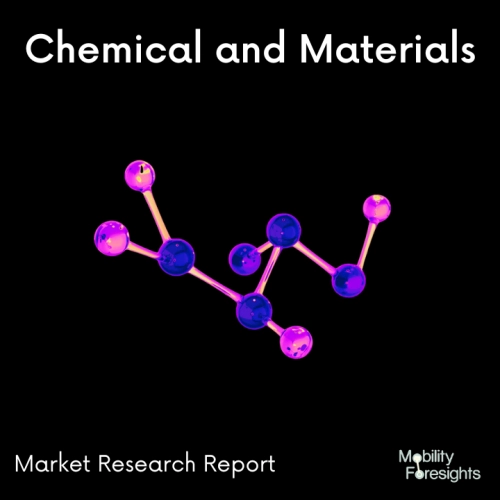
- Get in Touch with Us
Last Updated: Apr 25, 2025 | Study Period: 2024-2030
The chemical substance with the formula LiCoO 2 is LiCoO2 Cathode Powder, sometimes known as lithium cobaltate or lithium cobaltite.
The IUPAC designation lithium cobalt(III) oxide refers to the cobalt atoms' formal +3 oxidation state.Lithium cobalt oxide is a crystalline solid that is typically used in the positive electrodes of lithium-ion batteries. It is a dark blue or bluish-gray solid.
Despite having lower capacity and power than cathodes based on nickel-cobalt-aluminum (NCA) oxides, batteries made using LiCoO2 Cathode Powder have relatively stable capacities.
LiCoO 2 cathodes have slightly better thermal stability issues than other nickel-rich chemistries, but not much. Due to this,LiCoO2 Cathode Powder batteries can experience thermal runaway when subjected to abusive conditions such as overcharging or operating at high temperatures (>130 °C).
The Global LiCoO2 Cathode Powder market accounted for $XX Billion in 2023 and is anticipated to reach $XX Billion by 2030, registering a CAGR of XX% from 2024 to 2030.
Due to its high packing density, high energy density, outstanding cycle life, and reliability, LiCoO2 Cathode Powder,continues to be the most popular cathode for lithium-ion batteries (LIBs) in the portable electronics market.
The upper cutoff voltage of LiCoO2 Cathode Powder -based batteries has been steadily increased in order to achieve higher energy density in order to meet the rising energy demands of portable electronics like smartphones and laptops.
However, charging to a high voltage (>4.2 V vs Li/Li+) can cause a number of harmful problems, such as surface deterioration, harm from destructive phase transitions, and inhomogeneous reactions. This causes the capacity, efficiency, and cycle life to rapidly degrade.
The recycling of used lithium-ion batteries (LIBs) has developed into a critical issue in recent years because of the rising pressure to reduce environmental pollution and ensure the sustainability of the battery metals.
Much research has concentrated on using high temperatures or powerful acid/alkali to convert the utilized active cathode material to a low valence state, which increases recycling and post-treatment expenses. Here, a method for recycling and regenerating LiCoO2 cathode material from used LiCoO2 Cathode Powder batteries is devised. It involves low-temperature roasting followed by water leaching.
In order to reduce the cathode material into water-soluble Li salt (Li2O and Li2CO3) and water-insoluble (Co and CoO), the used LiCoO2 Cathode Powder is heated with glucose (C6H12O6) as a reagent.
Under the ideal conditions of 1 hour of roasting at 550 °C followed by 30 minutes of water leaching with a solid-liquid ratio of 50 g/L, the recovery rates for Li and Co are 97% and 99%, respectively.
It is simple to transform the recovered Li-rich solution and Co-rich residue into Li2CO3 and Co3O4, respectively, which serve as the building blocks for producing new LiCoO2 cathode material. After 800 cycles at 4.4 V, the regenerate LiCoO2 displays improved cycling stability with 87% capacity retention.
Sl no | Topic |
1 | Market Segmentation |
2 | Scope of the report |
3 | Abbreviations |
4 | Research Methodology |
5 | Executive Summary |
6 | Introduction |
7 | Insights from Industry stakeholders |
8 | Cost breakdown of Product by sub-components and average profit margin |
9 | Disruptive innovation in the Industry |
10 | Technology trends in the Industry |
11 | Consumer trends in the industry |
12 | Recent Production Milestones |
13 | Component Manufacturing in US, EU and China |
14 | COVID-19 impact on overall market |
15 | COVID-19 impact on Production of components |
16 | COVID-19 impact on Point of sale |
17 | Market Segmentation, Dynamics and Forecast by Geography, 2024-2030 |
18 | Market Segmentation, Dynamics and Forecast by Product Type, 2024-2030 |
19 | Market Segmentation, Dynamics and Forecast by Application, 2024-2030 |
20 | Market Segmentation, Dynamics and Forecast by End use, 2024-2030 |
21 | Product installation rate by OEM, 2023 |
22 | Incline/Decline in Average B-2-B selling price in past 5 years |
23 | Competition from substitute products |
24 | Gross margin and average profitability of suppliers |
25 | New product development in past 12 months |
26 | M&A in past 12 months |
27 | Growth strategy of leading players |
28 | Market share of vendors, 2023 |
29 | Company Profiles |
30 | Unmet needs and opportunity for new suppliers |
31 | Conclusion |
32 | Appendix |