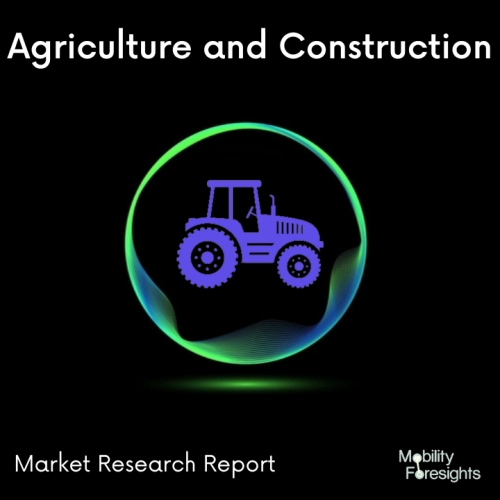
- Get in Touch with Us
Last Updated: Apr 25, 2025 | Study Period: 2024-2030
Concrete is a fundamental building material that will remain in high demand for the foreseeable future. It's difficult to envision a world without concrete and its dominating forerunner, Ordinary Portland Cement (OPC).
Although many forms of concrete have been produced for use in various purposes, they all have the following characteristics: familiarity, adaptability, strength, durability, broad availability, fire resistance, resistance to the weather, and comparably low cost. It is a global product produced in thousands of factories throughout the world.
The most energy-consuming operation is the manufacturing of cement clinker from limestone and chalk by heating limestone to temperatures exceeding 950°C. As a result of the manufacture of lime, a crucial component in cement, cement manufacturing is the third greatest source of man-made CO2 emissions.
As a result, energy savings during cement manufacture may result in a decreased environmental effect. The cement production process offers the most opportunity for enhancing energy efficiency and lowering CO2 emissions.
It is critical to remember that waste materials ignite and burn at different temperatures and under different circumstances during the cement pyro processing process.
As a result, solid waste fuels must be delivered into the kiln in a way that does not significantly alter the temperature profile or chemical processes in the overall pyroprocessing.
The four basic process pathways utilized for cement manufacture are dry, semi-dry, semi-wet, and wet processes. Dry procedures are significantly more energy efficient, although the method of choosing is mostly determined by the condition of raw materials.
The cement industry confronts a variety of issues, including dwindling fossil fuel reserves, raw material shortages, ever-increasing demand for cements and concrete, expanding environmental concerns related to climate change, and an ailing global economy.
Despite the modest gains in process efficiency achieved by the cement industry in recent years, OPC manufacturing continues to account for around 6% of all man-made worldwide carbon emissions.
To know more about Global Cement Market, read our report
SI no | Timeline | Company | Developments |
1 | November 2021 | Ambuja Cement | Ambuja Cement has partnered with Indian Institute of Technology Delhi(IITD) in order to develop next-generation low carbon cement for a greener future. |
2 | November 2021 | Betolar | Finland-based Betolar has partnered with housing company Tara in order to encourage low-carbon concrete in India. |
3 | September 2021 | Orient Cement | Orient Cement has signed a Memorandum of Understanding(MOU) with Adani Power Maharashtra for the building of a new grinding plant in Maharashtra. |
4 | September 2021 | Dalmia Cement | Dalmia Cement has added its additional capacity of 2.25 Million Tonnes at the Kapilas Cement Manufacturing Works(KSMW) near Cuttack. |
5 | August 2021 | Ambuja Cement | In order to expand the Cement Grinding unit by 1.5 MTPA in Punjab, Ambuja Cement has invested Rs 310 crores over the next two years. |
Following the pandemic-induced lockdown (June 2020 onwards), the cement industry experienced a boom as a result of the overall growth of the Indian economy, owing primarily to increased industrial activity, thriving real estate business, growing construction activity, and expanding infrastructure investment.
Historically, cement has been a severely taxed industry, with both the federal and state governments levying taxes that equal to around 30% of the selling price of cement or over 70% of the ex-factory price.
OPC is a critical building material as well as a strategic commodity. Because of our reliance on OPC, the globe today generates about 3.6 billion.
Although estimates vary by nation, over half of the world's OPC is used to produce around 11 billion metric tonnes of concrete each year; the remainder is used in mortars, screeds, stucco, coatings, soil stabilisation, and other uses.
China now dominates the OPC market, accounting for 57.3 percent of worldwide consumption. The cement industry, like the rest of the construction industry, is facing unprecedented challenges in terms of energy supply, CO2 emissions, and alternative material utilisation. As fuel sources dwindle, the global cost of energy climbs inexorably.
If carbon-reducing cements could be produced for commercial use, they would most likely provide the safest, most cost-effective, and most elegant Carbon Capture and Storage (CCS) technology.
The availability of resources determines how much cement is produced in each country. When domestic output falls short of meeting demand, a country might import to fill the gap.
By 2050, emissions will be nearly five times higher than they were in 1990. This is not a wise path to take as the world becomes more environmentally conscious.
The sustainability measures will thus not only assist pave the road for a "greener" cement industry, but will also help reduce greenhouse gas taxes and ensure the company's long-term viability.
The India Cement Market can be segmented into following categories for further analysis.
SI no | Timeline | Company | Developments |
1 | November 2021 | TANCEM | In TamilNadu, the Chief Minister has announced the launch of a new cement product âValimaiâ which denotes strength and it would control rise in price of cement. |
2 | August 2021 | Ambuja Cement | Ambuja Cement has made a difference in concrete in areas of carbon footprint reduction, protection of natural resources and also for sustainable construction. |
3 | June 2021 | Ambuja Cement | Ambuja Cement has further invested in Industry 4.0 under its âPlants of Tomorrowâ and to make cement manufacturing more efficient. |
4 | March 2021 | ACC | ACC ltd has launched the Global green concrete âECOPactâ, a low carbon range of concrete in Kolkata. |
The India cement market industry has seen significant changes as a result of technical advancement and incorporation of cutting-edge technologies in the quest of cost efficiency and consolidation.
Modernizations at the factories, as well as improvements to plant procedures, have also contributed to a reduction in staffing needs.
Ordinary Portland Cement (OPC), Portland Pozzolana Cement (PPC), Portland Blast Furnace Slag Cement (PBFS), Oil Well Cement, Rapid Hardening Portland Cement, Sulphate Resisting Portland Cement, and White Cement, among others, are produced in India.
The primary distinction is the percentage of clinkers utilised. These many types of cement are manufactured exactly according to BIS criteria, and their quality is equivalent to the best in the world.
Production industries in cement production have been and continue to be streamlined and automated, utilising the best available technology to minimise costs, emissions, and boost productivity.
This has resulted in modest reductions in GreenHouse Gas (GHG) emissions as well as lower employment levels in the industry. The creation of novel cements entails the development of cement production procedures that utilise various raw materials.
The common goal of innovative cement developers is to create cement that emits less CO2 and takes less energy to produce without lowering or compromising the cement's efficiency.
Wastes can also change the composition of cement. When tyres are co-incinerating, for example, the zinc oxide level of clinkers increases dramatically.
As a result of the combustion of alternative fuels, several components are introduced into the kiln via ash. These can have an impact on the cement's performance qualities, such as decreased early strength and longer setting periods.
Dalmia Cement (Bharat) Ltd, a subsidiary of Dalmia Bharat Ltd, has laid out a four-year investment plan to expand its present facilities and establish new manufacturing operations in Tamil Nadu.
The company plans to build two greenfield grinding machines, each with a capacity of two million tonnes per year. With the opening of the new unit, the company plans to create new employment in Virudhunagar, in addition to expanding current facilities.
UltraTech Cement, the flagship company of the Aditya Birla Group, has announced a capital of Rs. 12,886 crores to increase capacity by 22.6 mtpa through a mix of brownfield and greenfield expansion. Integrated and grinding equipment, as well as bulk terminals, would be set up to do this.
The extra capacity will be built all around the country. This investment is based on a strong belief in India's growth potential as well as a thorough understanding of the cement industry's market dynamics.
Conkrete Super King (CSK) and Halo Super King were recently launched by India Cements to capitalise on the brand identification of its successful Indian Premier League club CSK (Chennai Super Kings).
While Conkrete Super King is being marketed as a one-stop shop for all concrete needs from foundation to roof, Halo Super King will be marketed for use in precast hollow blocks, which are rapidly replacing traditional bricks in construction.
In Rajasthan, Wonder Cement, one of the country's largest cement manufacturers, introduced Wonder Cement XTREME, an environmentally friendly and high-strength cement, for all essential concrete applications. Wonder Cement presently holds a premium position in the market, thanks to its large network of dealers and retailers.
SI no | Timeline | Company | Sales |
1 | Q2-2021 | Ultratech | The total income of Ultratech at the end of March 2021 is 14,465 crores and in 2020 the total income was 11,054 crores. |
2 | Q2-2021 | JK Cement | At the end of June 2021, the total income was 166,096 lakhs and in 2020 the total income was 98,529 lakhs. |
3 | Q3-2021 | Jaypee Group | The total income at the end of September is about 113,868 lakhs and in 2020 the total income was 73584 lakhs. |
4 | Q3-2021 | Ramco Cements | At the end of third quarter the total income is 150,103 lakhs and in 2020 the income was 126,531 lakhs |
5 | Q3-2021 | NCL Industries | The total revenue at the end of March 2021 is 40,519 lakhs and in 2020 the revenue was 24,686 lakhs. |
The India cement market sector has already reduced overall CO2 emissions to an industrial average of 0.72 t CO2/t cement, down from a far higher level of 1.12 t CO2/t cement in 1996.
CO2 emissions are expected to be lowered further to 0.58 t CO2/t cement by 2050. Simultaneously, R&D activities are aimed at developing and implementing techniques for designing buildings and concrete structures for a specific service life, the use of C&D waste in construction, and the substitution of natural sand with bottom ash.
Supplementary cementitious materials (SCMs) can be employed as fillers or for their pozzolanic qualities, and Ultratech cement has lately begun to focus on them.
Blast furnace slag, fly ash, and, to a lesser extent, silica fume are the most common industrial SCMs. The goal was to reduce direct resource utilisation and improve waste generation reuse implementation within the industrial sector.
This resulted in the development of new cement formulations with substantially greater strengths and requirements.
Ambuja Cements has also been involved in the provision of unique cement technology for the purpose of high strength railway sleepers under the Ambuja Railcam product brand, which is a high Blaine Portland cement.
In addition, it has introduced the low carbon footprint based high strength cement of Compchem, which has the least impact on the environment in the country.
Shree Cement is renowned for its effective and cutting-edge manufacturing techniques. The business offers a wide range of products to meet different construction needs. It manufactures a variety of cements, such as Sulphate Resistant Cement (SRC), Portland Pozzolana Cement (PPC), and Ordinary Portland Cement (OPC). Modern facilities are used in their production, and strict quality control procedures are followed to guarantee uniformity and longevity.
The focus on sustainability that Shree Cement places as one of its distinguishing characteristics. Throughout its activities, the firm has incorporated a number of environmentally friendly projects.
It concentrates on lowering its carbon footprint, increasing energy efficiency, and reducing waste production. To meet its sustainability objectives, Shree Cement has implemented cutting-edge technology like waste heat recovery systems, alternative fuel usage, and renewable energy sources.
As a result of its dedication to sustainable methods, it has won numerous awards and certifications.The manufacturing facilities of Shree Cement are positioned carefully to facilitate effective distribution and prompt product delivery.
The business has a robust distribution network that includes many different channels, such as dealers, merchants, and direct sales to significant construction projects. Shree Cement is able to meet the various needs of consumers all over India thanks to its broad reach.
Shree Cement prioritizes research & development in addition to its manufacturing skills to promote innovation and product enhancement. To create innovative cement formulations and improve product performance, the company makes investments in research facilities and collaborates with recognized institutions.
Because of its dedication to innovation, Shree Cement has been able to market specialty products designed for certain uses, such as high-strength cement for infrastructure projects and environmentally friendly cement for green buildings.
The success of Shree Cement can be attributed to its capable personnel, solid management, and customer-focused philosophy. The organization places a high value on employee welfare and development, ensuring a skilled and motivated staff. Additionally, it keeps a close contact with its clients by offering technical support, effective logistics, and top-notch after-sales care.
A specialist cement product recognized for its quick-setting qualities is Birla Chetak Cement, produced by Birla Corporation Limited. It is a well-known brand in the Indian cement industry, providing premium cement options for a variety of construction projects. Due to its dependability and effectiveness, Birla Chetak Cement has become well-liked among contractors, engineers, and builders.
The capacity of Birla Chetak Cement to reach a high starting strength in a short amount of time is one of its main advantages. With the help of this innovation, formwork may be removed more quickly, speeding up construction projects.
Early strength development reduces construction downtime and speeds up project timeframes, which increases production and efficiency. Excellent workability and simple handling characteristics of Birla Chetak Cement enable effective mixing and application.
It sticks nicely to various building materials, ensuring a solid and long-lasting bond. High-quality raw ingredients are used in the cement's formulation, and cutting-edge manufacturing processes guarantee dependable performance.
Birla Chetak Cement not only has quick-setting capabilities but also has excellent compressive strength, low permeability, and resilience to environmental conditions. These characteristics help the constructions made using Birla Chetak Cement to be stable and long-lasting.
Sl no | Topic |
1 | Market Segmentation |
2 | Scope of the report |
3 | Abbreviations |
4 | Research Methodology |
5 | Executive Summary |
6 | Introduction |
7 | Insights from Industry stakeholders |
8 | Cost breakdown of Product by sub-components and average profit margin |
9 | Disruptive innovation in the Industry |
10 | Technology trends in the Industry |
11 | Consumer trends in the industry |
12 | Recent Production Milestones |
13 | Component Manufacturing in US, EU and China |
14 | COVID-19 impact on overall market |
15 | COVID-19 impact on Production of components |
16 | COVID-19 impact on Point of sale |
17 | Market Segmentation, Dynamics and Forecast by Geography, 2024-2030 |
18 | Market Segmentation, Dynamics and Forecast by Product Type, 2024-2030 |
19 | Market Segmentation, Dynamics and Forecast by Application, 2024-2030 |
20 | Market Segmentation, Dynamics and Forecast by End use, 2024-2030 |
21 | Product installation rate by OEM, 2023 |
22 | Incline/Decline in Average B-2-B selling price in past 5 years |
23 | Competition from substitute products |
24 | Gross margin and average profitability of suppliers |
25 | New product development in past 12 months |
26 | M&A in past 12 months |
27 | Growth strategy of leading players |
28 | Market share of vendors, 2023 |
29 | Company Profiles |
30 | Unmet needs and opportunity for new suppliers |
31 | Conclusion |
32 | Appendix |