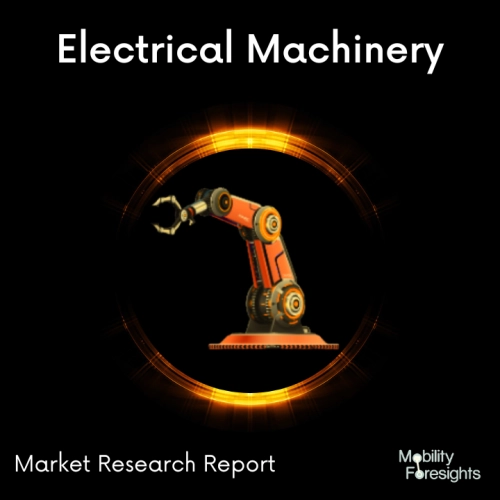
- Get in Touch with Us
Last Updated: Apr 25, 2025 | Study Period: 2023-2030
When an electric motor can contain an internal explosion without rupturing and putting the entire industrial facility in danger, it is said to be explosion-proof.
An explosion proof design contains the internal combustion to prevent a greater explosion or fire when a spark ignites volatile gas within a motor.
A nameplate clearly identifies an explosion-proof motor's suitability for a given hazardous environment. an enclosure for a motor that can withstand and contain an explosion inside. Pathways for flame exhaust that control the flames and let hot gases out of the enclosure.
No surface that is higher than the vapor, gas, or dust's lowest auto-ignition temperature in the expected environment.
Suitable for explosive and risky situations, with excellent sealing performance and reduced accident risk. Explosion-proof motors are required for industrial applications that require highly combustible, omnipresent materials.
A motor that is explosion-proof does not guarantee that it will never explode or that it will not be affected by explosions from outside.
On the other hand, an explosion-proof motor has features that prevent a larger, combustible environment from being ignited by an internal motor explosion.
Explosion-proof motors are required for hazardous applications like distilleries, biodiesel plants, gas applications, grain elevators, and chemical plants.
TheGlobal Explosion Proof Brake Motor marketaccounted for $XX Billion in 2022 and is anticipated to reach $XX Billion by 2030, registering a CAGR of XX% from 2023 to 2030.
An improvement to a conventional explosion-proof electric brake motor is included in this invention.
The motor housing is attached to an electrical conduit, the brake housing is secured to the motor housing and has an electrical attached to it, and the flange is attached to the motor housing and is designed to secure the motor to a drive mounting for driving a shaft.
A waterproof means for the first housing is added between the brake housing and the motor housing in the improvement.
In order to secure the brake electrical conduit to the brake housing, a first conduit waterproofing method has been developed.
The motor electrical conduit is sealed to the motor housing using a second waterproofing method. The flange can be sealed to the motor housing using an adapted waterproofing method.
As a result, the waterproofing methods and conventional electric brake motor combine to create an explosion-proof brake motor that can be submerged.
The present invention's method and apparatus are generally related to a method and apparatus for making electric submersible brake motors.
More specifically, it relates to an explosion-proof electric brake motor that is waterproof, as well as an apparatus and method for modifying a commercial electric brake motor so that it can operate in both an environment where explosive gases are present and an environment where it is submerged.
Hydrogen sulfide, methane, and other similar gases are typical explosive gas environments in which the brake motor can be used.
Having a brake motor that is able to function in both explosive and submerged environments is desirable in a number of different operating conditions.
One such climate is in sewage treatment activities. A bar rack screen is inserted into the flow stream during such operations to collect debris.
Vulcan Industries, based in Missouri Valley, Iowa, manufactures one such bar rack screen known as the "Mensch Screen."
The screen is cleaned of any debris that has collected using a scraper that is powered by an electric brake motor. Methane, hydrogen sulfide, and other explosive gases are frequently produced in these kinds of environments.
Additionally, the scraper brake motor may temporarily submerge depending on the depth of the flow stream. As a result, having a brake motor that can operate in both explosive and submerged conditions may be desirable.
Sl no | Topic |
1 | Market Segmentation |
2 | Scope of the report |
3 | Abbreviations |
4 | Research Methodology |
5 | Executive Summary |
6 | Introduction |
7 | Insights from Industry stakeholders |
8 | Cost breakdown of Product by sub-components and average profit margin |
9 | Disruptive innovation in the Industry |
10 | Technology trends in the Industry |
11 | Consumer trends in the industry |
12 | Recent Production Milestones |
13 | Component Manufacturing in US, EU and China |
14 | COVID-19 impact on overall market |
15 | COVID-19 impact on Production of components |
16 | COVID-19 impact on Point of sale |
17 | Market Segmentation, Dynamics and Forecast by Geography, 2023-2030 |
18 | Market Segmentation, Dynamics and Forecast by Product Type, 2023-2030 |
19 | Market Segmentation, Dynamics and Forecast by Application, 2023-2030 |
20 | Market Segmentation, Dynamics and Forecast by End use, 2023-2030 |
21 | Product installation rate by OEM, 2023 |
22 | Incline/Decline in Average B-2-B selling price in past 5 years |
23 | Competition from substitute products |
24 | Gross margin and average profitability of suppliers |
25 | New product development in past 12 months |
26 | M&A in past 12 months |
27 | Growth strategy of leading players |
28 | Market share of vendors, 2023 |
29 | Company Profiles |
30 | Unmet needs and opportunity for new suppliers |
31 | Conclusion |
32 | Appendix |