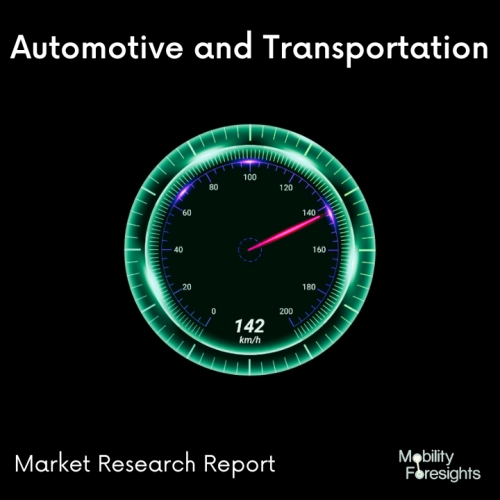
- Get in Touch with Us
Last Updated: Apr 25, 2025 | Study Period: 2023-2030
The creation of safe, suitable electrolytes that are stable and pose no safety issues is necessary for the usage of next-generation batteries. Difluoro(oxalato)borate ([DFOB]) anion has been utilised as an electrolyte additive to help with stability, but this method has mostly been used with solvent electrolytes that are flammable.
A halide-free tosylate-based synthetic pathway has effectively replaced the conventional synthetic route employing halide starting materials, which is favourable for a purer, halide-free result. While the ILs exhibit relatively strong ionic conductivity, the synthesised [DFOB]-based salts have good heat stability.
The novel electrolytes based on [DFOB] thus exhibit promise for further study as battery electrolytes in both liquid and solid states.
With the development of new battery technologies that have higher energy densities, including those that use Lithium (Li) metal anodes, it is necessary to use improved electrolytes that do not degrade or pose any safety risks.
Traditional organic electrolytes have a history of degrading in the presence of metallic Li, which increases the danger of fire and battery failure.
Ionic liquids (ILs) and organic ionic plastic crystals (OIPCs), on the other hand, may be crucial in the development of new classes of advanced electrolytes because of their superior safety prospects, including their high levels of thermal and chemical stability, lack of flammability, and negligible vapour pressure.Additionally, they often exhibit electrochemical stability across a broad potential range.
The Global EV halide-free plastics Market accounted for $XX Billion in 2022 and is anticipated to reach $XX Billion by 2030, registering a CAGR of XX% from 2023 to 2030.
Heat stabilisers deteriorate with time as a result of exposure to heat and moisture, halide ions flee the surface, and metallic connections corrode. It is advised that plastic components close to electronic circuitry contain less than 50 parts per million (ppm) of halides to prevent this kind of part failure.
To reduce the risk of electrical failure, many manufacturers are searching for thermoplastic materials that don't rely on halide additives or red phosphorous for their thermal and flame retardant properties.
DSM has a long track record of success delivering material solutions embraced by leading automotive, electrical and electronics brands worldwide.As automotive electronics become increasingly powerful and complex, they generate higher power levels and more heat, increasing the risk of electrical failure and fire.
Many automotive suppliers currently use ionic additives, such as red phosphorous flame retardants or inorganic heat stabilizers, to respectively improve the thermal and flame retardant performance of the plastic components used in electronics.
Yet, as components degrade over time, these additives can form acids that corrode electrical contacts after prolonged exposure to heat and moisture.
This may cause an electronic component to fail or change its characteristics, potentially compromising a key vehicle safety feature, such as a sensor â which may lead to severe consequences.
Sabic, a leader in the manufacturing of specialty chemicals and materials, makes halide-free thermoplastics called Xenoy iQ resins. These resins, which are recognized for their great performance and durability, were created especially for use in automotive applications. Halide-freeness is one of the main benefits of Xenoy iQ resins. Compounds containing chlorine, bromine, or iodine are known as halides.
These substances are frequently employed as flame retardants in plastics, but they may be harmful to human health and the environment. Since halide-free polymers like Xenoy iQ resins are safer and more environmentally friendly, electric car makers favor using them. Additionally, well-known for their superior mechanical qualities are Xenoy iQ resins.
They are perfect for use in automotive parts that may be exposed to difficult operating circumstances because of their excellent impact resistance and ability to survive exposure to a broad variety of temperatures. They also have resistance to UV rays and weathering, which helps to guarantee that they last for a long period while still being strong and durable.
The ease of processing Xenoy iQ resins is another benefit. They may be precisely molded into intricate designs, enabling manufacturers to produce unique components that are tailored to the demands of their vehicles. This design and manufacturing flexibility enables the development of lighter parts while maintaining their strength and durability, which can assist to enhance the vehicle's overall performance.
High-performance, halide-free thermoplastic Xenoy iQ resins are ideally suited for usage in electric vehicles. They are the best option for a variety of automotive applications due to their strength, flexibility, and longevity. In the upcoming years, it is expected that demand for halide-free polymers like Xenoy iQ resins will increase as more firms place an emphasis on sustainability and minimizing their environmental impact.
In the manufacture of specialty materials and chemicals, DuPont is a world leader. Their range of halide-free polymers, Zytel HTN, which is intended exclusively for use in electric vehicles, is one of their products. Manufacturers seeking to produce light, efficient electric cars frequently choose these materials because of their great performance and durability. The great heat resistance of Zytel HTN is one of its main benefits.
The substance is perfect for use in high-temperature applications like engine and electric motor components since it can endure exposure to temperatures of up to 300 °C without losing its mechanical qualities.
The component's strong heat resistance also contributes to its longer lifespan and lower maintenance requirements. In addition to having exceptional strength and rigidity, Zytel® HTN is a popular material for structural parts, including chassis, battery, and suspension components. Because of the material's high elasticity modulus, it can withstand large loads and stress without deforming or losing its shape.
This makes it possible for the car to maintain stability and safety even at high speeds or in difficult road conditions. The lightweight nature of Zytel HTN is another benefit. The substance has a high strength-to-weight ratio, allowing it to be significantly lighter while still offering the same amount of strength and durability as conventional materials like metal.
Sl no | Topic |
1 | Market Segmentation |
2 | Scope of the report |
3 | Abbreviations |
4 | Research Methodology |
5 | Executive Summary |
6 | Introduction |
7 | Insights from Industry stakeholders |
8 | Cost breakdown of Product by sub-components and average profit margin |
9 | Disruptive innovation in the Industry |
10 | Technology trends in the Industry |
11 | Consumer trends in the industry |
12 | Recent Production Milestones |
13 | Component Manufacturing in US, EU and China |
14 | COVID-19 impact on overall market |
15 | COVID-19 impact on Production of components |
16 | COVID-19 impact on Point of sale |
17 | Market Segmentation, Dynamics and Forecast by Geography, 2023-2030 |
18 | Market Segmentation, Dynamics and Forecast by Product Type, 2023-2030 |
19 | Market Segmentation, Dynamics and Forecast by Application, 2023-2030 |
20 | Market Segmentation, Dynamics and Forecast by End use, 2023-2030 |
21 | Product installation rate by OEM, 2023 |
22 | Incline/Decline in Average B-2-B selling price in past 5 years |
23 | Competition from substitute products |
24 | Gross margin and average profitability of suppliers |
25 | New product development in past 12 months |
26 | M&A in past 12 months |
27 | Growth strategy of leading players |
28 | Market share of vendors, 2023 |
29 | Company Profiles |
30 | Unmet needs and opportunity for new suppliers |
31 | Conclusion |
32 | Appendix |