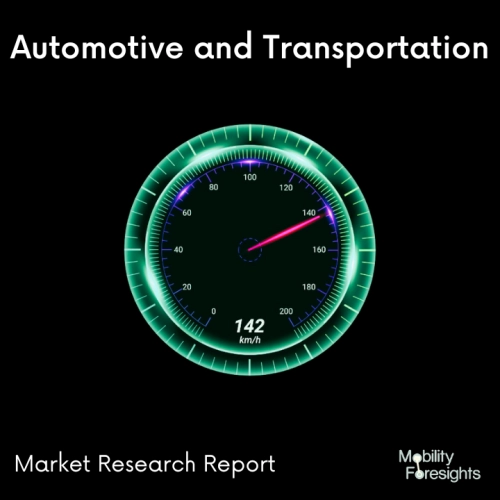
- Get in Touch with Us
Last Updated: Apr 25, 2025 | Study Period: 2023-2030
Insulation polymer composites are used in electrical equipment to support and separate electrical conductors without allowing current to pass through the insulators.
Silicone rubber is the most widely used polymeric insulation material for high voltage products. Insulation polymer composites have a core composed of a fiberglass rod covered by polymer weather sheds.
Manufactures use various shed materials, designs, and construction methods. Basic polymer shed materials used are silicone rubber, EPM, EPDM, CE, and polytetrafluroethylene (PTFE or Teflon).
The automotive sector is undergoing a significant transformation to address critical challenges affecting consumers and the climate.
One of the most difficult tasks is reducing the weight of vehicles in order to minimize energy consumption. A ten percent decrease in curb weight is predicted to result in a six to eight percent reduction in energy consumption.
Composite materials having better strength to weight ratio are one of the finest options for planning, designing and manufacturing of the lightweight components.
In automobile sector, employment of composite materials would reduce the weight of electric vehicles as well as influence their aerodynamic properties.
Therefore, it would decrease the consumption of fuel as well by cutting down harmful emissions and particulate matter.
Numerous developments in such technologies are studied over the last decade by automobile establishments and academic researchers.
Fiber-reinforced polymers, particularly those established on glass and carbon fibers, have attracted attention of the automobile sector due to their high performance and lesser weight
The Global EV Motor Insulation polymer composites market accounted for $XX Billion in 2022 and is anticipated to reach $XX Billion by 2030, registering a CAGR of XX% from 2023 to 2030.
JEC company launches ultra-light, low carbon âaerogelâ insulation polymer composites
University of Bath spin-out company Aerogel Core Ltd set to develop next generation materials for the aerospace and automotive industries.
A team of engineers from the University of Bath has created a new company, Aerogel Core Ltd, specialising in ultra-light âaerogelsâ that can be used as soundproofing and heat-shielding materials for the aerospace and automotive industries.
As well as tuneable acoustic properties, ultralight aerogels have other functional properties such as thermal, fire and electromagnetic interference shielding.
The coupling of both acoustic and other functional properties provides a material that can have a large impact within many industrial sectors.
In particular, the material meets the functionalities of specific engineering applications for the aerospace sector, creating the best acoustic properties for a material with incredibly low density.
Sl no | Topic |
1 | Market Segmentation |
2 | Scope of the report |
3 | Abbreviations |
4 | Research Methodology |
5 | Executive Summary |
6 | Introduction |
7 | Insights from Industry stakeholders |
8 | Cost breakdown of Product by sub-components and average profit margin |
9 | Disruptive innovation in the Industry |
10 | Technology trends in the Industry |
11 | Consumer trends in the industry |
12 | Recent Production Milestones |
13 | Component Manufacturing in US, EU and China |
14 | COVID-19 impact on overall market |
15 | COVID-19 impact on Production of components |
16 | COVID-19 impact on Point of sale |
17 | Market Segmentation, Dynamics and Forecast by Geography, 2023-2030 |
18 | Market Segmentation, Dynamics and Forecast by Product Type, 2023-2030 |
19 | Market Segmentation, Dynamics and Forecast by Application, 2023-2030 |
20 | Market Segmentation, Dynamics and Forecast by End use, 2023-2030 |
21 | Product installation rate by OEM, 2023 |
22 | Incline/Decline in Average B-2-B selling price in past 5 years |
23 | Competition from substitute products |
24 | Gross margin and average profitability of suppliers |
25 | New product development in past 12 months |
26 | M&A in past 12 months |
27 | Growth strategy of leading players |
28 | Market share of vendors, 2023 |
29 | Company Profiles |
30 | Unmet needs and opportunity for new suppliers |
31 | Conclusion |
32 | Appendix |