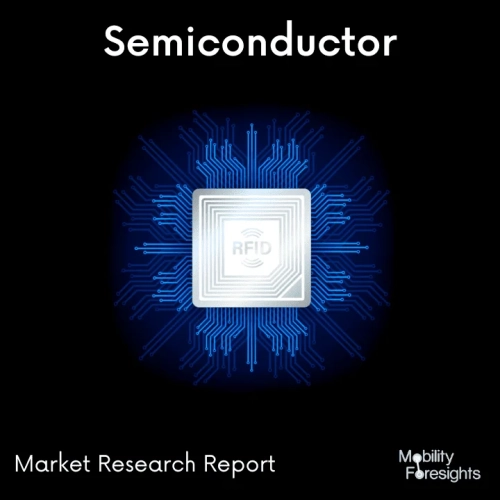
- Get in Touch with Us
Last Updated: Apr 25, 2025 | Study Period:
A semiconductors binding equipment is a piece of semiconductor device manufacturing equipment. It can be used to bind two materials collectively, usually through the application of heat and/or compression. Metals, polymers, and other non-metallic substances can be bonded together.
Wire bonders and die bonders are the two types of semiconductors binding machines available. Wire bonders have been used to attach semiconductor chip connections to their packages or printed circuit boards (PCB).
In Connected systems, semiconductors bonding techniques are utilised to join multi-stacked dies onto interfaces while using as little space as feasible. The semiconductors bonding industry is being propelled ahead by the increased use of stacked die technologies in IoT devices.
The practise of layering on bare die upon top of someone else within such a semiconductor-based packaging is known as stacked die, and it is utilised to utilise the same geographical region on a membranes for various functionalities.
Because shorter interconnection routing among integrated devices increases analogue signals, die layering enhances electrolytic device properties. Device makers (OEMs) in the semiconductor sector are focusing on expanding the notion of IoT beyond connectivity.
Sensors, RFID tags, smart metres, smart street signs, and distribution control mechanisms are just a few of the IoT apps and platforms that are increasingly being used in applications like construction and telemonitoring, industrial materials, combined feature, intellectual clothing stores, transportation infrastructure, and more.
In the next years, APAC is projected to continue to dominate the semiconductors bonding industry. The presence of a high number of manufacturing facilities, IDM, especially OSAT enterprises in APAC contributes to the region's dominant position.
APAC is home to the majority of the country's top IDMs and foundries. In the semiconductor manufacturing procedure, these firms use die bonding technology. Furthermore, the region's growing number of IDMs is likely to enhance market growth in the near future.
HybondInc. is a leading mobiliser of the equipment in the market. The latest integration has been the When retaining dies on semiconductors, the EDB-141 can indeed be equipped with a waffles pack/jel packing, loose dies platform, or die ejector.
For incredibly low quantity epoxy pouring, the dispense equipment can be equipped with HYBOND's micro-dispense nozzle. This die strengthened is tough enough for continuous operation, yet small development runs, and laboratory application are perfect.
Panasonic is part of the component manufacturers trending companies in the current industry. The Die bonding occurs quickly after Epoxy injection, allowing the bonded procedure to be completed even before Epoxy deteriorates through duration.
This ensures that all bond locations on a substrates are secure and of good quality. The Bonded Stage Lens also allows for pre-bonding examination following Epoxy dispensing and post-bonding inspection following die bonding (OP). This solution enables you to carry out manufacture while monitoring quality in real time.
Sl no | Topic |
1 | Market Segmentation |
2 | Scope of the report |
3 | Abbreviations |
4 | Research Methodology |
5 | Executive Summary |
6 | Introduction |
7 | Insights from Industry stakeholders |
8 | Cost breakdown of Product by sub-components and average profit margin |
9 | Disruptive innovation in theIndustry |
10 | Technology trends in the Industry |
11 | Consumer trends in the industry |
12 | Recent Production Milestones |
13 | Component Manufacturing in US, EU and China |
14 | COVID-19 impact on overall market |
15 | COVID-19 impact on Production of components |
16 | COVID-19 impact on Point of sale |
17 | Market Segmentation, Dynamics and Forecast by Geography, 2024-2030 |
18 | Market Segmentation, Dynamics and Forecast by Product Type, 2024-2030 |
19 | Market Segmentation, Dynamics and Forecast by Application, 2024-2030 |
20 | Market Segmentation, Dynamics and Forecast by End use, 2024-2030 |
21 | Product installation rate by OEM, 2023 |
22 | Incline/Decline in Average B-2-B selling price in past 5 years |
23 | Competition from substitute products |
24 | Gross margin and average profitability of suppliers |
25 | New product development in past 12 months |
26 | M&A in past 12 months |
27 | Growth strategy of leading players |
28 | Market share of vendors, 2023 |
29 | Company Profiles |
30 | Unmet needs and opportunity for new suppliers |
31 | Conclusion |
32 | Appendix |