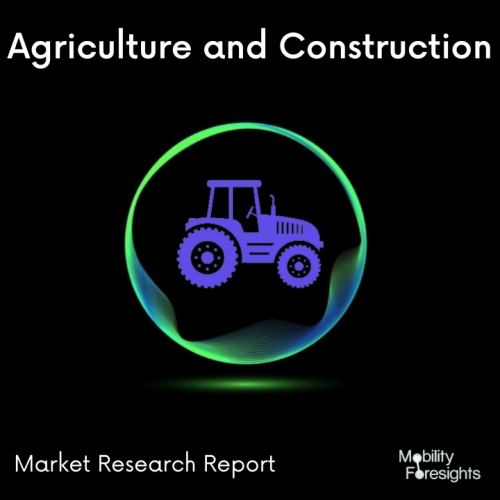
- Get in Touch with Us
Last Updated: Apr 25, 2025 | Study Period: 2024-2030
A concrete that has gone above and beyond in the mix design and placement to ensure a sustainable structure and a long life cycle with a minimal maintenance surface is referred to as "green concrete." e.g. reducing CO2 emissions, waste water, and energy.
Green concrete is characterized as having at least one component made of waste material, a production method that does not harm the environment, high performance, and life cycle sustainability.
Waste material can be used to make green concrete as a whole or partial replacement for cement and fine or coarse aggregate. Blast furnace slag, manufactured sand, glass aggregate, fly ash, recovered demolition waste aggregate, and recycled concrete aggregate are among the waste products used.
The global green concrete market accounted for $XX Billion in 2021 and is anticipated to reach $XX Billion by 2030, registering a CAGR of XX% from 2024 to 2030.
For concreting in crowded places where material storage is impractical, Precise Conchem has released Ready Mix Concrete (RMC), their most recent concreting solution.It is a kind of concrete that is manufactured and mixed according to the customer's specifications distant from the construction site and then transported utilizing a transit vehicle.
The use of Precise Ready Mix Concrete is a practical solution for lowering construction sites' workloads and streamlining onsite labor. Due to the right process control and raw materials used in its production, ready-mixed concrete also offers superior durability.
To hasten the growth of circular and sustainable building, ACC has brought the "ECOPact" global concrete project. ECOPact has been introduced in the NCR Region to enable carbon-neutral construction, following a successful market adoption on a global scale. LafargeHolcim launched the global green concrete brand ECOPact all over the world.
When compared to normal (CEM I) concrete, ECOPact emits 30% to 100% less carbon than that material.ECOPact is accessible in a range of strength classes and adheres to the requirements.
The ECOPact range will exhibit qualities that are equivalent to or superior to those of conventional concrete because of the advantageous properties of Supplementary Cementitious Materials (SCM) and the selected cement types. It can also be polished, pumped, and handled like regular concrete.
ECOPact solutions are suited for all structural components: from foundations to columns and beams, external or internal walls, driveways, walkways etc. In India, ECOPact concrete can be produced and transported anywhere within the usual delivery range of the concrete plant.
In order to offer green cement, The Hallett Group is entering Australia's cement market by constructing a cement plant in Port Augusta. The Australian federal government has supported the initiative.
Slag from the Liberty Whyaller Steelworks and the Nyrstar Port Pirie smelter will be used by the supplier of building and construction materials. At Port Adelaide, it will have a separate important and export distribution facility. Australia's CO2 emissions will be decreased by the Green Cement Transformation initiative.
At Port Augusta, a hub for processing supplemental cementitious materials (SCMs) and blending green cement will run on wind and solar power. It will create three SCM goods by either grinding them separately or mixing them with other activator products obtained from Hallett's Adelaide distribution centre.
The Elkomix-60 Quick Master Compact Concrete Batching Plant was used to commence concrete production by the German firm, which is well-known for its high-quality architectural basalt stone façade, at Mendig, a city halfway between Frankfurt and Köln.
95% of the raw materials used in the manufacturing of concrete at this concrete plant, which uses two units each of 75 tonnes and 500 tonnes of bolted type cement silos, are recycled resources. The majority of the binder used is "flue dust," and all of the aggregates utilised originate from recycling materials from demolished buildings.
Flue dust is a complex mixture of inorganic particles that have been finely divided and separated from the exhaust gases produced during the production of portland cement. Flue dust will be kept in a 500-ton cement silo and used to make green concrete.
GREEN CONCRETE MARKET GEOGRAPHY OVERVIEW
The North American market, particularly the USA, will be one of the prime markets for Green Concrete Market due to the nature of industrial automation in the region, high consumer spending compared to other regions, and the growth of various industries, mainly AI, along with constant technological advancements.
The GDP of the USA is one of the largest in the world, and it is home to various industries such as Pharmaceuticals, Aerospace, and Technology. The average consumer spending in the region was $72K in 2023, and this is set to increase over the forecast period. Industries are focused on industrial automation and increasing efficiency in the region.
This will be facilitated by the growth in IoT and AI across the board. Due to tensions in geopolitics, much manufacturing is set to shift towards the USA and Mexico, away from China. This shift will include industries such as semiconductors and automotive.
The European market, particularly Western Europe, is another prime market for Green Concrete Market due to the strong economic conditions in the region, bolstered by robust systems that support sustained growth. This includes research and development of new technologies, constant innovation, and developments across various industries that promote regional growth. Investments are being made to develop and improve existing infrastructure, enabling various industries to thrive.
In Western Europe, the margins forGreen Concrete Market are higher than in other parts of the world due to regional supply and demand dynamics. Average consumer spending in the region was lower than in the USA in 2023, but it is expected to increase over the forecast period.
Eastern Europe is anticipated to experience a higher growth rate compared to Western Europe, as significant shifts in manufacturing and development are taking place in countries like Poland and Hungary. However, the Russia-Ukraine war is currently disrupting growth in this region, with the lack of an immediate resolution negatively impacting growth and creating instability in neighboring areas. Despite these challenges, technological hubs are emerging in Eastern Europe, driven by lower labor costs and a strong supply of technological capabilities compared to Western Europe.
There is a significant boom in manufacturing within Europe, especially in the semiconductor industry, which is expected to influence other industries. Major improvements in the development of sectors such as renewable energy, industrial automation, automotive manufacturing, battery manufacturing and recycling, and AI are poised to promote the growth ofGreen Concrete Market in the region.
Asia will continue to be the global manufacturing hub for Green Concrete Market over the forecast period with China dominating the manufacturing. However, there will be a shift in manufacturing towards other Asian countries such as India and Vietnam.
The technological developments will come from China, Japan, South Korea, and India for the region. There is a trend to improve the efficiency as well as the quality of goods and services to keep up with the standards that are present internationally as well as win the fight in terms of pricing in this region.
The demand in this region will also be driven by infrastructural developments that will take place over the forecast period to improve the output for various industries in different countries. There will be higher growth in the Middle East as investments fall into place to improve their standing in various industries away from petroleum.
Plans such as Saudi Arabia Vision 2030, Qatar Vision 2030, and Abu Dhabi 2030 will cause developments across multiple industries in the region. There is a focus on improving the manufacturing sector as well as the knowledge-based services to cater to the needs of the region and the rest of the world. Due to the shifting nature of fossil fuels, the region will be ready with multiple other revenue sources by the time comes, though fossil fuels are not going away any time soon.
Africa is expected to see the largest growth inGreen Concrete Marketover the forecast period, as the region prepares to advance across multiple fronts. This growth aligns with the surge of investments targeting key sectors such as agriculture, mining, financial services, manufacturing, logistics, automotive, and healthcare.
These investments are poised to stimulate overall regional growth, creating ripple effects across other industries as consumer spending increases, access to products improves, and product offerings expand.This development is supported by both established companies and startups in the region, with assistance from various charitable organizations. Additionally, the presence of a young workforce will address various existing regional challenges.
There has been an improvement in political stability, which has attracted and will continue to attract more foreign investments. Initiatives like the African Continental Free Trade Area (AfCFTA) are set to facilitate the easier movement of goods and services within the region, further enhancing the economic landscape.
Latin America and the Oceania region will showcase growth over the forecast period inGreen Concrete Market). In Latin America, the focus in the forecast period will be to improve their manufacturing capabilities which is supported by foreign investments in the region.
This will be across industries mainly automotive and medical devices. There will also be an increase in mining activities over the forecast period in this region. The area is ripe for industrial automation to enable improvements in manufacturing across different industries and efficiency improvements. This will lead to growth of other industries in the region.
Margin Comparison (Highest to lowest) | Region | Remarks |
1 | Europe | The supply chain demands and the purchasing power in the region enable suppliers to extradite a larger margin from this region than other regions. This is for both locally manufactured as well as imported goods and services in the region. |
2 | North America | Due to the high spending power in this region, the margins are higher compared to the rest of the world, but they are lower than Europe as there is higher competition in this region. All the suppliers of goods and services target USA as a main market thereby decreasing their margins compared to Europe |
3 | Asia | Lower purchasing power, coupled with higher accessibility of services in this regions doesnât enable suppliers to charge a high margin making it lower than Europe and North America. The quality of goods and services are also affected due to this aspect in the region |
4 | Africa and ROW | The margins are the lowest in this region, except for Australia and New Zealand as the countries in this region donât have much spending power and a large portion of the products and services from this area is exported to other parts of the world |
Sl no | Topic |
1 | Market Segmentation |
2 | Scope of the report |
3 | Abbreviations |
4 | Research Methodology |
5 | Executive Summary |
6 | Introduction |
7 | Insights from Industry stakeholders |
8 | Cost breakdown of Product by sub-components and average profit margin |
9 | Disruptive innovation in the Industry |
10 | Technology trends in the Industry |
11 | Consumer trends in the industry |
12 | Recent Production Milestones |
13 | Component Manufacturing in US, EU and China |
14 | COVID-19 impact on overall market |
15 | COVID-19 impact on Production of components |
16 | COVID-19 impact on Point of sale |
17 | Market Segmentation, Dynamics and Forecast by Geography, 2022-2030 |
18 | Market Segmentation, Dynamics and Forecast by Product Type, 2022-2030 |
19 | Market Segmentation, Dynamics and Forecast by Application, 2022-2030 |
20 | Market Segmentation, Dynamics and Forecast by End use, 2022-2030 |
21 | Product installation rate by OEM, 2022 |
22 | Incline/Decline in Average B-2-B selling price in past 5 years |
23 | Competition from substitute products |
24 | Gross margin and average profitability of suppliers |
25 | New product development in past 12 months |
26 | M&A in past 12 months |
27 | Growth strategy of leading players |
28 | Market share of vendors, 2022 |
29 | Company Profiles |
30 | Unmet needs and opportunity for new suppliers |
31 | Conclusion |
32 | Appendix |