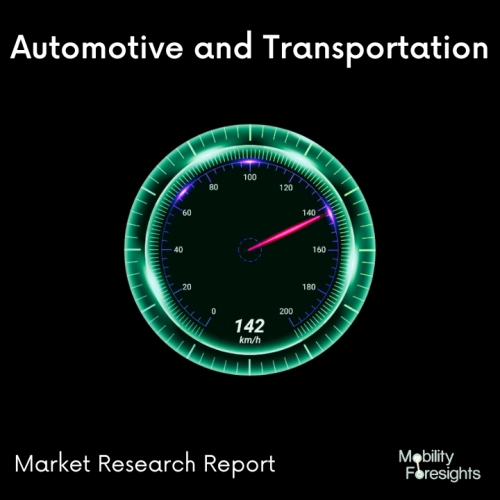
- Get in Touch with Us
Last Updated: Apr 25, 2025 | Study Period: 2023-2030
In the field of electronics, potting is the process of covering an entire electronic assembly with a solid or gelatinous substance to protect it against gaseous phenomena like corona discharge, shock, and vibration, as well as water, moisture, and corrosive substances.
The most popular materials used by fabricators for potting electronics are epoxy and urethane. They provide the electronics they cover with a tremendous level of protection because of their extreme hardness.
Urethanes can withstand temperatures of up to 180 °F, but epoxy materials can often withstand temperatures of up to 250 °F, depending on the product.
Aluminum, boron, cobalt, copper, dysprosium, iron, neodymium, niobium, silicon steel, terbium, and praseodymium are among the materials expected to be used in motors. Aluminium, boron, cobalt, copper, dysprosium, iron, neodymium, niobium, silicon steel, terbium, and praseodymium are among the materials expected to be used in motors.
The regenerative braking system of an electric motor is a crucial component. By transforming the vehicle's kinetic energy into another form and storing it for later use, this system slows down the moving object.
The global EV motor potting compound market accounted for $XX Billion in 2022 and is anticipated to reach $XX Billion by 2030, registering a CAGR of XX% from 2023 to 2030.
There are several valid arguments in favour of potting electronics. The circuit board is protected from external factors including moisture in the air, caustic chemicals, and gases by being embedded in a potting compound (sulphur in particular attacks the copper used in the components and PCB tracks).
In addition to providing support and cushioning for delicate or fragile components, such as the brittle ferrites used in transformer cores, potting also provides protection against the impacts of mechanical shock and vibration. So that the strength of the pin connection to the circuit board is not solely dependent on the solder joints, it also supports and relieves much of the strain off the PCB pins.
Additionally, potting replaces the air surrounding a converter PCB with a highly insulating medium1, preventing arc-over in the power supply from over-voltage stress, which is especially dangerous at high altitudes, as well as the effects of pollution like moisture, dust, and dirt, which could weaken the insulation between the input and output or allow tracking to happen across surfaces.
In order to lessen the stress caused by temperature differences on the components, thermally conductive potting materials also prevent hotspots inside the converter by transporting heat away to the casing and levelling-out the thermal gradients. Finally, potting provides fire protection (UL94-V0) due to the compound's inability to ignite or sustain a flame after curing. A potted DC/DC converter also has a longer lifespan in terms of storage and operation.
Sl no | Topic |
1 | Market Segmentation |
2 | Scope of the report |
3 | Abbreviations |
4 | Research Methodology |
5 | Executive Summary |
6 | Introduction |
7 | Insights from Industry stakeholders |
8 | Cost breakdown of Product by sub-components and average profit margin |
9 | Disruptive innovation in the Industry |
10 | Technology trends in the Industry |
11 | Consumer trends in the industry |
12 | Recent Production Milestones |
13 | Component Manufacturing in US, EU and China |
14 | COVID-19 impact on overall market |
15 | COVID-19 impact on Production of components |
16 | COVID-19 impact on Point of sale |
17 | Market Segmentation, Dynamics and Forecast by Geography, 2023-2030 |
18 | Market Segmentation, Dynamics and Forecast by Product Type, 2023-2030 |
19 | Market Segmentation, Dynamics and Forecast by Application, 2023-2030 |
20 | Market Segmentation, Dynamics and Forecast by End use, 2023-2030 |
21 | Product installation rate by OEM, 2023 |
22 | Incline/Decline in Average B-2-B selling price in past 5 years |
23 | Competition from substitute products |
24 | Gross margin and average profitability of suppliers |
25 | New product development in past 12 months |
26 | M&A in past 12 months |
27 | Growth strategy of leading players |
28 | Market share of vendors, 2023 |
29 | Company Profiles |
30 | Unmet needs and opportunity for new suppliers |
31 | Conclusion |
32 | Appendix |