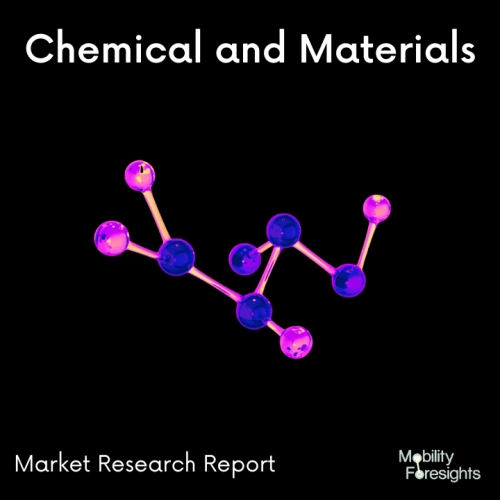
- Get in Touch with Us
Last Updated: Apr 25, 2025 | Study Period: 2024-2030
The process of moulding or shaping plastic pieces or inserts around other, non-plastic parts is known as insert injection moulding.
Most often, the inserted component is a straightforward item like a thread or rod, but in rare circumstances, inserts can be more complicated like a battery or motor.
The major distinction between insert moulding and outsert moulding is that with outsert moulding, the volume and/or surface area of the insert is greater than that of the plastic. In outsert moulding, the plastic is injected into the part rather than around it.
The Global Insert Injection Molding Market accounted for $XX Billion in 2023 and is anticipated to reach $XX Billion by 2030, registering a CAGR of XX% from 2024 to 2030.
Overmolding and insert moulding are both injection moulding techniques, although insert moulding differs in a few significant aspects. Insert moulding is the process of loading a preformed component (typically metal) into a mould before the plastic material is injected.
This is in contrast to overmolding, which involves injecting a second resin onto a firmer plastic substrate. This enables product teams to mould ergonomic devices, power tool grips, and rubber gaskets directly onto pre-existing parts without adding additional manual labour.
With the aid of the injection moulding technology, designers and engineers can quickly incorporate threaded metal inserts into plastic components, encase metal electrical components inside shielding plastic housings, or produce everyday hand tools like scissors and screwdrivers.
In comparison to alternative techniques for encasing metal components into plastic products, insert injection moulding is a procedure that is easier to manage and can produce superior results.
Manufacturers in the consumer goods, beauty, and other sectors, as well as those in the medical, electrical, and automotive sectors, are increasingly utilising insert moulding technology.
However, product teams should take a few design and manufacturing process issues into mind in order to optimise the advantages of insert moulding.
In the end, insert moulding simplifies the process of joining pieces to make sturdy parts without the need for assembly or any extra stages that could raise manufacturing costs.
Although insert moulding and overmolding are comparable in many aspects, the latter is more versatile in terms of material choices and end-use applications.
In fact, insert moulding is frequently employed to build the housings for life-saving medical equipment like pacemakers and other implants.
Sl no | Topic |
1 | Market Segmentation |
2 | Scope of the report |
3 | Abbreviations |
4 | Research Methodology |
5 | Executive Summary |
6 | Introduction |
7 | Insights from Industry stakeholders |
8 | Cost breakdown of Product by sub-components and average profit margin |
9 | Disruptive innovation in the Industry |
10 | Technology trends in the Industry |
11 | Consumer trends in the industry |
12 | Recent Production Milestones |
13 | Component Manufacturing in US, EU and China |
14 | COVID-19 impact on overall market |
15 | COVID-19 impact on Production of components |
16 | COVID-19 impact on Point of sale |
17 | Market Segmentation, Dynamics and Forecast by Geography, 2024-2030 |
18 | Market Segmentation, Dynamics and Forecast by Product Type, 2024-2030 |
19 | Market Segmentation, Dynamics and Forecast by Application, 2024-2030 |
20 | Market Segmentation, Dynamics and Forecast by End use, 2024-2030 |
21 | Product installation rate by OEM, 2023 |
22 | Incline/Decline in Average B-2-B selling price in past 5 years |
23 | Competition from substitute products |
24 | Gross margin and average profitability of suppliers |
25 | New product development in past 12 months |
26 | M&A in past 12 months |
27 | Growth strategy of leading players |
28 | Market share of vendors, 2023 |
29 | Company Profiles |
30 | Unmet needs and opportunity for new suppliers |
31 | Conclusion |
32 | Appendix |