INDUSTRIAL VACUUM PUMPS MARKET
KEY FINDINGS
- The Industrial Vacuum Pumps Market from 2024 to 2030 exhibits promising growth prospects driven by expanding applications in various industries such as semiconductor, chemical, and pharmaceutical.
- Increasing demand for vacuum pumps in manufacturing processes for removing gases and creating vacuum environments propels market expansion during the forecast period.
- Technological advancements like the development of energy-efficient and low-maintenance vacuum pumps are anticipated to enhance market penetration and drive adoption across industries.
- The emergence of Industry 4.0 and automation trends further accelerates the adoption of vacuum pump solutions, fostering market growth.
- Asia Pacific is projected to witness substantial growth attributed to rapid industrialization, particularly in countries like China and India, coupled with investments in manufacturing infrastructure.
- Stringent environmental regulations focusing on energy efficiency and emission reduction propel the demand for eco-friendly vacuum pump solutions, shaping market dynamics.
- Rising awareness regarding the benefits of vacuum technology in preserving product quality and optimizing manufacturing processes drives market demand among end-users.
- Collaborations and partnerships among key players for product development and geographic expansion are anticipated to intensify competition in the industrial vacuum pumps market.
- The adoption of vacuum pump systems in emerging sectors such as renewable energy, aerospace, and medical devices presents lucrative opportunities for market players during the forecast period.
- Despite the favorable growth outlook, challenges related to high initial investments and maintenance costs may hinder market growth, necessitating strategic initiatives to address cost concerns and sustain competitiveness.
INDUSTRIAL VACUUM PUMPS MARKET OVERVIEW
- The industrial vacuum pumps market is poised for significant growth over the next six years, with analysts predicting a Compound Annual Growth Rate (CAGR) of around 6.7% by 2030. This translates to a market size exceeding $8.75 billion by the end of the decade.
- This growth is attributed to several key factors. One major driver is the ever-increasing demand for advanced technology across various industries. From semiconductors and electronics to pharmaceuticals and general manufacturing, intricate processes rely on efficient vacuum generation.
- Heightened automation is another key contributor. As industries automate more processes, the need for reliable and efficient vacuum pumps becomes ever more critical. These pumps play a crucial role in tasks like material handling, degassing, and leak detection in automated systems.
- The growing focus on energy efficiency and sustainability is also influencing the market. Manufacturers are developing pumps that consume less energy and produce fewer emissions, catering to the rising environmental concerns of businesses.
- Technological advancements are another area propelling the market forward. New pump designs are emerging that offer improved performance, higher pumping speeds, and better durability. These advancements translate to increased productivity and reduced downtime for businesses.
- The industrial vacuum pumps market is not without its challenges. One key concern is the initial investment cost associated with these pumps. However, the long-term benefits in terms of efficiency, productivity, and energy savings are likely to outweigh the initial expense.
- Another challenge is the stringent regulations governing the use of certain lubricants in vacuum pumps. This is leading to the development of dry pumps that eliminate the need for lubricants altogether.
- The Asia Pacific region is expected to be a major growth engine for the industrial vacuum pumps market. The booming manufacturing sector in countries like China and India is a key driver in this region.
- North America and Europe are also expected to witness steady growth, driven by the continued demand for advanced technologies and a focus on process optimization in these regions.
- Overall, the industrial vacuum pumps market presents a promising outlook for the coming years. With growing demand across industries, technological advancements, and a focus on sustainability, this market is set for continued expansion and innovation.
INTRODUCTION TO INDUSTRIAL VACUUM PUMPS MARKET
Industrial vacuum pumps are mechanical devices used to create a vacuum or low-pressure environment within industrial settings by removing air or gases from a sealed chamber or system. These pumps play a crucial role in various industries such as manufacturing, pharmaceuticals, food processing, and semiconductor manufacturing, where the creation of vacuum environments is essential for processes like filtration, packaging, and material handling.
There are several types of industrial vacuum pumps, including rotary vane pumps, liquid ring pumps, dry vacuum pumps, and scroll pumps. Each type has its unique mechanism of operation and is suitable for different applications based on factors like required vacuum level, pumping speed, and compatibility with the handled materials.
The benefits of industrial vacuum pumps include improved efficiency in manufacturing processes, enhanced product quality, reduced contamination risks, and increased productivity. These pumps also enable precise control over vacuum levels, which is critical for maintaining the integrity of sensitive materials and processes.
However, along with these benefits, there are risks and challenges associated with industrial vacuum pump systems, including potential leaks leading to contamination, high initial investment costs, energy consumption concerns, and the need for regular maintenance to ensure optimal performance and longevity. Additionally, improper selection or operation of vacuum pump systems can result in process inefficiencies or product quality issues, highlighting the importance of careful planning and maintenance in industrial applications.
INDUSTRIAL VACUUM PUMPS MARKET SIZE AND FORECAST
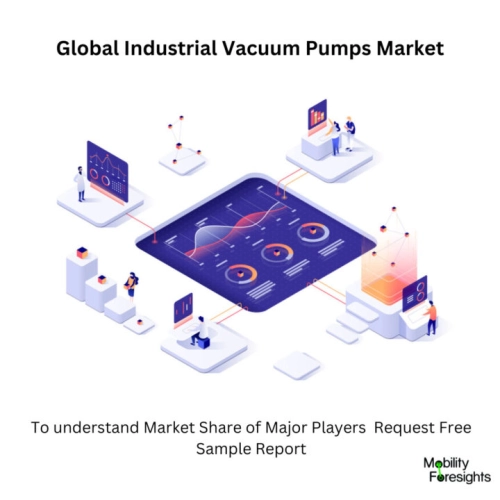
The Global Industrial vacuum pumps market accounted for $XX Billion in 2023 and is anticipated to reach $XX Billion by 2030, registering a CAGR of XX% from 2024 to 2030.
INDUSTRIAL VACUUM PUMPS MARKET TRENDS
- Adoption of smart and IoT-enabled vacuum pump systems for remote monitoring and predictive maintenance, enhancing operational efficiency and reducing downtime.
- Increasing focus on sustainability drives the development of energy-efficient and eco-friendly vacuum pump technologies to meet stringent regulatory requirements.
- Integration of advanced materials and coatings to improve pump performance, durability, and resistance to corrosive substances, expanding application possibilities.
- Growing demand for customized vacuum pump solutions tailored to specific industry requirements, spurring innovation and product differentiation among manufacturers.
- Expansion of vacuum pump applications beyond traditional industries into emerging sectors such as 3D printing, nanotechnology, and electric vehicle manufacturing.
INDUSTRIAL VACUUM PUMPS MARKET NEW PRODUCT DEVELOPMENT
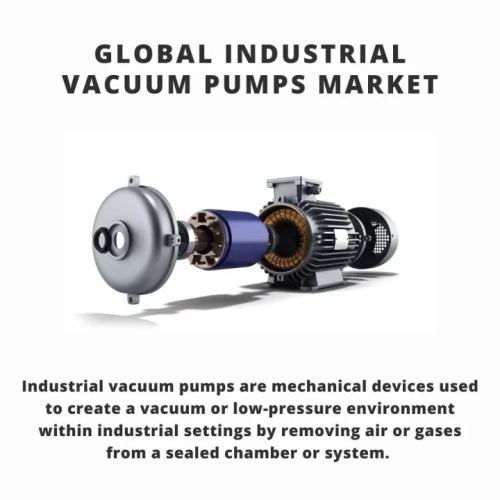
- Edwards Vacuum:Known for their emphasis on innovation, they're likely developing pumps focused on energy efficiency.
- Agilent Technologies:Their focus on R&D suggests they might have cutting-edge pump technologies in the pipeline.
- Pfeiffer Vacuum:Being at the forefront of development suggests new pumps with superior performance and reliability.
- Leybold GmbH:Their development of dry pumps indicates new offerings catering to sustainability.
INDUSTRIAL VACUUM PUMPS MARKET SEGMENTATION
Industrial Vacuum Pumps Market By Geography
- USA
- Europe
- China
- Asia Excluding China
- ROW
Industrial Vacuum Pumps Market By Pump Type
- Rotary Vane Pumps
- Piston Pumps
- Screw Pumps
- Claw Pumps
- Diffusion Pumps
- Cryogenic Pumps
- Turbomolecular Pumps
Industrial Vacuum Pumps Market By Application
- Semiconductors & Electronics
- Pharmaceuticals & Biotechnology
- Food & Beverage Processing
- Chemical Processing
- Power Generation
- Solar Photovoltaics
Industrial Vacuum Pumps Market By Capacity
- Low Vacuum (up to 100 mbar)
- Medium Vacuum (100 mbar to 1 mbar)
- High Vacuum (1 mbar to 10^-3 mbar)
- Ultra-High Vacuum (below 10^-3 mbar)
INDUSTRIAL VACUUM PUMPS MARKET COMPANY PROFILES
INDUSTRIAL VACUUM PUMPS MARKET REPORT WILL ANSWER FOLLOWING QUESTIONS
- What are the projected growth rates for the industrial vacuum pumps market from 2024 to 2030?
- What are the key drivers driving the growth of the industrial vacuum pumps market during the forecast period?
- Which regions are expected to witness the highest growth in the industrial vacuum pumps market?
- What are the major applications of industrial vacuum pumps across different industries?
- How do advancements in vacuum pump technology impact market dynamics?
- What role does sustainability play in shaping the industrial vacuum pumps market?
- How do regulatory policies influence the adoption of vacuum pump solutions?
- What are the emerging trends in vacuum pump rental and leasing services?
- How are key players strategizing to maintain their market position amidst competition?
- What are the challenges faced by manufacturers in the industrial vacuum pumps market?
- How does the adoption of IoT and smart technologies impact vacuum pump operations?
- What are the implications of Industry 4.0 on vacuum pump manufacturing and usage?
- What are the environmental implications of vacuum pump operations and how are they being addressed?
- How are manufacturers innovating to improve the energy efficiency of vacuum pump systems?
- What are the emerging applications of vacuum pumps in niche industries?
- What are the opportunities for collaboration and partnerships in the vacuum pump market ecosystem?
- How do advancements in materials and coatings enhance vacuum pump performance?
- What are the key considerations for end-users when selecting vacuum pump solutions?
- How are emerging economies contributing to market growth in the industrial vacuum pumps sector?
- What are the technological advancements driving the evolution of vacuum pump systems?
- How does the shift towards decentralized vacuum systems impact market dynamics?
- What are the implications of the COVID-19 pandemic on the industrial vacuum pumps market?
- How do fluctuations in raw material prices affect the profitability of vacuum pump manufacturers?
- What are the potential risks associated with the adoption of vacuum pump technology?
- How do changing consumer preferences influence product development in the vacuum pump industry?
- What are the opportunities for market expansion in untapped regions or industries?
- How do trade policies and geopolitical factors affect the global vacuum pump market?
- What are the implications of digitalization on vacuum pump maintenance and servicing?
- How are manufacturers addressing concerns related to noise pollution and vibration in vacuum pump operations?
- What are the prospects for growth in the aftermarket segment of the industrial vacuum pumps market?