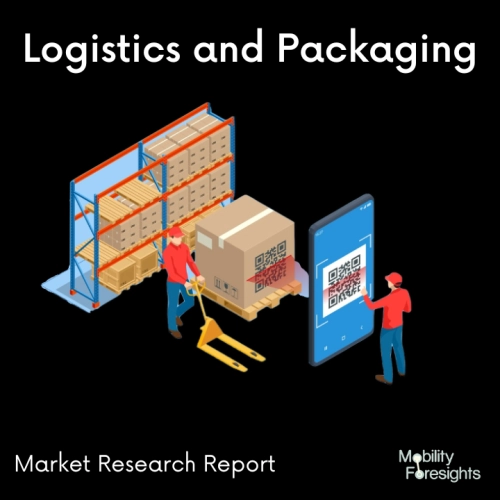
- Get in Touch with Us
Last Updated: Apr 25, 2025 | Study Period: 2024-2030
Because foam is moisture-proof, it keeps packaged things from getting wet during transit in the rain. Foam has a soft surface that is ideal for polishing things such as glass, ceramics, polished wood, and so on.
Foam is the finest material for packaging products that require a snug fit. There is little waste in the production process because most foam packing is cut to the exact specs necessary for the product. There are no off-cuts or waste, thus the amount used is greatly reduced. Unlike plastic, foam may be recycled completely after it has been opened.
The Global Foam packaging market accounted for $XX Billion in 2022 and is anticipated to reach $XX Billion by 2030, registering a CAGR of XX% from 2024 to 2030.
Tekni-Plex Introduces Foam Polypropylene Food Trays The trays, which have been under development for a year, offer a recyclable alternative to the foam polystyrene trays commonly used to pack meat and other fresh goods.
With the introduction of foam polypropylene (FPP) food trays, Wayne, PA-based Tekni-Plex Consumer Products is extending packaging alternatives for fresh meat and vegetable packers.According to the business, the first customer to use the FPP trays at retail for meat is a large wholesale organisation.
The foam PP trays are a drop-in replacement for standard foam polystyrene (FPS) trays and are designed for fresh food products such as meat, poultry, pork, fruits, and vegetables. However, unlike FPS, which has a limited or non-existent recycling infrastructure, FPP trays are easily recyclable.
All curbside/municipal recycling programmes that can currently process PP packaging will be able to process the new FPP trays. FPP will sort through current PP sorting procedures at materials recovery plants, much like conventional PP resin.
(MRFs),The FPP trays are available in a range of colors, although Tekni-Plex suggests natural resin or white to improve recyclability at MRFs. FPP has the same recycling code as non-foam PP:Because PP and PS are extremely different resins, they needed to use all of their material science skills to adapt their production method to process this material.
""They also wanted to offer an FPP processor tray that was as strong and efficient as the FPS trays, without requiring any changes to their customers' equipment." By doing so, they were able to provide a drop-in alternative solution to FPS while also aligning with the environmental aims."
Sl no | Topic |
1 | Market Segmentation |
2 | Scope of the report |
3 | Abbreviations |
4 | Research Methodology |
5 | Executive Summary |
6 | Introduction |
7 | Insights from Industry stakeholders |
8 | Cost breakdown of Product by sub-components and average profit margin |
9 | Disruptive innovation in the Industry |
10 | Technology trends in the Industry |
11 | Consumer trends in the industry |
12 | Recent Production Milestones |
13 | Component Manufacturing in US, EU and China |
14 | COVID-19 impact on overall market |
15 | COVID-19 impact on Production of components |
16 | COVID-19 impact on Point of sale |
17 | Market Segmentation, Dynamics and Forecast by Geography, 2023-2030 |
18 | Market Segmentation, Dynamics and Forecast by Product Type, 2023-2030 |
19 | Market Segmentation, Dynamics and Forecast by Application, 2023-2030 |
20 | Market Segmentation, Dynamics and Forecast by End use, 2023-2030 |
21 | Product installation rate by OEM, 2023 |
22 | Incline/Decline in Average B-2-B selling price in past 5 years |
23 | Competition from substitute products |
24 | Gross margin and average profitability of suppliers |
25 | New product development in past 12 months |
26 | M&A in past 12 months |
27 | Growth strategy of leading players |
28 | Market share of vendors, 2023 |
29 | Company Profiles |
30 | Unmet needs and opportunity for new suppliers |
31 | Conclusion |
32 | Appendix |