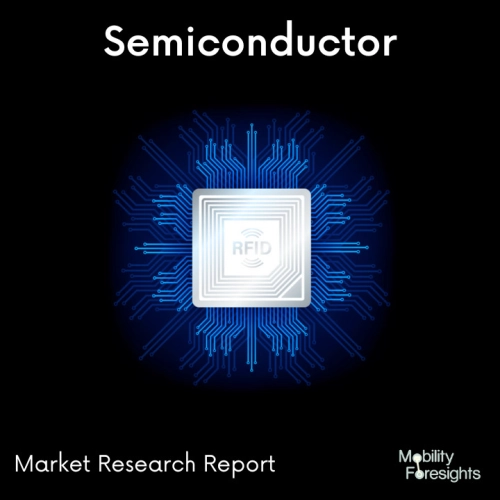
- Get in Touch with Us
Last Updated: Apr 25, 2025 | Study Period: 2024-2030
Germanium wafers are a particularly desirable semiconductor because of their distinctive qualities. Ge wafers are light and mechanically robust. Additionally, these wafers can be manufactured with a 300 mm diameter. Germanium wafers are utilised in a wide range of applications due to their exceptional crystallographic and distinctive electric characteristics.
Space solar cells, terrestrial solar cells (CPV), sensors, infrared optics, high brightness LEDs, and many more semiconductor applications are some specialised uses for germanium wafers. The most common form of electrical grade Germanium is a wafer or substrate. It is a component in the production of solar cells. It is a suitable option for producing thin films for household solar cells as well.
The Global Germanium waferMarket accountedfor $XX Billion in 2023 and is anticipated to reach $XX Billion by 2030, registering a CAGR of XX% from 2024 to 2030.
S NO | Overview of Development | Development Detailing |
1 | In partnership with esteemed business and academic partners, Umicore Electro-Optic Materials (EOM) announces the successful development of 6" Germanium wafers for vertical cavity surface emitting lasers. | A crucial part of telecom and 3D sensing systems are vertical cavity surface emitting lasers (VCSELs). Data Centers, Face Recognition systems, LiDAR Time of Flight sensors on mobile devices, and in-cabin sensing in autonomous vehicles are just a few examples of where these technologies are being used.
|
One of the factors pushing the switch from GaAs to Germanium wafers is the increase in VCSEL array sizes and costs, which will improve the working distance of these sensors. Defect-free 6" Germanium wafers outperform GaAs wafers in terms of performance and process costs for extremely demanding applications like VCSELs.
The metalloid germanium, which resembles the elements silicon and tin, is shiny, solid, and grey. It is regarded as a crucial component for technological advancements. Different electronic devices use elemental Germanium as a semiconductor.
The first semiconductor circuits were built of germanium and were used in early recordings. Today, materials like gallium arsenide and silicon are also commonly employed. Space solar cells, terrestrial solar cells, infrared optics, sensors, high-brightness LEDs, and other products can all be made using germanium wafers. It is helpful in organometallic chemistry and employed in the creation of nanowires.
It is not simple to turn an element into tiny wafers with a clean, damage-free surface that resembles a mirror. There are several steps involved. The substance becomes a germanium crystal by the Czochralski process. Through the use of cutting, grinding, and etching, the crystal is turned into a wafer. It is cleaned and inspected by the Ge wafers.
Depending on the needs of the customer, this procedure may require polishing the wafers on either one or both sides. The premium wafers are arranged in single-wafer containers and stored in a nitrogen environment.
Germanium wafers are utilised in a wide range of applications due to their exceptional crystallographic and distinctive electric characteristics. Space solar cells, terrestrial solar cells (CPV), sensors, infrared optics, high brightness LEDs, and many more semiconductor applications are some specialised uses for germanium wafers.
The Germanium system comes in three anti-reflection coating options: 3 - 5 m for mid-infrared applications, 3 - 12 m for broadband multispectral applications, and 8 - 12 m for thermal imaging applications. Ge wafer with a diameter of 55 mm and a thickness of 1 mm in the image has an AR coating on both surfaces at a thickness of 7 to 14 m, with a Tavg of greater than 95%.
An anti-reflection coating is advised for these ge windows to provide adequate transmission due to their high index of refraction. Germanium experiences thermal runaway, which causes the gearbox to drop as temperature rises. The recommended operating temperature for these germanium windows is below 100°C.
When developing for weight-sensitive systems, germanium's high density (5.33 g/cm3) should be taken into account. Due to its higher Knoop Hardness (780) than magnesium fluoride, germanium is the perfect material for infrared applications.
Certain characteristics of the Ge substrate need to be developed for the existing and next solar cell technologies produced in Europe. Additionally, this work will support UMICORE in retaining its leadership position and competitiveness in a market that is getting more and more competitive, thereby ensuring Europe's independence in this essential component for high-efficiency solar cells.
To raise the quality with a noticeable increase in yield at the solar cell producer; to make the Ge-substrates cost-effective. Improved round-edge wheel performance (less breakage), more homogenous surface grinding, greater throughput, and more cost-effective intrinsic stress alleviation all contribute to increased wafer strength.
The wafer's surface was improved by lowering the prevalence of surface flaws. Cleaning has increased by using optimised particle and metal cleaning and wafer drying based on surface tension gradient; polishing has also been improved by using better-suited chemicals and polishing pads; and cleaning has increased by using optimised particles and metal cleaning, increased solar cell production yield and better substrate quality.
Costs have implicitly decreased as the production of solar cells has increased. The production of solar cells in Europe remains independent because of this activity.
North America
The North American market, particularly the USA, will be one of the prime markets for (Germanium Wafer Market) due to the nature of industrial automation in the region, high consumer spending compared to other regions, and the growth of various industries, mainly AI, along with constant technological advancements. The GDP of the USA is one of the largest in the world, and it is home to various industries such as Pharmaceuticals, Aerospace, and Technology. The average consumer spending in the region was $72K in 2023, and this is set to increase over the forecast period. Industries are focused on industrial automation and increasing efficiency in the region. This will be facilitated by the growth in IoT and AI across the board. Due to tensions in geopolitics, much manufacturing is set to shift towards the USA and Mexico, away from China. This shift will include industries such as semiconductors and automotive.
Europe
The European market, particularly Western Europe, is another prime market for (Germanium Wafer Market) due to the strong economic conditions in the region, bolstered by robust systems that support sustained growth. This includes research and development of new technologies, constant innovation, and developments across various industries that promote regional growth. Investments are being made to develop and improve existing infrastructure, enabling various industries to thrive. In Western Europe, the margins for (Germanium Wafer Market) are higher than in other parts of the world due to regional supply and demand dynamics. Average consumer spending in the region was lower than in the USA in 2023, but it is expected to increase over the forecast period.
Eastern Europe is anticipated to experience a higher growth rate compared to Western Europe, as significant shifts in manufacturing and development are taking place in countries like Poland and Hungary. However, the Russia-Ukraine war is currently disrupting growth in this region, with the lack of an immediate resolution negatively impacting growth and creating instability in neighboring areas. Despite these challenges, technological hubs are emerging in Eastern Europe, driven by lower labor costs and a strong supply of technological capabilities compared to Western Europe.
There is a significant boom in manufacturing within Europe, especially in the semiconductor industry, which is expected to influence other industries. Major improvements in the development of sectors such as renewable energy, industrial automation, automotive manufacturing, battery manufacturing and recycling, and AI are poised to promote the growth of (Germanium Wafer Market) in the region.
Asia
Asia will continue to be the global manufacturing hub for (Germanium Wafer Market) over the forecast period with China dominating the manufacturing. However, there will be a shift in manufacturing towards other Asian countries such as India and Vietnam. The technological developments will come from China, Japan, South Korea, and India for the region. There is a trend to improve the efficiency as well as the quality of goods and services to keep up with the standards that are present internationally as well as win the fight in terms of pricing in this region. The demand in this region will also be driven by infrastructural developments that will take place over the forecast period to improve the output for various industries in different countries.
There will be higher growth in the Middle East as investments fall into place to improve their standing in various industries away from petroleum. Plans such as Saudi Arabia Vision 2030, Qatar Vision 2030, and Abu Dhabi 2030 will cause developments across multiple industries in the region. There is a focus on improving the manufacturing sector as well as the knowledge-based services to cater to the needs of the region and the rest of the world. Due to the shifting nature of fossil fuels, the region will be ready with multiple other revenue sources by the time comes, though fossil fuels are not going away any time soon.
Africa
Africa is expected to see the largest growth in (Germanium Wafer Market) over the forecast period, as the region prepares to advance across multiple fronts. This growth aligns with the surge of investments targeting key sectors such as agriculture, mining, financial services, manufacturing, logistics, automotive, and healthcare. These investments are poised to stimulate overall regional growth, creating ripple effects across other industries as consumer spending increases, access to products improves, and product offerings expand. This development is supported by both established companies and startups in the region, with assistance from various charitable organizations. Additionally, the presence of a young workforce will address various existing regional challenges. There has been an improvement in political stability, which has attracted and will continue to attract more foreign investments. Initiatives like the African Continental Free Trade Area (AfCFTA) are set to facilitate the easier movement of goods and services within the region, further enhancing the economic landscape.
RoW
Latin America and the Oceania region will showcase growth over the forecast period in (Germanium Wafer Market). In Latin America, the focus in the forecast period will be to improve their manufacturing capabilities which is supported by foreign investments in the region. This will be across industries mainly automotive and medical devices. There will also be an increase in mining activities over the forecast period in this region. The area is ripe for industrial automation to enable improvements in manufacturing across different industries and efficiency improvements. This will lead to growth of other industries in the region.
Margin Comparison (Highest to lowest) | Region | Remarks |
1 | Europe | The supply chain demands and the purchasing power in the region enable suppliers to extradite a larger margin from this region than other regions. This is for both locally manufactured as well as imported goods and services in the region. |
2 | North America | Due to the high spending power in this region, the margins are higher compared to the rest of the world, but they are lower than Europe as there is higher competition in this region. All the suppliers of goods and services target USA as a main market thereby decreasing their margins compared to Europe |
3 | Asia | Lower purchasing power, coupled with higher accessibility of services in this regions doesnât enable suppliers to charge a high margin making it lower than Europe and North America. The quality of goods and services are also affected due to this aspect in the region |
4 | Africa and ROW | The margins are the lowest in this region, except for Australia and New Zealand as the countries in this region donât have much spending power and a large portion of the products and services from this area is exported to other parts of the world |
USAâ $210 billion is allocated to federal R&D with main focus on health research, clean energy, semiconductor manufacturing, sustainable textiles, clean energy, and advanced manufacturing. Investments by private players are mainly focused on technological development including 5G infrastructure and AI in the region.
Europeâ EIC is investing â¬1 billion to innovative companies in sectors like AI, biotechnology, and semiconductors. There is also a focus on developing the ecosystem in the continent as well as improving the infrastructure for developing industries such as electric vehicles and sustainable materials. Private players are targeting data centers, AI, battery plants, and high end technological R&D investments.
Asiaâ There are investments to tackle a range of scientific and technological advancements in this region mainly coming in from China, India, South Korea, and Japan. This will include artificial intelligence, 5G, cloud computing, pharmaceutical, local manufacturing, and financial technologies. Many countries are aiming to be digital hubs including Saudi Arabia.
Africaâ Investments in the region are focused on improving the technological capabilities in the region along with socio-economic development and growth. Private participants of investments in this region is venture capital dominated who are targeting the various growth elements of the region as social stability improves. The major industries are fintech, easier lending, and manufacturing.
Latin America â The focus in the region is for fintech, e-commerce, and mobility sectors. There are also investments in improving manufacturing in the region. Local investments is focused on improving the healthcare, and transportation infrastructure in the region. The region is attracting foreign investments to improve their ability to utilize the natural resources present in the region.
Rest of the Worldâ The investments in this region are focused on clean energy, green metals, and sustainable materials. Funds in Australia are focused on solar energy and battery technologies, along with high end futuristic areas such as quantum computing. The main countries of private investment in ROW will be Australia, Canada, and New Zealand.
Sl no | Topic |
1 | Market Segmentation |
2 | Scope of the report |
3 | Abbreviations |
4 | Research Methodology |
5 | Executive Summary |
6 | Introduction |
7 | Insights from Industry stakeholders |
8 | Cost breakdown of Product by sub-components and average profit margin |
9 | Disruptive Innovation in the Industry |
10 | Technology Trends in the Industry |
11 | Consumer trends in the industry |
12 | Recent Production Milestones |
13 | Component Manufacturing in the US, EU and China |
14 | COVID-19 impact on overall market |
15 | COVID-19 impact on Production of components |
16 | COVID-19 impact on the point of sale |
17 | Market Segmentation, Dynamics and Forecast by Geography, 2024-2030 |
18 | Market Segmentation, Dynamics and Forecast by Product Type, 2024-2030 |
19 | Market Segmentation, Dynamics and Forecast by Application, 2024-2030 |
20 | Market Segmentation, Dynamics and Forecast by End Use, 2024-2030 |
21 | Product installation rate by OEM, 2023 |
22 | Incline/Decline in Average B-2-B selling price in the past 5 years |
23 | Competition from substitute products |
24 | Gross margin and average profitability of suppliers |
25 | New product development in the past 12 months |
26 | M&A in the past 12 months |
27 | Growth strategy of leading players |
28 | Market share of vendors, 2023 |
29 | Company Profiles |
30 | Unmet needs and opportunities for new suppliers |
31 | Conclusion |
32 | Appendix |