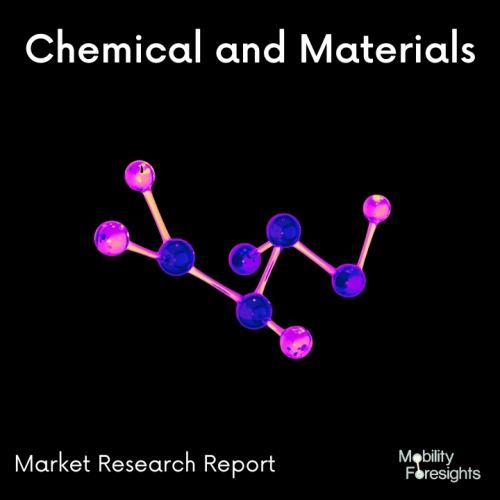
- Get in Touch with Us
Last Updated: Apr 25, 2025 | Study Period: 2024-2030
Hollow core composite insulators, which had been languishing below industry expectations, began to rise exponentially around.This was partially due to end users being more aware of the advantages of this technology, particularly safety in the case of an explosive failure.
Another important reason has been the significantly increased supplier base, which now includes significant Chinese and European industrial facilities.
Since only around half of the market for hollow insulators was accounted for by this technology five years ago, it is projected that this technology now represents more than percent of the market.
These insulators are anticipated to have the same market share as porcelain for apparatus insulators . Certain applications, such dead tank breakers and HVDC bushings, do in fact.
Being able to master the production process for hollow composite insulators is one of the most difficult tasks since the tube must function properly on both an electrical and a mechanical level.
Electrical grade glass fibres are wound onto polished steel mandrels at carefully calculated winding angles using a wet filament winding method, which entails dipping the fibres in an epoxy resin bath before using them to create FRP tubes.
A tube can be created to fulfil almost any end user requirements in terms of inner pressure as well as bending and torsional loads based on these angles and winding thickness.
The Global hollow silicone rubber insulator market accounted for $XX Billion in 2023 and is anticipated to reach $XX Billion by 2030, registering a CAGR of XX% from 2024 to 2030.
Conical composite insulators, or INMRs, have discovered a ready market among some producers of breakers' bushings.
These do offer savings in terms of a quicker mould filling process and a lesser demand for silicone housing material, even though they do not significantly reduce the amount of tube materials or winding machine time.
Smaller top flanges and a lesser necessity for internal SF6 gas, which in some countries is now charged by volume to the hollow insulator, both result in savings. Additionally, they aid in extending phase-to-phase distances, enabling greater machine compaction.
Sl no | Topic |
1 | Market Segmentation |
2 | Scope of the report |
3 | Abbreviations |
4 | Research Methodology |
5 | Executive Summary |
6 | Introduction |
7 | Insights from Industry stakeholders |
8 | Cost breakdown of Product by sub-components and average profit margin |
9 | Disruptive innovation in the Industry |
10 | Technology trends in the Industry |
11 | Consumer trends in the industry |
12 | Recent Production Milestones |
13 | Component Manufacturing in US, EU and China |
14 | COVID-19 impact on overall market |
15 | COVID-19 impact on Production of components |
16 | COVID-19 impact on Point of sale |
17 | Market Segmentation, Dynamics and Forecast by Geography, 2024-2030 |
18 | Market Segmentation, Dynamics and Forecast by Product Type, 2024-2030 |
19 | Market Segmentation, Dynamics and Forecast by Application, 2024-2030 |
20 | Market Segmentation, Dynamics and Forecast by End use, 20242030 |
21 | Product installation rate by OEM, 2023 |
22 | Incline/Decline in Average B-2-B selling price in past 5 years |
23 | Competition from substitute products |
24 | Gross margin and average profitability of suppliers |
25 | New product development in past 12 months |
26 | M&A in past 12 months |
27 | Growth strategy of leading players |
28 | Market share of vendors, 2023 |
29 | Company Profiles |
30 | Unmet needs and opportunity for new suppliers |
31 | Conclusion |
32 | Appendix |