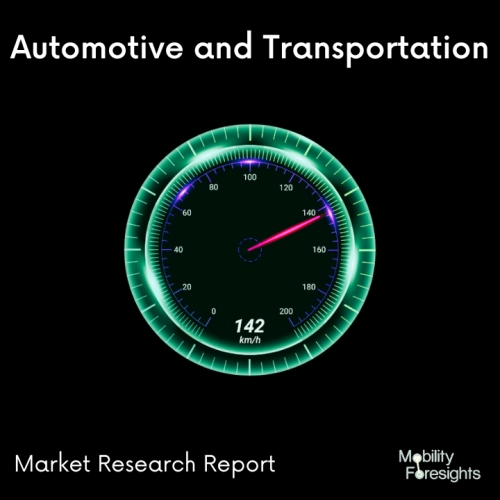
- Get in Touch with Us
Last Updated: Apr 25, 2025 | Study Period: 2023-2030
In both conventional and electric powertrains, the planetary carrier is a functional element that is essential for planetary transmissions. The planetary gears are fitted into what may be thought of as a cage.
The pinion gears will be pushed to revolve around the stationary sun gear and these pinions will revolve simultaneously on their own axes given by the carrier pins if the sun gear is prevented from spinning and the input shaft and planet carrier are rotated.
Due to the independent rotating movements of the planet carrier and the revolving planet gears, motion will be transferred from the carrier and pinion gears to the annulus ring gear. As a result, the annulus and therefore the output shaft will be forced to circle at a somewhat quicker speed.
A gear system made up of spur gears is known as a planetary gear. A centre gear, called a sun gear, serves as the input and driver of the set in planetary gearing (also known as epicyclic gearing).
The sun gear revolves around one or more planet-shaped "driven" gears. Finally, the planets construct an internal spur gear design by engaging a ring gear from the interior.
Planetary gear trains are renowned for being incredibly robust designs because the planet gears are equally distributed around the sun. A planetary gearset also has the advantage of being easily adaptable to other ratios by simply swapping out the carrier and sun gears.
In a planetary gearset, spur gears that rotate in the same plane in opposition to one another are used. Because they don't use specialised angles or cuts like bevel or herringbone gearing, spur gears are a more simple sort of gear in terms of engineering, but their tooth shape design is intricate.
This tooth design will define where the teeth make contact, which will then determine the available power, torque, and speed potential of the gears depending on the application.
The Global EV planetary carrier market accountedfor $XX Billion in 2022 and is anticipated to reach $XX Billion by 2030, registering a CAGR of XX% from 2023 to 2030.
The planetary carrier assembly demonstrates the cutting-edge design capabilities for improved performance from GKN, a pioneer in powder metal carrier technology. The assembly is a component of Ford Motor Company's 10-speed F-150 transmission.
The flanged hub component of the assembly has a special twist-lock mechanism that lowers stress in multiple places. This made it possible to reduce the fuel consumption of the transmission.
High stresses resulted because the transmission's space restrictions precluded a castellated design from handling the axial loading. Reducing the pressures while enhancing efficiency and fuel usage was GKN's challenge.The performance of the 10-speed transmission's shifting was significantly improved by weight reductions.
This worm planetary drive is meant to be utilised with bucket wheel reclaimers that are employed in tough, muddy, and dusty environments in crawler applications.
This type of application has severely unbalanced loading circumstances. output that is flawless High-radial-load situations are handled by roller bearings. Worm and worm wheel serve as the gearbox's input and are responsible for the electric motor's 90o transmission. The worm shaft's two ending inputs allow it to be used as either the LH or the RH.
Sl no | Topic |
1 | Market Segmentation |
2 | Scope of the report |
3 | Abbreviations |
4 | Research Methodology |
5 | Executive Summary |
6 | Introduction |
7 | Insights from Industry stakeholders |
8 | Cost breakdown of Product by sub-components and average profit margin |
9 | Disruptive innovation in the Industry |
10 | Technology trends in the Industry |
11 | Consumer trends in the industry |
12 | Recent Production Milestones |
13 | Component Manufacturing in US, EU and China |
14 | COVID-19 impact on overall market |
15 | COVID-19 impact on Production of components |
16 | COVID-19 impact on Point of sale |
17 | Market Segmentation, Dynamics and Forecast by Geography, 2023-2030 |
18 | Market Segmentation, Dynamics and Forecast by Product Type, 2023-2030 |
19 | Market Segmentation, Dynamics and Forecast by Application, 2023-2030 |
20 | Market Segmentation, Dynamics and Forecast by End use, 2023-2030 |
21 | Product installation rate by OEM, 2023 |
22 | Incline/Decline in Average B-2-B selling price in past 5 years |
23 | Competition from substitute products |
24 | Gross margin and average profitability of suppliers |
25 | New product development in past 12 months |
26 | M&A in past 12 months |
27 | Growth strategy of leading players |
28 | Market share of vendors, 2023 |
29 | Company Profiles |
30 | Unmet needs and opportunity for new suppliers |
31 | Conclusion |
32 | Appendix |