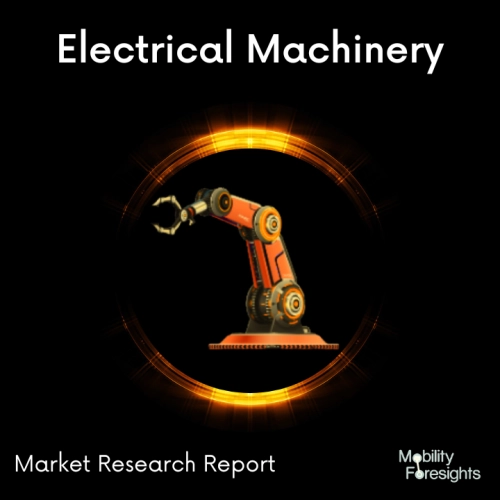
- Get in Touch with Us
Last Updated: Apr 25, 2025 | Study Period: 2023-2030
Gantry Loader (GL) automation provides high speed, high accuracy workpiece transfer and loading/unloading for unmanned operation over extended periods of time. Different specification work loader hands and work conveyors are available for a wide range of Mazak machine tools.
Conveyor can be located on machine right or left side, measurement equipment can be added and can connect two machines. By adding automatic door and robot I/F, gantry loader can be field installed onQUICK TURN's.
Different specification work loader hands and gantry loaders are available to meet a wide range of production requirements.They are Designed for large volume production for automotive components for the machining of components such as engine blocks and cylinder head.
Some of the important players in Gantry Loaders market are DMG Mori, Mazak, PROMOT Automation GmbH, Okuma, Muratec, CNC Indexing, KBH, Nakamura-Tome, ATS System, Gem, Wenger, CMZ, Dormac Production Automation, YMG Corporation Limited, Ningbo Gongtie Smart Technology Co., Ltd, Teijin Engineering Limited, Gantry Loaders Breakdown Data by Type.
The Global Gantry Loaders market accounted for $XX Billion in 2022 and is anticipated to reach $XX Billion by 2030, registering a CAGR of XX% from 2023 to 2030.
OKUMA GANTRY LOADERS - The Okuma Gantry Loader (OGL) is a built-in solution for efficient parts load/unload and minimum takt time. During workpiece load/unload, the headstock moves to that position, allowing the loader to enter the machine regardless of turret position. In addition, with servo-driven hand rotation and faster speed, a workpiece load/unload time of 4 seconds has been achieved.
The LB2000 EX II 2-axis turning center is built on Okumaâs Thermo-Friendly Concept to ensure minimal thermal growth, and slanted box bed construction translates to unsurpassed quality and rigidity. Equipped with Okumaâs high-power, high-torque PREX motor, this machine delivers high-quality machining from heavy- to high-speed cutting with a through-hole diameter able to accommodate larger workpieces.
The operator-friendly, open-architectureOSP-P300Lcontrol makes this machine not only easy to operate, but also to integrate with other peripheral equipment. A wide variety of bed lengths, bore sizes, and optionsâincluding live tooling, sub-spindle, and Y-axisâmeans there is a configuration to meet any shop's requirements.
Sl no | Topic |
1 | Market Segmentation |
2 | Scope of the report |
3 | Abbreviations |
4 | Research Methodology |
5 | Executive Summary |
6 | Introduction |
7 | Insights from Industry stakeholders |
8 | Cost breakdown of Product by sub-components and average profit margin |
9 | Disruptive innovation in the Industry |
10 | Technology trends in the Industry |
11 | Consumer trends in the industry |
12 | Recent Production Milestones |
13 | Component Manufacturing in US, EU and China |
14 | COVID-19 impact on overall market |
15 | COVID-19 impact on Production of components |
16 | COVID-19 impact on Point of sale |
17 | Market Segmentation, Dynamics and Forecast by Geography, 2023-2030 |
18 | Market Segmentation, Dynamics and Forecast by Product Type, 2023-2030 |
19 | Market Segmentation, Dynamics and Forecast by Application, 2023-2030 |
20 | Market Segmentation, Dynamics and Forecast by End use, 2023-2030 |
21 | Product installation rate by OEM, 2023 |
22 | Incline/Decline in Average B-2-B selling price in past 5 years |
23 | Competition from substitute products |
24 | Gross margin and average profitability of suppliers |
25 | New product development in past 12 months |
26 | M&A in past 12 months |
27 | Growth strategy of leading players |
28 | Market share of vendors, 2023 |
29 | Company Profiles |
30 | Unmet needs and opportunity for new suppliers |
31 | Conclusion |
32 | Appendix |