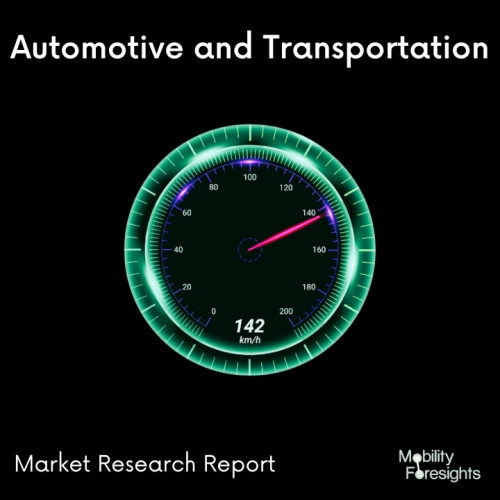
- Get in Touch with Us
Last Updated: Apr 25, 2025 | Study Period: 2024-2030
While metal remains the preferred material when it comes to producing various auto parts, the subsequent rise in weight of vehicles has prompted automakers to search for alternatives in order to optimize overall vehicle efficiency. Thus, plastics are the second most frequent material used nowadays to construct various automobile parts after metal.
Due to the presence of a bigger battery pack, a smaller internal combustion engine, and the need for lightweight materials to increase fuel economy, electric cars consume more plastic than traditional automobiles.
The raw materials used most frequently to create the components and accessories that make up an electric car are known as electric vehicle plastics.
Some of the major drivers driving the growth of the electric vehicle plastics market in the upcoming years are the increase in electric vehicle sales and manufacturing, as well as government limits on car emissions.
The Italy EV Plastics Market accounted for $XX Billion in 2023 and is anticipated to reach $XX Billion by 2030, registering a CAGR of XX% from 2024 to 2030.
Plastics used in charging infrastructure are in high demand as sales of electric vehicles soar. According to LANXESS, there are several applications for its Durethan polyamides and Pocan polyesters in this field.
A new design idea for charging inlets from LANXESS demonstrates the potential benefits of these thermoplastic compounds. The charging coupler of the external charging station is accommodated by these, which are fitted in battery electric cars.
The design is the result of conversations LANXESS has had with charging system manufacturers, and it includes the knowledge the company has previously gained from working on several projects to construct charging infrastructure.
The front and rear housings, a socket for the connector from the charging station, and an actuator are the main components of this charging inlet design. The latter secures the connector so that it cannot be unintentionally or purposefully taken out while charging.
Another crucial components are the pin holder. It secures a printed circuit board (PCB) with cables for charging with direct or alternating current, among other things, as well as the metallic connector pins.
A lot of thought went into the pin holder's design. It arranges the cables such that the heat generated during charging is diffused through them as well as through the other wires that aren't in use.
Sl no | Topic |
1 | Market Segmentation |
2 | Scope of the report |
3 | Abbreviations |
4 | Research Methodology |
5 | Executive Summary |
6 | Introduction |
7 | Insights from Industry stakeholders |
8 | Cost breakdown of Product by sub-components and average profit margin |
9 | Disruptive innovation in the Industry |
10 | Technology trends in the Industry |
11 | Consumer trends in the industry |
12 | Recent Production Milestones |
13 | Component Manufacturing in US, EU and China |
14 | COVID-19 impact on overall market |
15 | COVID-19 impact on Production of components |
16 | COVID-19 impact on Point of sale |
17 | Market Segmentation, Dynamics and Forecast by Geography, 2024-2030 |
18 | Market Segmentation, Dynamics and Forecast by Product Type, 2024-2030 |
19 | Market Segmentation, Dynamics and Forecast by Application, 2024-2030 |
20 | Market Segmentation, Dynamics and Forecast by End use, 2024-2030 |
21 | Product installation rate by OEM, 2023 |
22 | Incline/Decline in Average B-2-B selling price in past 5 years |
23 | Competition from substitute products |
24 | Gross margin and average profitability of suppliers |
25 | New product development in past 12 months |
26 | M&A in past 12 months |
27 | Growth strategy of leading players |
28 | Market share of vendors, 2023 |
29 | Company Profiles |
30 | Unmet needs and opportunity for new suppliers |
31 | Conclusion |
32 | Appendix |