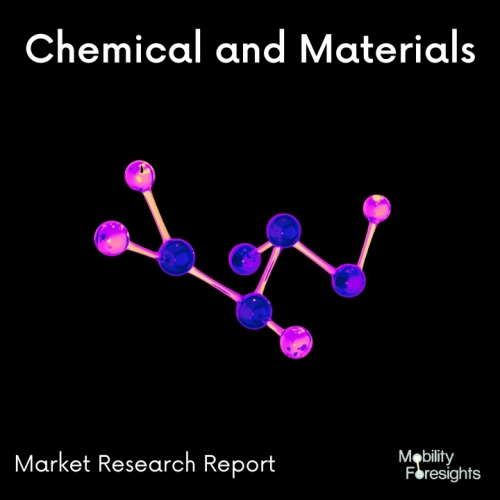
- Get in Touch with Us
Last Updated: Apr 25, 2025 | Study Period: 2024-2030
A flat-panel display or other electronically modulated optical device that makes use of polarizers and the light-modulating capabilities of liquid crystals is known as a liquid-crystal display (LCD) processing chemical. Liquid crystals don't directly emit light; instead, they create colour or monochromatic pictures using a backlight or reflector. There are LCDs that can show random images or fixed images with little information that can be seen or hidden.
Examples of gadgets using these displays include preset words, digits, and seven-segment displays, such as those seen in digital clocks. They both make use of the same fundamental technology, although some displays have larger components, whereas others employ a grid of tiny pixels to create random images.
Depending on the polarizer configuration, LCDs can be either generally on or off. A character negative LCD will have a black backdrop with letters that are the same colour as the backlight, while a character positive LCD will have black writing on a background that is the opposite of the colour of the illumination. Blue LCDs have optical filters applied to the white to give them their distinctive appearance.
There are many different applications for LCDs, such as LCD televisions, computer monitors, instrument panels, cockpit displays for aeroplanes, and interior and outdoor signs. LCD projectors and portable consumer electronics like digital cameras, watches, calculators, and mobile phones, including smartphones, frequently include small LCD panels. In almost all applications, LCD displays have taken the role of heavy, clunky, and less energy-efficient cathode-ray tube displays.
The Global LCD processing chemical Market accounted for $XX Billion in 2023 and is anticipated to reach $XX Billion by 2030, registering a CAGR of XX% from 2024 to 2030.
launch of the SU-3400 Single Wafer Cleaning System by SCREEN. In response to these market developments, SCREEN SPE has been working to create the SU-3400, a brand-new single wafer cleaning system with unmatched productivity.
This system inherits the exceptionally dependable cleaning performance that SCREEN SPE's SU series, the current de facto standard in the sector, has already offered. SCREEN SPE has reduced the size of the cleaning chambers and implemented a new platform with six level, stacked towers with the SU-3400.
The SU-3400 has 24 chambers, the same as the traditional SCREEN SPE system3, but the redesigned structure reduces the system's overall footprint. The SU-3400 also has a cutting-edge wafer transfer system that significantly raises productivity per unit area. The SU-3400 now has a practical processing capability of up to 1,200 wafers thanks to the improved design.
Sl no | Topic |
1 | Market Segmentation |
2 | Scope of the report |
3 | Abbreviations |
4 | Research Methodology |
5 | Executive Summary |
6 | Introduction |
7 | Insights from Industry stakeholders |
8 | Cost breakdown of Product by sub-components and average profit margin |
9 | Disruptive innovation in the Industry |
10 | Technology trends in the Industry |
11 | Consumer trends in the industry |
12 | Recent Production Milestones |
13 | Component Manufacturing in US, EU and China |
14 | COVID-19 impact on overall market |
15 | COVID-19 impact on Production of components |
16 | COVID-19 impact on Point of sale |
17 | Market Segmentation, Dynamics and Forecast by Geography, 2024-2030 |
18 | Market Segmentation, Dynamics and Forecast by Product Type, 2024-2030 |
19 | Market Segmentation, Dynamics and Forecast by Application, 2024-2030 |
20 | Market Segmentation, Dynamics and Forecast by End use, 2024-2030 |
21 | Product installation rate by OEM, 2023 |
22 | Incline/Decline in Average B-2-B selling price in past 5 years |
23 | Competition from substitute products |
24 | Gross margin and average profitability of suppliers |
25 | New product development in past 12 months |
26 | M&A in past 12 months |
27 | Growth strategy of leading players |
28 | Market share of vendors, 2023 |
29 | Company Profiles |
30 | Unmet needs and opportunity for new suppliers |
31 | Conclusion |
32 | Appendix |