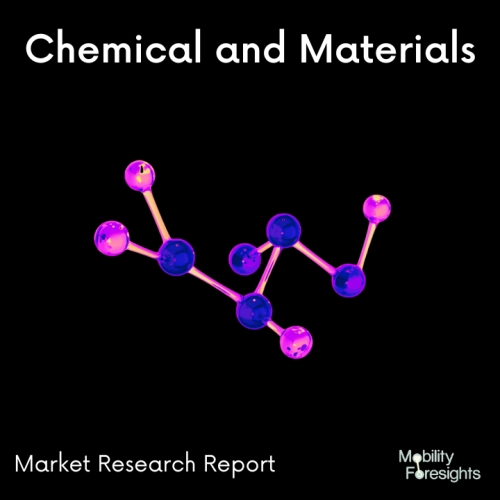
- Get in Touch with Us
Last Updated: Apr 25, 2025 | Study Period: 2024-2030
Hexafluoropropylene and tetrafluoroethylene are copolymers to create fluorinated ethylene propylene (FEP). In contrast to polytetrafluoroethylene resins, it can be melt-processed using standard injection molding and screw extrusion methods. The composition of FEP and the fluoropolymers PTFE and PFA are very similar.
Despite being more easily formable, FEP and PFA both have PTFE's advantageous characteristics of minimal friction and non-reactivity. FEP is more transparent than PTFE, melts at 260 °C, and is resistant to sunlight. Tetrafluoroethylene and hexafluoropropylene combinations are free-radical polymerized to form FEP.
The mixture is biased to make up for the propylene component's comparatively poor reactivity. Peroxydisulfate, which homolyzes to produce sulfate radicals, is generally used to start the reaction. Almost all solvents do not readily dissolve FEP, When conducting the polymerization as an emulsion in water, a surfactant like perfluorooctanesulfonic acid is frequently used. 5% of the propylene component is present in the polymer.
FEP film can be used to shield components during the curing process when producing high-quality composite parts, as in the aerospace sector. The "release film" used in these applications is designed to stop the curing adhesive polymer from adhering to the vacuum bagging materials.
FEP is a good option in the industry due to its ability to maintain chemical stability in high temperatures and resist damage by chemical fuels.
The Global Fluorinated ethylene propylene (FEP) coating Market accounted for $XX Billion in 2022 and is anticipated to reach $XX Billion by 2030, registering a CAGR of XX% from 2024 to 2030.
Industrial coatings made of Teflon launched Fluorinated ethylene propylene (FEP) coating melt and flow during baking to produce nonporous films. These industrial coatings offer outstanding nonstick qualities and a low coefficient of friction, and their maximum operating temperature is 200 °C.
They have great chemical resistance as well as having a strong dielectric. These multi-coat solutions, which are frequently utilized in nonstick applications like mold release, are available in water-based liquid and powder form.