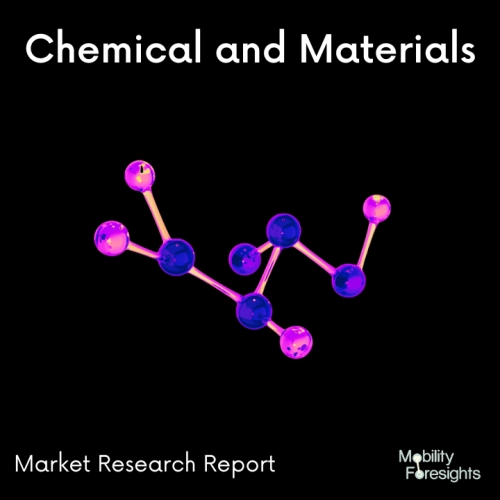
- Get in Touch with Us
Last Updated: Apr 25, 2025 | Study Period: 2024-2030
A form of alloy steel called high-strength low-alloy has higher mechanical qualities or stronger corrosion resistance than carbon steel. HSLA steels are distinct from other steels in that they are designed to meet particular mechanical qualities rather than a particular chemical makeup.
To maintain their formability and weldability, they include between 0.05 and 0.25% carbon. Manganese, up to 2.0%, and trace amounts of copper, nickel, niobium, nitrogen, vanadium, chromium, molybdenum, titanium, calcium, rare-earth elements, or zirconium are further alloying components. For reinforcement, copper, titanium, vanadium, and niobium are used.
These substances are meant to change the typical ferrite-pearlite aggregate microstructure of carbon steels, resulting in an extremely fine dispersion of alloy carbides in a nearly pure ferrite matrix.
By refining the grain size, which in the case of ferrite enhances yield strength by 50% for every doubling of the mean grain diameter, eliminates the toughness-reducing effect of a pearlitic volume percentage while maintaining and increasing the material's strength.
Another small factor is the intensification of the precipitation. The range of their yield strengths is 250 to 590 megapascals.
HSLA steels typically require 25 to 30% more power to manufacture than carbon steels due to their superior strength and toughness. To boost corrosion resistance, copper, silicon, nickel, chromium, and phosphorus are added.
Zirconium, calcium, and rare-earth elements are included to control the morphology of the sulfide inclusions, which improves formability. These are required because most HSLA steels have directionally sensitive characteristics.
Testing longitudinally and transversely to the grain can result in considerable variations in formability and impact strength. Because it suffers tensile loads, bends that are parallel to the longitudinal grain are more likely to crack near the outside border.
In HSLA steels that have undergone sulfide shape control treatment, this directional feature is significantly diminished.
They are used in vehicles such as cars, trucks, cranes, bridges, roller coasters, and other structures that need to be strong while yet being lightweight, such as cars and trucks. Structures and cross-sections made with HSLA steel are typically 20 to 30 percent lighter than carbon steel equivalents of the same strength.
The Global High-Strength Low-Alloy Steel Market accounted for $XX Billion in 2023 and is anticipated to reach $XX Billion by 2030, registering a CAGR of XX% from 2024 to 2030.
Hot Rolled High Strength Low Alloy Steel Coils were launched by Chesterfield Steel. Steels with a high degree of formability and high strength are also simple to weld.
They might be more rust- and corrosion-resistant than plain-carbon steels. HSLA steels are designed to have particular mechanical qualities rather than particular chemical makeups.
Use hot-rolled, low-alloy steel grades with high strength where it is most cost-effective, such as in automobiles, trucks, cranes, bridges, and other constructions.
HSLA steels outperform plain-carbon steels in corrosion and rust resistance.
Use HSLA steels in vehicles, heavy machinery, bridges, cranes, and other structures where their high strength-to-weight ratio is most advantageous financially. Chemistry: Mn, Si, Cr, and Mo up to a certain percentage. Cost: Moderate. Thickness:.045 to.250, Steel Grades: 35-100 Master coil: the process.
Sl no | Topic |
1 | Market Segmentation |
2 | Scope of the report |
3 | Abbreviations |
4 | Research Methodology |
5 | Executive Summary |
6 | Introduction |
7 | Insights from Industry stakeholders |
8 | Cost breakdown of Product by sub-components and average profit margin |
9 | Disruptive innovation in the Industry |
10 | Technology trends in the Industry |
11 | Consumer trends in the industry |
12 | Recent Production Milestones |
13 | Component Manufacturing in US, EU and China |
14 | COVID-19 impact on overall market |
15 | COVID-19 impact on Production of components |
16 | COVID-19 impact on Point of sale |
17 | Market Segmentation, Dynamics and Forecast by Geography, 2024-2030 |
18 | Market Segmentation, Dynamics and Forecast by Product Type, 2024-2030 |
19 | Market Segmentation, Dynamics and Forecast by Application, 2024-2030 |
20 | Market Segmentation, Dynamics and Forecast by End use, 2024-2030 |
21 | Product installation rate by OEM, 2023 |
22 | Incline/Decline in Average B-2-B selling price in past 5 years |
23 | Competition from substitute products |
24 | Gross margin and average profitability of suppliers |
25 | New product development in past 12 months |
26 | M&A in past 12 months |
27 | Growth strategy of leading players |
28 | Market share of vendors, 2023 |
29 | Company Profiles |
30 | Unmet needs and opportunity for new suppliers |
31 | Conclusion |
32 | Appendix |