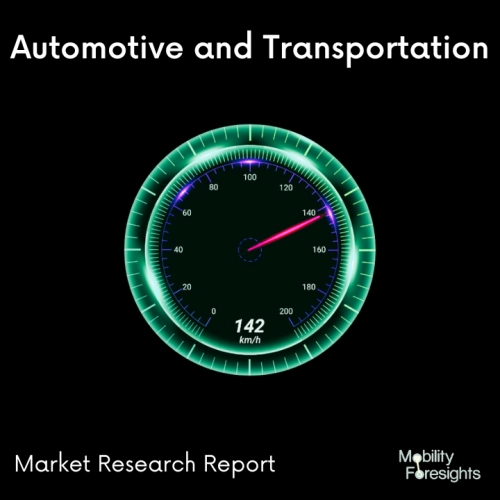
- Get in Touch with Us
Last Updated: Apr 25, 2025 | Study Period: 2024-2030
The powertrain is made up of a variety of components that cooperate to propel a vehicle forward by generating power from the engine and transferring it to the wheels. Drivetrain and powertrain are sometimes used interchangeably, although the drivetrain is just a word for all components of the powertrain that are unrelated to the engine.
The primary parts of the powertrain are:Engine: The engine is what powers the vehicle. It has pistons inside the cylinders that move up and down to ignite the combustion process.
Transmission: The transmission converts the engine's rotation into usable energy by adjusting the engine's output to the driving environment using a variety of gears and clutches.riveshaft: The driveshaft is where the torqueâthe force an engine produces while it rotatesâis delivered to the differential.
Differential: The differential, which is a component of either the front or rear axle assemblies, aids in the efficient turning of a vehicle. It makes advantage of the driveshaft's torque and transfers it to the wheels, enabling them to rotate at various rates.
Axles: Axle assemblies sustain a vehicle's weight and transfer engine power to the wheels while being situated in between the vehicle's wheels.
One or more electric motors are used in an electric vehicle (EV) to provide propulsion. Electricity from extravehicular sources, a collector system, or a battery can all be used to power it (sometimes charged by solar panels, or by converting fuel to electricity using fuel cells or a generator).
A renewed interest in an electric transportation infrastructure emerged in the latter half of the 20th and the beginning of the 21st centuries as a result of the negative environmental effects of the petroleum-based transportation infrastructure and the concern of peak oil.
Electric vehicles (EVs) differ from conventional cars in that the electricity they use can be produced using a variety of fuels, including nuclear power, renewable energy sources like solar and wind power, or any combination of those. The carbon footprint and other emissions of electric vehicles varies depending on the fuel and technology utilized for energy generation.
The Global EV Powertrain Plastics market accounted for $XX Billion in 2022 and is anticipated to reach $XX Billion by 2030, registering a CAGR of XX% from 2024 to 2030.
To extend vehicle range, the new generation of electric and hybrid vehicles must be lighter and stronger. The specific application areas of electric vehicles, such as electric motors, battery thermal management, and chassis, are where automotive OEMs concentrate more of their attention.
These conversions are made possible by a number of applications for metal replacement in different under-the-hood components employing high-performance plastic materials, primarily polyamide-based polymers, with the advantages of high tensile strength, high-temperature resistance, and lightness.
Higher voltages can be safely accommodated by thermally conductive polymers used in electric vehicle battery housings and LED casings. Additionally, they provide more possibilities for light writhing, are more adaptable, and may produce heat management systems that are more uniform.
Polyamides have great opportunities in battery trays and connectors in electric vehicles, as electric cars have many sensors, cameras, and radars. The connectors are molded from Polyamide due to their temperature resistance property.
Manufacturers such as BASF use special polyamide and polybutylene terephthalate grades that meet the demands for flame retardancy, color stability, and electrical isolation. This allows BASF to save weight and installation space around the battery pack and improve the vehicleâs safety. Thus, the demand for thermally stable plastic is increasing in the electric & hybrid vehicle segment.
Sl no | Topic |
1 | Market Segmentation |
2 | Scope of the report |
3 | Abbreviations |
4 | Research Methodology |
5 | Executive Summary |
6 | Introduction |
7 | Insights from Industry stakeholders |
8 | Cost breakdown of Product by sub-components and average profit margin |
9 | Disruptive innovation in the Industry |
10 | Technology trends in the Industry |
11 | Consumer trends in the industry |
12 | Recent Production Milestones |
13 | Component Manufacturing in US, EU and China |
14 | COVID-19 impact on overall market |
15 | COVID-19 impact on Production of components |
16 | COVID-19 impact on Point of sale |
17 | Market Segmentation, Dynamics and Forecast by Geography, 2024-2030 |
18 | Market Segmentation, Dynamics and Forecast by Product Type, 2024-2030 |
19 | Market Segmentation, Dynamics and Forecast by Application, 2024-2030 |
20 | Market Segmentation, Dynamics and Forecast by End use, 2024-2030 |
21 | Product installation rate by OEM, 2023 |
22 | Incline/Decline in Average B-2-B selling price in past 5 years |
23 | Competition from substitute products |
24 | Gross margin and average profitability of suppliers |
25 | New product development in past 12 months |
26 | M&A in past 12 months |
27 | Growth strategy of leading players |
28 | Market share of vendors, 2023 |
29 | Company Profiles |
30 | Unmet needs and opportunity for new suppliers |
31 | Conclusion |
32 | Appendix |