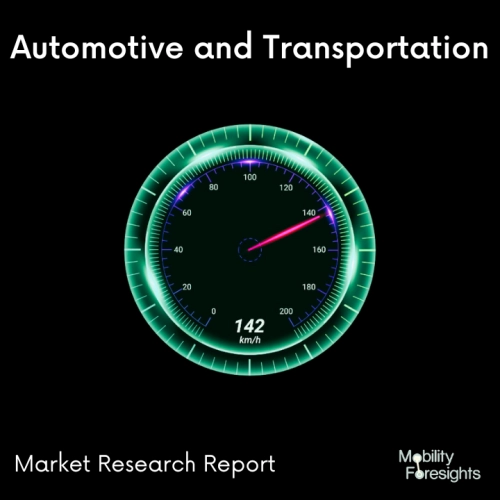
- Get in Touch with Us
Last Updated: Apr 25, 2025 | Study Period: 2023-2030
Permanent magnet synchronous motors (PMSMs) are frequently used in electric vehicles (EVs) for propulsion. To produce torque and power, these motors rely on the interaction of the spinning magnetic field created by the motor's stator with the magnetic field created by the permanent magnets.
The bonding of the permanent magnets to the motor's rotor is one of the crucial phases in the manufacture of PMSMs. The performance, efficiency, and dependability of the motor are all determined by this process, which is essential.
Both approaches have benefits and drawbacks. Better motor performance is obtained through adhesive bonding because it is a more flexible approach and permits more exact control over the magnet location.
Yet, automating it might be more expensive and difficult. Although mechanical retention is a simpler and more automatable method, it may lead to less accurate magnet placement and may be less dependable in high-speed applications.
In general, the application of the motor, the required performance, and the manufacturing process all influence the choice of bonding method. To get the best outcomes, manufacturers may combine the two techniques.
Global EV motor magnet bonding market accounted for $XX Billion in 2022 and is anticipated to reach $XX Billion by 2030, registering a CAGR of XX% from 2023 to 2030.
A new magnet bonding glue solution from 3M has been unveiled; it is intended to largely replace messy liquid adhesives, ease magnet positioning, and provide high bond strength with control over bond line thickness.
The 3M motor Magnet Bonding AU-205 system is a low-tack double-sided tape that combines a modified structural epoxy adhesive with a thickness control system. It claims to provide strong chemical resistance and binding strength in an easy-to-convert tape form that complies with RoHS and REACH regulations and doesn't include any volatile organic components.
The permanent magnet bond line thickness, which is essential to motor performance, may now be better controlled, according to 3m's claim about AU-205. The air gap is the space that exists between the outside diameter of the rotor and the internal diameter of the stator. A PM motor can operate more efficiently if the rotor/stator air gap is precisely managed and minimised.
Sl no | Topic |
1 | Market Segmentation |
2 | Scope of the report |
3 | Abbreviations |
4 | Research Methodology |
5 | Executive Summary |
6 | Introduction |
7 | Insights from Industry stakeholders |
8 | Cost breakdown of Product by sub-components and average profit margin |
9 | Disruptive innovation in the Industry |
10 | Technology trends in the Industry |
11 | Consumer trends in the industry |
12 | Recent Production Milestones |
13 | Component Manufacturing in US, EU and China |
14 | COVID-19 impact on overall market |
15 | COVID-19 impact on Production of components |
16 | COVID-19 impact on Point of sale |
17 | Market Segmentation, Dynamics and Forecast by Geography, 2023-2030 |
18 | Market Segmentation, Dynamics and Forecast by Product Type, 2023-2030 |
19 | Market Segmentation, Dynamics and Forecast by Application, 2023-2030 |
20 | Market Segmentation, Dynamics and Forecast by End use, 2023-2030 |
21 | Product installation rate by OEM, 2023 |
22 | Incline/Decline in Average B-2-B selling price in past 5 years |
23 | Competition from substitute products |
24 | Gross margin and average profitability of suppliers |
25 | New product development in past 12 months |
26 | M&A in past 12 months |
27 | Growth strategy of leading players |
28 | Market share of vendors, 2023 |
29 | Company Profiles |
30 | Unmet needs and opportunity for new suppliers |
31 | Conclusion |
32 | Appendix |