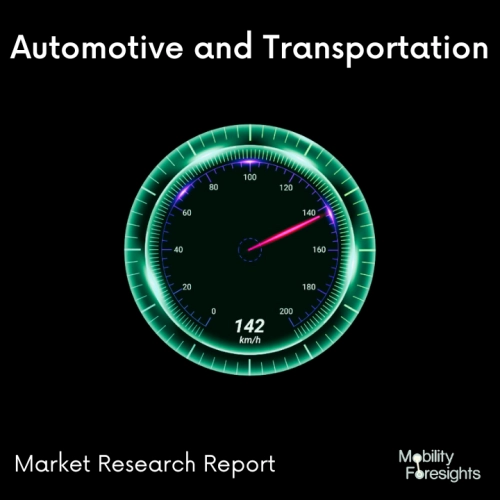
- Get in Touch with Us
Last Updated: Apr 26, 2025 | Study Period: 2023-2030
Micro injection molding is a molding technique used to create plastic parts with tolerances between 10 and 100 micrometres and shot weights between 1 and 0.1 grammes.
This molding technique enables the most accurate and precise fabrication of intricate tiny geometries.
The fundamental idea behind the micro injection molding technique is relatively similar to that of conventional injection molding. With this method, the injection molding machine incorporates a micro injection unit.
The method of plastic injection molding involves melting plastic pellets (thermosetting/thermoplastic polymers) that, once flexible enough, are injected at pressure into a mold cavity, filling it and solidifying it to create the finished product.
Rapid injection molding is a technology-driven procedure used by Protolabs that makes use of factory automation.
Direct delivery of CAD models to the manufacturing floor is where mold milling gets started, but most of the time, aluminium rather than steel is used to make the molds.
When compared to conventional steel molds, this enables tooling that is faster and more cost-effective. At Proto Labs, the thermoplastic injection molding procedure is a regular procedure utilising an aluminium mold.
Metals like aluminium don't need cooling channels since they transmit heat much more effectively than steel does. In a barrel, resin pellets are loaded before being melted, squeezed, and fed into the mold's runner system.
The item is molded after hot resin is shot through the gates into the mold chamber.
The Global EV Micro Injection Molded Plastic market accountedfor $XX Billion in 2022 and is anticipated to reach $XX Billion by 2030, registering a CAGR of XX% from 2023 to 2030.
The market for micro injection molding machines is anticipated to grow from USD 381 million in 2021 to USD 609 million in 2026, at a CAGR of 9.8%.
The expansion of the automotive industry and the increase in demand from medical applications are the main drivers of this market.
The demand for extremely accurate molds that are effective for performing medical procedures is being driven by the shift towards nanotechnology and miniaturisation in the medical industry.
The growing automation of automobiles and the development of electric cars are also driving up the demand for high-precision parts to improve performance.
The main barrier to market growth is the high investment costs associated with all-electric machines' high level of technology. The pricey maintenance is yet another drawback.
For producers of plastic packaging, the development of a circular economy, rising energy costs, and shifting customer demands present significant hurdles.
A new Packaging Center has been developed by ENGEL, a producer of injection molding machines, to assist its clients in this challenging sector in further enhancing production cell performance and ensuring their competitiveness.
Over 300 foreign visitors arrived in Austria in mid-May for the opening of the new Technology and Expertise Centre.
There are two locations, Schwertberg and St. Valentin, that have production cells that are suitable for use with a wide range of packaging requirements.
These include dual speed dual-platen machines for big containers, e-speed machines for thin-walled containers and pails, and all-electric e cap high-performance equipment for making caps and flip-top lids.
Sl no | Topic |
1 | Market Segmentation |
2 | Scope of the report |
3 | Abbreviations |
4 | Research Methodology |
5 | Executive Summary |
6 | Introduction |
7 | Insights from Industry stakeholders |
8 | Cost breakdown of Product by sub-components and average profit margin |
9 | Disruptive innovation in the Industry |
10 | Technology trends in the Industry |
11 | Consumer trends in the industry |
12 | Recent Production Milestones |
13 | Component Manufacturing in US, EU and China |
14 | COVID-19 impact on overall market |
15 | COVID-19 impact on Production of components |
16 | COVID-19 impact on Point of sale |
17 | Market Segmentation, Dynamics and Forecast by Geography, 2023-2030 |
18 | Market Segmentation, Dynamics and Forecast by Product Type, 2023-2030 |
19 | Market Segmentation, Dynamics and Forecast by Application, 2023-2030 |
20 | Market Segmentation, Dynamics and Forecast by End use, 2023-2030 |
21 | Product installation rate by OEM, 2023 |
22 | Incline/Decline in Average B-2-B selling price in past 5 years |
23 | Competition from substitute products |
24 | Gross margin and average profitability of suppliers |
25 | New product development in past 12 months |
26 | M&A in past 12 months |
27 | Growth strategy of leading players |
28 | Market share of vendors, 2023 |
29 | Company Profiles |
30 | Unmet needs and opportunity for new suppliers |
31 | Conclusion |
32 | Appendix |