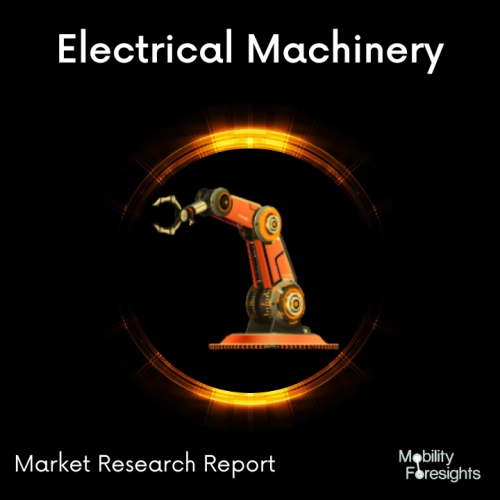
- Get in Touch with Us
Last Updated: Apr 25, 2025 | Study Period: 2024-2030
Using a ram or screw-type plunger, liquid plastic or rubber material is forced into a mould cavity where it solidifies into a shape that follows the contour of the mould.
This process is known as injection moulding. The injection unit's duties include using heat to melt plastic and injecting the molten material into a mould.
To melt plastic introduced from the hopper and to collect molten plastic in front of the screw (a process known as metering), the screw is turned.
A manufacturing technique that enables mass production of parts is injection moulding. Molten materials are injected into a mould to make it work. Usually, it is employed as a mass production technique to create thousands of similar goods.
The India plastic injection molding machine market accounted for $XX Billion in 2023 and is anticipated to reach $XX Billion by 2030, registering a CAGR of XX% from 2024 to 2030.
WINELECToday, all electric machines are well accepted for general moulding, automotive, and thin wall packaging segments as well due to the excellent benefits provided in terms of better moulding consistency, reduced rejections, high productivity, low energy consumption, and environment friendly approach.
Windsor has introduced an all-electric injection moulding machine from the "WINELEC" series that can produce 400ml thin wall containers with a 4 cavity capacity in under 5.0 seconds.
With many value-added features, including clamp movement on frictionless linear guides, nozzle contact force arrangement driven by servo motor, air cooled servo motors, and most recent generation control system, etc The WINELEC series of all-electric machines are entirely designed and produced in India.
in addition to the benefits of using an electric machine, such as complete control over all movements, improved precision, high dynamics, and increased productivity at a lower cost of manufacturing (saving between 50% and 80% of energy) The clamp force range for WINELEC series machines will be 50 to 350 tonnes, and a variety of injection units can be used depending on the application's needs.
To display the first "Totally Integrated PET Preform system" developed in India, the 32L WINPET machine was introduced.
The obvious goal was to make customers' lives easier by offering turnkey projects and with single point process setting of moulding machine, mould, and auxiliaries in PET Preform production, which is always a very crucial and time-consuming job.
Sl no | Topic |
1 | Market Segmentation |
2 | Scope of the report |
3 | Abbreviations |
4 | Research Methodology |
5 | Executive Summary |
6 | Introduction |
7 | Insights from Industry stakeholders |
8 | Cost breakdown of Product by sub-components and average profit margin |
9 | Disruptive innovation in the Industry |
10 | Technology trends in the Industry |
11 | Consumer trends in the industry |
12 | Recent Production Milestones |
13 | Component Manufacturing in US, EU and China |
14 | COVID-19 impact on overall market |
15 | COVID-19 impact on Production of components |
16 | COVID-19 impact on Point of sale |
17 | Market Segmentation, Dynamics and Forecast by Geography, 2024-2030 |
18 | Market Segmentation, Dynamics and Forecast by Product Type, 2024-2030 |
19 | Market Segmentation, Dynamics and Forecast by Application, 2024-2030 |
20 | Market Segmentation, Dynamics and Forecast by End use, 2024-2030 |
21 | Product installation rate by OEM, 2023 |
22 | Incline/Decline in Average B-2-B selling price in past 5 years |
23 | Competition from substitute products |
24 | Gross margin and average profitability of suppliers |
25 | New product development in past 12 months |
26 | M&A in past 12 months |
27 | Growth strategy of leading players |
28 | Market share of vendors, 2023 |
29 | Company Profiles |
30 | Unmet needs and opportunity for new suppliers |
31 | Conclusion |
32 | Appendix |