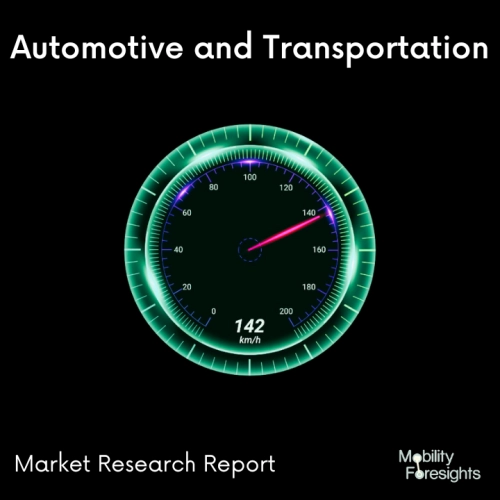
- Get in Touch with Us
Last Updated: Apr 25, 2025 | Study Period: 2024-2030
EV Motor mounts are an efficient means of isolating motor vibrations, dampening road excitations, and supporting stability. Drive trains for commercial vehicles are a major source of vibrations due to their substantial weight and strong torques.
Commercial vehicle motor mounts from Vibracoustic help to lessen noise and vibration, can bear high loads and torques, guarantee dependable operation, and are weight-optimized. Electric commercial vehicle motor mounts offer both static and dynamic dampening, and the resonance frequency can be accurately adjusted.
The Global EV motor mount market accounted for $XX Billion in 2022 and is anticipated to reach $XX Billion by 2030, registering a CAGR of XX% from 2024 to 2030.
Demands for electric mount powertrains over traditional fuel engines are growing as a result of huge developments in automotive technology. In terms of cleaner and quieter operation, the electric powertrain has benefits. An electric motor powered by batteries replaces the traditional engine in an electric vehicle.
The term "conventional engine" in this context refers to power sources like diesel, gasoline, compressed natural gas (CNG), and some hybrid vehicles. As a result, the system design strategy for mount also changes.
Currently, a variety of methods are used to install electric powertrains, including the traditional pendulum type, with or without a cradle, common or unique motor and electric box mountings, etc.
Consequently, NVH criteria for electric powertrains may not be met by conventional mount. Because electric motors are more noise-free than IC engines, the little vibration problem increased the amount of engine noise in the passenger compartment. It is possible to isolate the system to prevent resonance by carefully placing all important EV components in their respective modes.
The systems employed are solely modified for the new application and are based on combustion engines for mounting electric powertrains. It follows that mounting systems that are designed for use with combustion engines may not always be the optimum option for electric powertrains.
An electric powertrain mounting design strategy is given. An example of a car with a traditional powerplant mounting that has been converted to an electric powertrain is provided. To determine the ideal stiffness that correlates with actual measured NVH values, the mount stiffness optimization method using multibody dynamics and HEEDS software is applied.
EV MOTOR MOUNT MARKETTHIS REPORT WILL ANSWER FOLLOWING QUESTIONS
Sl no | Topic |
1 | Market Segmentation |
2 | Scope of the report |
3 | Abbreviations |
4 | Research Methodology |
5 | Executive Summary |
6 | Introduction |
7 | Insights from Industry stakeholders |
8 | Cost breakdown of Product by sub-components and average profit margin |
9 | Disruptive innovation in the Industry |
10 | Technology trends in the Industry |
11 | Consumer trends in the industry |
12 | Recent Production Milestones |
13 | Component Manufacturing in US, EU and China |
14 | COVID-19 impact on overall market |
15 | COVID-19 impact on Production of components |
16 | COVID-19 impact on Point of sale |
17 | Market Segmentation, Dynamics and Forecast by Geography, 2024-2030 |
18 | Market Segmentation, Dynamics and Forecast by Product Type, 2024-2030 |
19 | Market Segmentation, Dynamics and Forecast by Application, 2024-2030 |
20 | Market Segmentation, Dynamics and Forecast by End use, 2024-2030 |
21 | Product installation rate by OEM, 2023 |
22 | Incline/Decline in Average B-2-B selling price in past 5 years |
23 | Competition from substitute products |
24 | Gross margin and average profitability of suppliers |
25 | New product development in past 12 months |
26 | M&A in past 12 months |
27 | Growth strategy of leading players |
28 | Market share of vendors, 2023 |
29 | Company Profiles |
30 | Unmet needs and opportunity for new suppliers |
31 | Conclusion |
32 | Appendix |