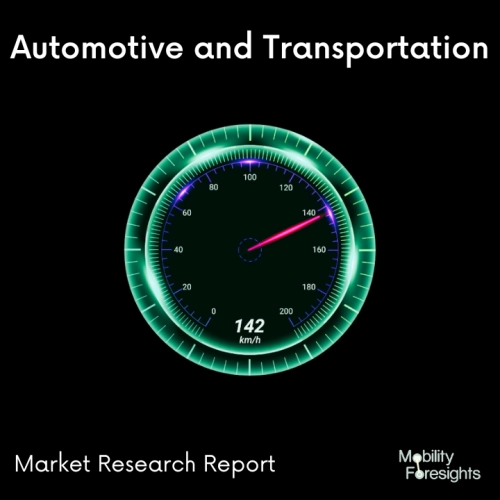
- Get in Touch with Us
Last Updated: Apr 25, 2025 | Study Period: 2024-2030
Plastic is both an insulator and a conductor of electricity. As a result, it has special functions in batteries, alternative drivetrains, and propulsion. There is increasing pressure on the world stage to continue cutting greenhouse gas (GHG) emissions.
During battery validation testing, EV manufacturers use displacement or LVDT (linear variable differential transformer) sensors to assess pouch and prismatic cell swelling. Lithium-ion (Li-ion), Nickel Manganese Cobalt (NMC), Nickel Metal Hydride (Ni-MH), Lithium Sulphur (Li-S), and Lead-Acid are the most popular battery chemistries for electric vehicles.
In place of Lithium-ion batteries, nickel-metal hydride batteries are frequently used in hybrid vehicles. Sensors are essential for keeping track of an EV's systems and ensuring that they are running smoothly at all times.
More than 100 unique sensors may be present in high-end EVs to track and control temperature, pressure, and component operation.
The Global EV Sensor plastics market accounted for $XX Billion in 2023 and is anticipated to reach $XX Billion by 2030, registering a CAGR of XX% from 2024 to 2030.
The global automobile industry is facing its greatest threat in the last forty years with the rise of electric vehicles (EVs).
As existing internal combustion, powertrain manufacturing equipment, and technology gradually experience lesser investment by automobile Original Equipment Manufacturers, the current fledgling EV transition will reach its apex (OEMs).
In order to take advantage of these enormous new electrical and electronic, plastic-to-metal conversion, and lightning prospects, major supply chains will need to be reconfigured. New plastic material systems will be required for EV cooling systems that remain in use both throughout driving and charging cycles, at greater voltage levels, with enhanced flame retardance, as well as increased operating temperatures for longer times.
New battery materials that have been adapted to lightweighting will also contribute to EV driving range on a single charge. Last but not least, future autonomous EVs will open up a vast new market for specialised plastic sensor materials.
In the automotive Electric Vehicle (EV) market, new plastic materials are being developed that will be a major technical market driver from 2020 to 2035.
The growth of thermoplastic composites in electric vehicles (EVs) and internal combustion engines (ICEVs) as well as enhanced under-the-hood, high heat, high performance metal-to-plastic conversion applications will coincide with this transition.
One of the top providers of electronic parts and services to the automobile sector is Molex, which offers plastic parts for EV sensors. The MX123 Connector System is one of their primary product categories in this field. The MX123 Connector System is intended for ruggedized, high-performance applications in challenging settings.
It is a high-density, modular connection technology that enables simple modification and design flexibility. In order to guarantee dependability in difficult conditions, the system comes with a choice of connector types, including wire-to-wire, wire-to-board, and wire-to-panel possibilities.
Battery management systems, electric power steering systems, and motor control units are just a few of the EV sensor applications that the MX123 Connector System is perfect for. The system is made to endure high heat, vibration, and moisture, making it suitable for usage in the harsh conditions seen in automotive applications.
Molex provides a variety of sensor housings and cable assemblies for EV sensor applications in addition to the MX123 Connector System. Their sensor housings are made to match the needs of certain applications and are intended to shield sensors from environmental threats. They provide a variety of lengths and configurations of cable assemblies that are made to transmit signals reliably in highly vibrating settings.
In addition to providing high-performance, ruggedized solutions for use in demanding automotive applications, Molex is a dependable provider of plastic parts for EV sensors. A few examples of the cutting-edge goods they provide to help the expanding EV sector are their MX123 Connector System, sensor housings, and cable assemblies.
TE Connectivity is a multinational technology business with a focus on creating electrical products and solutions for a range of markets, including the car sector. TE Connectivity provides a wide selection of products made specifically to satisfy the demands of electric vehicles when it comes to plastic parts for EV sensors. The AMP+ HVA 280 High-Voltage Connector System is one of TE Connectivity's most well-liked plastic EV sensor parts.
This item is perfect for EV sensors because it is made for usage in high-voltage situations. The connecting system has a durable construction that can endure extreme weather and high levels of vibration. Additionally, it features a high level of sealing to safeguard against dust and moisture. Additionally, TE Connectivity provides a selection of sensor housings tailored for EV sensors.
These housings, which are built of sturdy materials, are intended to shield sensors from elements like water, dust, and vibration. The housings may be altered to match particular client needs and come in a variety of sizes and forms to accommodate various sensor types.
The Miniaturized Coaxial Interconnect System (MCIS), another item provided by TE Connectivity, is made for use in high-frequency applications. For use in EV sensors that need high-speed data transfer, the MCIS is a compact, lightweight connection system. It has a low-profile design that saves space and a strong locking mechanism to assure dependable communication.
Overall, TE Connectivity provides a comprehensive selection of plastic EV sensor parts that are created to specifically satisfy the demands of electric cars. For practically every application, TE Connectivity offers a solution, including high-voltage connectors, sensor housings, and cable assemblies.
Sl no | Topic |
1 | Market Segmentation |
2 | Scope of the report |
3 | Abbreviations |
4 | Research Methodology |
5 | Executive Summary |
6 | Introduction |
7 | Insights from Industry stakeholders |
8 | Cost breakdown of Product by sub-components and average profit margin |
9 | Disruptive innovation in the Industry |
10 | Technology trends in the Industry |
11 | Consumer trends in the industry |
12 | Recent Production Milestones |
13 | Component Manufacturing in US, EU and China |
14 | COVID-19 impact on overall market |
15 | COVID-19 impact on Production of components |
16 | COVID-19 impact on Point of sale |
17 | Market Segmentation, Dynamics and Forecast by Geography, 2023-2030 |
18 | Market Segmentation, Dynamics and Forecast by Product Type, 2023-2030 |
19 | Market Segmentation, Dynamics and Forecast by Application, 2023-2030 |
20 | Market Segmentation, Dynamics and Forecast by End use, 2023-2030 |
21 | Product installation rate by OEM, 2023 |
22 | Incline/Decline in Average B-2-B selling price in past 5 years |
23 | Competition from substitute products |
24 | Gross margin and average profitability of suppliers |
25 | New product development in past 12 months |
26 | M&A in past 12 months |
27 | Growth strategy of leading players |
28 | Market share of vendors, 2023 |
29 | Company Profiles |
30 | Unmet needs and opportunity for new suppliers |
31 | Conclusion |
32 | Appendix |