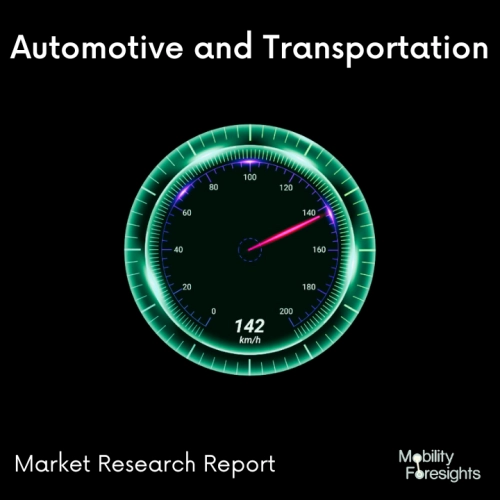
- Get in Touch with Us
Last Updated: Apr 25, 2025 | Study Period: 2023-2030
The method of plastic injection moulding involves melting plastic pellets (thermosetting/thermoplastic polymers) that, once flexible enough, are injected at pressure into a mould cavity, filling it and solidifying it to create the finished product.
The most crucial procedure in the plastics sector is injection moulding, which makes it possible to produce components quickly and affordably in practically any shape or size. Before, this method could not be used to mould transparent glass.
Glass may now be injected into moulds at 130 °C at high throughput thanks to the new "Glassomer" injection moulding technology from a unique granulate.
Pure quartz glass is produced once the injection-moulded components are heated to transform them into glass. The procedure is more energy-efficient than traditional glass melting it uses less energy.
The surface quality of the formed glass components is excellent, negating the need for additional processing processes like polishing.
Applications for the designs made available by Glassomer's glass injection moulding technique span from lab-on-a-chip and medical technology to data technology and solar technology.
Quartz glass is transparent, and its extremely low coefficient of expansion makes it ideal for sensors and optics, which function dependably at any temperature if the essential parts are constructed of glass.
The Global EV Injection Moldable Glass-Plastic market accountedfor $XX Billion in 2022 and is anticipated to reach $XX Billion by 2030, registering a CAGR of XX% from 2023 to 2030.
The most crucial procedure in the plastics sector is injection moulding, which makes it possible to produce components quickly and affordably in practically any shape or size.
Before, this method could not be used to mould transparent glass. Glass may now be injected into moulds at 130 °C at high throughput thanks to the new "Glassomer" injection moulding technology from a unique granulate.
Pure quartz glass is created once the injection-moulded components are heated up during the manufacturing process.
The procedure is more energy-efficient than traditional glass melting since it uses less energy. Because of the exceptional surface quality of the manufactured glass components, additional procedures like polishing are not necessary.
To improve its proprietary method for injecting clear glass pieces into ordinary plastics injection moulding machines, Glassomer GmbH (Freiburg, Germany) and injection moulding machine and automation supplier Engel have established a partnership.
Glassomer's method enables parts to be moulded from pellets made of a mixture of silica and a polymer binder that has been extruded into a flexible filament and cut into pellets.
The polymer binder is then removed from the moulded parts using a water-based debinding technique. The sections are sintered after being debounce, producing clear components with the same characteristics as commercial fused silica glass.
For injection moulding, there are countless plastic materials available. Tensile strength and impact resistance are only two examples of the various end-use qualities that different plastic resins can impart.
Processing specifications for injection moulded plastics include melt temperature and moulding pressure. The same plastic material is available in many grades, including resin varieties with fillers like glass or fibreglass.
Strong, transparent thermoplastic known as acrylic serves as a lightweight, break-resistant substitute for glass.
Moreover, this material has outstanding optical clarity, allowing a large amount of light to travel through. Acrylic also withstands the weather and ultraviolet (UV) light. PMMA, another name for acrylic, or its full chemical name, poly (methyl methacrylate).
Sl no | Topic |
1 | Market Segmentation |
2 | Scope of the report |
3 | Abbreviations |
4 | Research Methodology |
5 | Executive Summary |
6 | Introduction |
7 | Insights from Industry stakeholders |
8 | Cost breakdown of Product by sub-components and average profit margin |
9 | Disruptive innovation in the Industry |
10 | Technology trends in the Industry |
11 | Consumer trends in the industry |
12 | Recent Production Milestones |
13 | Component Manufacturing in US, EU and China |
14 | COVID-19 impact on overall market |
15 | COVID-19 impact on Production of components |
16 | COVID-19 impact on Point of sale |
17 | Market Segmentation, Dynamics and Forecast by Geography, 2023-2030 |
18 | Market Segmentation, Dynamics and Forecast by Product Type, 2023-2030 |
19 | Market Segmentation, Dynamics and Forecast by Application, 2023-2030 |
20 | Market Segmentation, Dynamics and Forecast by End use, 2023-2030 |
21 | Product installation rate by OEM, 2023 |
22 | Incline/Decline in Average B-2-B selling price in past 5 years |
23 | Competition from substitute products |
24 | Gross margin and average profitability of suppliers |
25 | New product development in past 12 months |
26 | M&A in past 12 months |
27 | Growth strategy of leading players |
28 | Market share of vendors, 2023 |
29 | Company Profiles |
30 | Unmet needs and opportunity for new suppliers |
31 | Conclusion |
32 | Appendix |