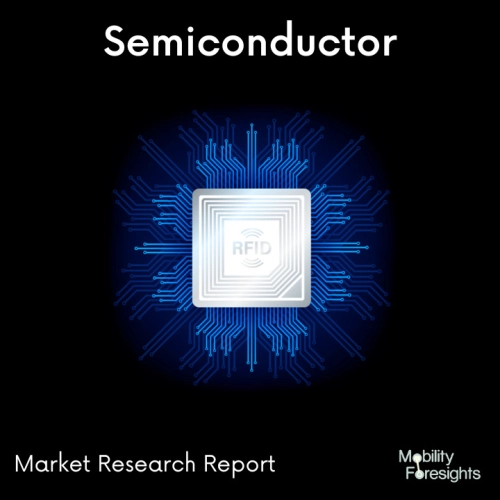
- Get in Touch with Us
Last Updated: Apr 25, 2025 | Study Period:
Each sensor has a thermocouple mold surface temperature detector, an infrared melt temperature detector, and a piezoelectric cavity pressure detector. The latter enables for the detection of both the melt temperature and the opposite mold surface temperature before the melt front arrives.
The idea behind the direct measurement approach is that a sensor is in direct touch with the melt in the cavity and monitors the pressure without any loss of pressure.
The Global In-Mold Sensors for Injection Molding market accounted for $XX Billion in 2023 and is anticipated to reach $XX Billion by 2030, registering a CAGR of XX% from 2024 to 2030.
The goal of the in-mold process is to analyze recent innovations in industry-standard sensors used to measure in-mold process parameters as well as research efforts to create original solutions for specific research and commercial issues related to injection molding process monitoring.
Sensors identify parameters of the in-mold process. There are numerous types of sensors that have different measurement objectives and sensing techniques. However, pressure and temperature sensors are the most common types of sensors used for in-mold process control.
One of the most widely used mass-production methods for the manufacture of plastics is injection molding. Injection molding accounts for around one-third of all plastics production worldwide.During injection molding, there are a number of issues with regard to measuring process parameters in the cavity.
First, melt pressure typically surpasses 150 MPa, which presents a problem. The second problem is that the detecting head is frequently exposed to a corrosive and abrasive medium at temperatures that are high and rapidly changing, often above 300 °C.
The ability to detect the actual melt pressure is hampered by the buildup of a frozen layer during the cooling phase.
Additionally, as the sensors are frequently integrated into molds, the high temperature of the mold may result in output variances as well as aberrations in the size and shape of the sensors. As a result, choosing the right sensors to use for measurements in the cavity during the process is a difficult challenge.
Sl no | Topic |
1 | Market Segmentation |
2 | Scope of the report |
3 | Abbreviations |
4 | Research Methodology |
5 | Executive Summary |
6 | Introduction |
7 | Insights from Industry stakeholders |
8 | Cost breakdown of Product by sub-components and average profit margin |
9 | Disruptive innovation in the Industry |
10 | Technology trends in the Industry |
11 | Consumer trends in the industry |
12 | Recent Production Milestones |
13 | Component Manufacturing in US, EU and China |
14 | COVID-19 impact on overall market |
15 | COVID-19 impact on Production of components |
16 | COVID-19 impact on Point of sale |
17 | Market Segmentation, Dynamics and Forecast by Geography, 2024-2030 |
18 | Market Segmentation, Dynamics and Forecast by Product Type, 2024-2030 |
19 | Market Segmentation, Dynamics and Forecast by Application, 2024-2030 |
20 | Market Segmentation, Dynamics and Forecast by End use, 2024-2030 |
21 | Product installation rate by OEM, 2023 |
22 | Incline/Decline in Average B-2-B selling price in past 5 years |
23 | Competition from substitute products |
24 | Gross margin and average profitability of suppliers |
25 | New product development in past 12 months |
26 | M&A in past 12 months |
27 | Growth strategy of leading players |
28 | Market share of vendors, 2023 |
29 | Company Profiles |
30 | Unmet needs and opportunity for new suppliers |
31 | Conclusion |
32 | Appendix |