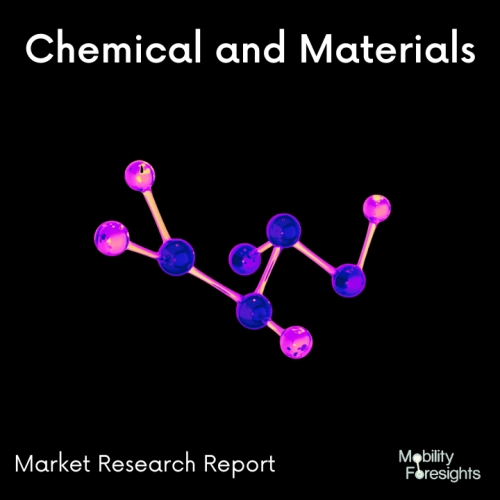
- Get in Touch with Us
Last Updated: Apr 25, 2025 | Study Period: 2024-2030
A specific kind of injection moulding machine known as a hydraulic injection moulding machine creates plastic components using hydraulic energy.
Molten plastic is injected into a mould cavity during the manufacturing process known as injection moulding. The mould is opened and the part is ejected once the plastic has cooled and solidified.
The pressure needed to inject the molten plastic into the mould cavity is produced by hydraulic injection moulding machines using a hydraulic system.
A hydraulic pump, a motor, valves, and cylinders make up the hydraulic system. The cylinders that move the mould and inject the plastic into the cavity of the mould are operated by the hydraulic pump, which produces the pressure needed to do so.
The ability of hydraulic injection moulding machines to provide high injection pressure, which is necessary for moulding large and complex parts, is one of their advantages.
Moreover, hydraulic machines provide more control over the moulding procedure, enabling accurate and reproducible part manufacturing.
Yet, there are also certain disadvantages to hydraulic injection moulding equipment. Compared to electric machines, they use more energy, are noisier, and need more maintenance.
Moreover, compared to electric machines, hydraulic machines can manufacture less parts in the same amount of time due to their shorter cycle times.
Global hydraulic injection molding machine marketaccounted for $XX Billion in 2023 and is anticipated to reach $XX Billion by 2030, registering a CAGR of XX% from 2024 to 2030.
At NPE 2018, which will be held May 7â11 at the Orange County Convention Center in Orlando, Yizumi-HPM Corp., a division of China's Yizumi Group and a leading manufacturer of high-quality hybrid injection moulding machinery from 60 to 3500-tons clamping force, will announce the launch of three new series of injection moulding machines.
The KEBA touch-screen control systems are utilised throughout the entire machine line in the DP-N series two-platen servo hydraulic, A5-N series toggle servo hydraulic, and FE-N series full servo, which are all designed to North American design criteria and standards.The series is designed and produced for the North American market, as indicated by the N designation.
The three new series from Yizumi-HPM are based on HPM designs but take advantage of Yizumi's skills in engineering, manufacturing, and finances as one of the top injection moulding machine manufacturers in the world.
The DP-N series two-platen servo hydraulic model UN1200DP-N-12050 from Yizumi-HPM has been released. This machine will utilise a unique MuCell FoamPro technology at NPE 2018, which Yizumi and Trexel Inc. of Wilmington, Massachusetts, the creators of the MuCell foaming procedure, created together.
FoamPro is a "fast heat, rapid cool" method that produces textured finishes while cutting clamping pressures by up to 50% and part weight by up to 20%.
Sl no | Topic |
1 | Market Segmentation |
2 | Scope of the report |
3 | Abbreviations |
4 | Research Methodology |
5 | Executive Summary |
6 | Introduction |
7 | Insights from Industry stakeholders |
8 | Cost breakdown of Product by sub-components and average profit margin |
9 | Disruptive innovation in the Industry |
10 | Technology trends in the Industry |
11 | Consumer trends in the industry |
12 | Recent Production Milestones |
13 | Component Manufacturing in US, EU and China |
14 | COVID-19 impact on overall market |
15 | COVID-19 impact on Production of components |
16 | COVID-19 impact on Point of sale |
17 | Market Segmentation, Dynamics and Forecast by Geography, 2024-2030 |
18 | Market Segmentation, Dynamics and Forecast by Product Type, 2024-2030 |
19 | Market Segmentation, Dynamics and Forecast by Application, 2024-2030 |
20 | Market Segmentation, Dynamics and Forecast by End use, 2024-2030 |
21 | Product installation rate by OEM, 2023 |
22 | Incline/Decline in Average B-2-B selling price in past 5 years |
23 | Competition from substitute products |
24 | Gross margin and average profitability of suppliers |
25 | New product development in past 12 months |
26 | M&A in past 12 months |
27 | Growth strategy of leading players |
28 | Market share of vendors, 2023 |
29 | Company Profiles |
30 | Unmet needs and opportunity for new suppliers |
31 | Conclusion |
32 | Appendix |