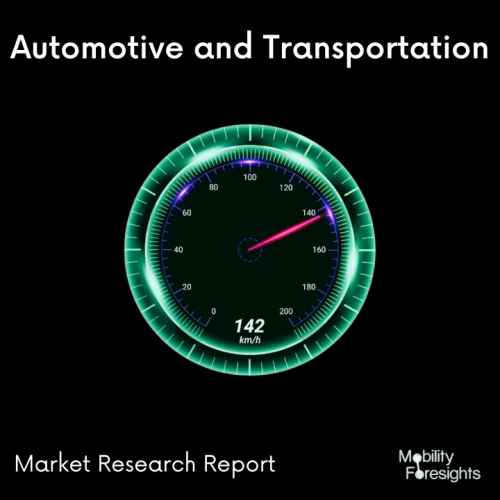
- Get in Touch with Us
Last Updated: Apr 25, 2025 | Study Period: 2023-2030
As a tetrafluoroethylene and hexafluoropropylene copolymer, fluorinated ethylene propylene copolymer (FEP) is a semi-crystalline perfluorinated polymer that is closely related to PTFE (FP30). Although its characteristics are mostly inferior to those of PTFE, they are comparable nonetheless, and it has the excellent practical benefit of being melt-processable. (though more expensive).
Its superior chemical resistance, electrical capabilities (up to very high frequencies), and excellent weathering resistance are comparable to those of PTFE when compared in more detail. It has increased impact strength and better radiation resistance, but it also has lower maximum use and heat deflection temperatures, and it is even a little less stiff and robust.
The Global EV Fluorinated ethylene propylene (FEP) market accounted for $XX Billion in 2022 and is anticipated to reach $XX Billion by 2030, registering a CAGR of XX% from 2023 to 2030.
Similar to Fluorinated Ethylene-Propylene (FEP), which has the trademark TeflonTM, PTFE was developed and has since grown to be one of the most significant man-made materials. PTFE, which is well-known for its non-stick qualities, is more flexible than conventional thermoplastics and durable over a broad temperature range.
PTFE is also extensively used because of its dielectric qualities, which enable it to be used as the dielectric material in RF coaxial cable assemblies and as insulation for wire jackets.
A centre conductor can be used to extrude PTFE into narrow cylindrical shapes, which can then be jacketed to create coaxial lines like RG-6 or RG-174 wire.PTFE cable is remarkably popular in LVDS and military cabling, in addition to being used on RF cables. Manufacturers struggle to bind materials to the PTFE jacket and process intricate cable bundles because of how slippery it is.
Small gauge wires that are twisted and routed in a bundle run the risk of sliding within the cross-section, which would result in the cable losing its form. In order to create a differential pair using the PTFE dielectric material as the wire jacket, twisted pairs can be wrapped together with a tight lay that achieves 4 twists per inch or tighter.
S No | Company Name | Development |
---|---|---|
1 | DelStar Technologies | In order to provide affordable solutions for high performance fluid and gas processing applications, DelStar Technologies, Inc. launched the new Coretec FEP tubing product. The new tube is made of low density polyethylene (LDPE), which is more affordable, and has a protective Teflon FEP (fluorinated ethylene propylene) layer within. |
Five sizes of this FEP-lined fractional tubing are available fromDelStar Technologies. This tubing offers FEP's advantages at a fraction of the price by coating the inner surface of LDPE tubing with the material. A surface with an extremely low coefficient of friction, low permeability, and chemical inertness is provided by the FEP lining.
Along with good thermal and electrical stability, it also demonstrates excellent chemical resistance. A cost-effective method to guarantee precise and reliable performance is to use Coretec FEP-lined tubing. For processing corrosive chemicals, fuels, solvents, or acids, industrial pumps are the best choice. The interior of the container is non-stick, which makes it easy to clean by flushing away adhesives or paint spray.
Fluorinated ethylene propylene (FEP) film is manufactured and used in VueLife "AC" Bags. Because of this unique surface treatment, the interior of the VueLife "AC" Bag has more surface energy than the interior of the VueLife® "C" Bag. The VueLife "AC" Bag's enhanced surface is intended to better stimulate cell and protein adherence to the surface of the bag, a property that can be used for transduction and transfection applications.
VueLife bags enable permeability to oxygen and carbon dioxide while remaining impermeable to water for increased culture and expansion since they are produced from the highest quality USP Class VI FEP material.
Each "AC" series bag typically has a needle-free injection site, a "Y" connector with PVC tubing leading to a female luer and a heat-sealed sterile docking tube, and these characteristics help to significantly lower the danger of culture contamination while facilitating the introduction of new material. There are more port, tubing, and connector kinds that can be tailored to the user's requirements.
Chemically, hexafluoropropylene and tetrafluoroethylene are copolymers to create FEP (fluorinated ethylene propylene). As a melt-processable variant of PTFE, it was developed. As a result, it has all of PTFE's chemical resistance and non-stick qualities while also having the capacity for extrusion and thermoforming. Holscot produces a wide range of FEP-based products for a wide range of sectors, including Heat Shrink Sleeving for the Print, Paper, Lamination, and related sectors.
The company has the ability to wrap or coat in-line objects like lights, lamps, metal, glass, and ceramic rods, as well as flexible elastomers like silicone and viton cable. They regularly provide a range of formed pieces for use in the aerospace, space, chemical, medical, pharma, and bio areas, and more recently have started delivering FEP for use in EV battery operated vehicles.
Sl no | Topic |
1 | Market Segmentation |
2 | Scope of the report |
3 | Abbreviations |
4 | Research Methodology |
5 | Executive Summary |
6 | Introdauction |
7 | Insights from Industry stakeholders |
8 | Cost breakdown of Product by sub-components and average profit margin |
9 | Disruptive innovation in theIndustry |
10 | Technology trends in the Industry |
11 | Consumer trends in the industry |
12 | Recent Production Milestones |
13 | Component Manufacturing in US, EU and China |
14 | COVID-19 impact on overall market |
15 | COVID-19 impact on Production of components |
16 | COVID-19 impact on Point of sale |
17 | Market Segmentation, Dynamics and Forecast by Geography, 2023-2030 |
18 | Market Segmentation, Dynamics and Forecast by Product Type, 2023-2030 |
19 | Market Segmentation, Dynamics and Forecast by Application, 2023-2030 |
20 | Market Segmentation, Dynamics and Forecast by End use, 2023-2030 |
21 | Product installation rate by OEM, 2023 |
22 | Incline/Decline in Average B-2-B selling price in past 5 years |
23 | Competition from substitute products |
24 | Gross margin and average profitability of suppliers |
25 | New product development in past 12 months |
26 | M&A in past 12 months |
27 | Growth strategy of leading players |
28 | Market share of vendors, 2023 |
29 | Company Profiles |
30 | Unmet needs and opportunity for new suppliers |
31 | Conclusion |
32 | Appendix |