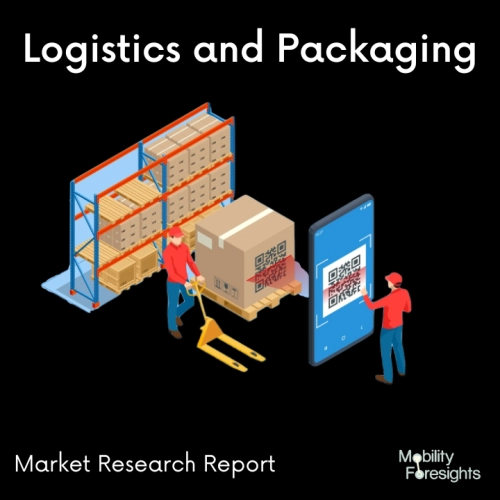
- Get in Touch with Us
Last Updated: Apr 25, 2025 | Study Period: 2023-2030
One of the world's strongest natural fibres is flax fibre material. It has been used to a variety of materials, including linen and even the mummy wraps. Flax fibre is the ideal material for food packaging solutions because of its strength, heat resistance, and biodegradability.
So, it is now appropriate for businesses to employ packaging made of Flex Fiber Material. The flax plant yields a natural cellulosic fibre known as flax fibre. Farmers collect flax fibre from the flax plant's surface below. Flax can be used for numerous things, including rope, tea bags, and currency.
This demonstrates the material's adaptability. Heat conductivity: Flax fibre has a high thermal conductivity. Also extremely resistant to deterioration at 120 degrees Celsius One of the strongest natural fibres is a strong material. more durable than cotton fibres. Tenacity ranges between 6.5 and 8 gm/denier.
Strong and resistant to bending, flax fibre material has a high degree of stiffness. Since flax fibre is derived from a plant, it is an environmentally beneficial material.
This indicates that flax fibre is a biodegradable substance that can degrade when crushed and exposed to germs. Additionally, flax fibre material can be recycled, preventing the requirement for landfills to hold the material.
The Global Flax fiber Packaging market accounted for $XX Billion in 2022 and is anticipated to reach $XX Billion by 2030, registering a CAGR of XX% from 2023 to 2030.
For original equipment manufacturers of automobiles, Cobra Advanced Composites, the automotive division of composite products producer Cobra International, has launched a line of production-ready, flax fiber-based, visual finish components. Compared to conventional carbon-look aesthetic components, the new natural fibre composite solutions offer a sustainable alternative.
According to a news release from CAC, the company has been providing aesthetic carbon fibre prepreg parts to vehicle OEMs since 2006. Manufacturers have asked CAC to create alternative composite technologies utilising more sustainable materials as new European regulatory goals rapidly approach.
The new components were made by CAC using autoclave-processed flax fibre prepregs. Low-density flax fibres, which need significantly less energy to generate than carbon provide excellent vibration damping and outstanding impact resistance, making them appropriate for a wide range of parts, including both interior and exterior parts.
Sl no | Topic |
1 | Market Segmentation |
2 | Scope of the report |
3 | Abbreviations |
4 | Research Methodology |
5 | Executive Summary |
6 | Introduction |
7 | Insights from Industry stakeholders |
8 | Cost breakdown of Product by sub-components and average profit margin |
9 | Disruptive innovation in the Industry |
10 | Technology trends in the Industry |
11 | Consumer trends in the industry |
12 | Recent Production Milestones |
13 | Component Manufacturing in US, EU and China |
14 | COVID-19 impact on overall market |
15 | COVID-19 impact on Production of components |
16 | COVID-19 impact on Point of sale |
17 | Market Segmentation, Dynamics and Forecast by Geography, 2023-2030 |
18 | Market Segmentation, Dynamics and Forecast by Product Type, 2023-2030 |
19 | Market Segmentation, Dynamics and Forecast by Application, 2023-2030 |
20 | Market Segmentation, Dynamics and Forecast by End use, 2023-2030 |
21 | Product installation rate by OEM, 2023 |
22 | Incline/Decline in Average B-2-B selling price in past 5 years |
23 | Competition from substitute products |
24 | Gross margin and average profitability of suppliers |
25 | New product development in past 12 months |
26 | M&A in past 12 months |
27 | Growth strategy of leading players |
28 | Market share of vendors, 2023 |
29 | Company Profiles |
30 | Unmet needs and opportunity for new suppliers |
31 | Conclusion |
32 | Appendix |