, Dynamics and Forecast by Application, 2024-2030 |
20 | Market Segmentation, Dynamics and Forecast by End use, 2024-2030 |
21 | Product installation rate by OEM, 2023 |
22 | Incline/Decline in Average B-2-B selling price in past 5 years |
23 | Competition from substitute products |
24 | Gross margin and average profitability of suppliers |
25 | New product development in past 12 months |
26 | M&A in past 12 months |
27 | Growth strategy of leading players |
28 | Market share of vendors, 2023 |
29 | Company Profiles |
30 | Unmet needs and opportunity for new suppliers |
31 | Conclusion |
32 | Appendix |