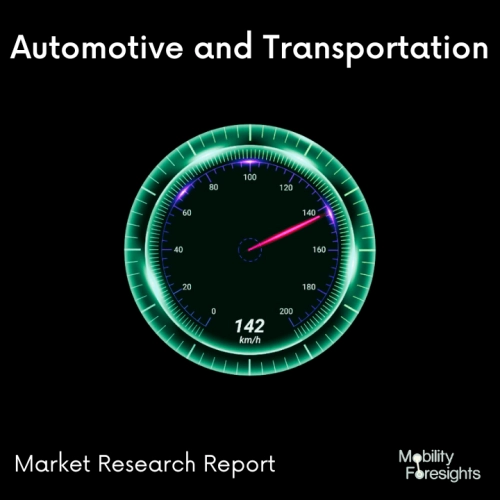
- Get in Touch with Us
Last Updated: Apr 25, 2025 | Study Period: 2024-2030
INTRODUCTION
The cores of motors, transformers, and generators in EV vehicles are made of electrical steel, sometimes referred to as silicon steel, which is an iron and silicon steel alloy.
This more malleable kind of steel has a high permeability, less core loss, and a variety of magnetic characteristics. Its low magnetic hysteresis and iron losses, or energy loss, are caused by its tiny hysteresis curve. For electrical steel, there are two types of structures: oriented and non-oriented.
The structure of grain-oriented electrical steel allows for higher flux densities and magnetic saturation since the orientation of the steel's grains is constant and stable. Grain-oriented electrical steel is most frequently used for transformers because they have predictable and precise magnetic field directions.
The Germany EV Steel Market accounted for $XX Billion in 2021 and is anticipated to reach $XX Billion by 2026, registering a CAGR of XX% from 2024 to 2030.
A battery housing constructed of steel that has been created by thyssenkrupp Steel as part of the selectrify program considerably increases fire safety in electric vehicles, is up to 50% less expensive to build, and emits only about half as much CO2 as equivalent battery housings made of aluminum.
Using ultra-high-strength steels has a lot of promise for electromobility, according to Patrick Tlauka, project manager for the selectrify program at thyssenkrupp Steel: They may satisfy a variety of criteria thanks to their concepts.
They provide designs that can withstand extremely high reaction forces and almost allow no deformation, as well as softer constructions with deliberate crumple zones that absorb impact energy.
The high-strength steel selectrify battery casing provides complete protection for the battery modules against accident influences. This safeguarding feature works to stop battery fires from starting in the first place.
Sl no | Topic |
1 | Market Segmentation |
2 | Scope of the report |
3 | Abbreviations |
4 | Research Methodology |
5 | Executive Summary |
6 | Introduction |
7 | Insights from Industry stakeholders |
8 | Cost breakdown of Product by sub-components and average profit margin |
9 | Disruptive innovation in the Industry |
10 | Technology trends in the Industry |
11 | Consumer trends in the industry |
12 | Recent Production Milestones |
13 | Component Manufacturing in US, EU and China |
14 | COVID-19 impact on overall market |
15 | COVID-19 impact on Production of components |
16 | COVID-19 impact on Point of sale |
17 | Market Segmentation, Dynamics and Forecast by Geography, 2024-2030 |
18 | Market Segmentation, Dynamics and Forecast by Product Type, 2024-2030 |
19 | Market Segmentation, Dynamics and Forecast by Application, 2024-2030 |
20 | Market Segmentation, Dynamics and Forecast by End use, 2024-2030 |
21 | Product installation rate by OEM, 2023 |
22 | Incline/Decline in Average B-2-B selling price in past 5 years |
23 | Competition from substitute products |
24 | Gross margin and average profitability of suppliers |
25 | New product development in past 12 months |
26 | M&A in past 12 months |
27 | Growth strategy of leading players |
28 | Market share of vendors, 2023 |
29 | Company Profiles |
30 | Unmet needs and opportunity for new suppliers |
31 | Conclusion |
32 | Appendix |