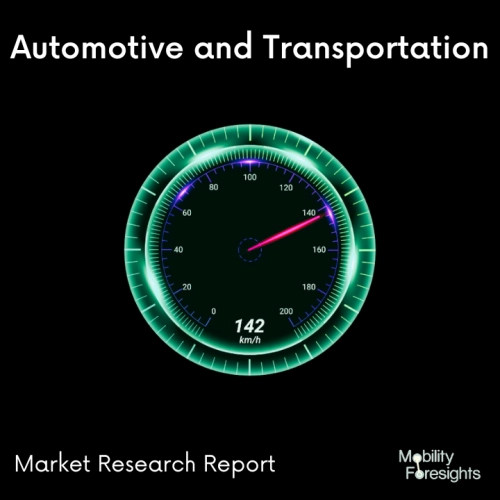
- Get in Touch with Us
Last Updated: Apr 25, 2025 | Study Period: 2024-2030
The drying of the wet particulate electrode coating is a crucial stage in the production of electrodes for lithium-ion batteries. A porous film is created when the solvent evaporates, solidifying the electrode film. Coating and drying were done on anode slurries made of graphite and an aqueous binder system.
An impingement drier and a substrate carrier with temperature control were employed in a lab setup to ensure specified and controllable drying conditions.
The selection of experimental temperatures was based on a computation of steady-state temperatures that arise from gas temperatures that are frequently used in industrial drying processes. This was done to allow a scale-up to continually pass dryers.
The electrodes of conventional lithium-ion batteries are coated using the wet method, which involves combining the active material, a conductive agent, and a binder in a solvent before coating the current collector foil using a slot die coating or transfer coating machine.
However, this method suffers from the issues of a lengthy drying period and solvent recovery, which significantly raises the cost of production and adds to the process complexity.
Dry electrode sheets are created using the TOB New Energy dry electrode method, which involves mixing PTFE binder, active material, and conductive agent at high speed, rolling them through a roller press machine, and then laminating them with current collector foil covered with conductive glue.Because fewer organic solvents are used in this method, the battery's capacity and cycle life are increased.
A new method of making lithium-ion batteries has been developed by MIT spinoff 24M Technologies, which can reduce production costs by as much as 40%. Importantly, the new method may be used with many lithium-ion battery chemistries, suggesting that solutions can make use of the technology.
Due to the use of "gooey electrodes" in the "Semi-solid" design, copper and aluminum, which make up over 80% of the materials in conventional batteries, are no longer necessary. Additionally, it raises the energy density, safety, and recycleability of the batteries.
The battery was developed by MIT spinoff 24M Technologies to lower the price of producing lithium-ion cells.With a novel design that takes fewer components and fewer procedures to produce each cell, the MIT spinoff 24M Technologies has now streamlined the manufacture of lithium-ion batteries. The method also enhances the energy density, security, and reliability.
The electrodes that are positively and negatively charged as well as the electrolyte substance that permits ions to move between them make up the bulk of batteries.
Solid electrodes are used in conventional lithium-ion batteries, which are held in place by layers of inert polymers and metals that separate the electrodes from the electrolyte. One benefit is that it does away with the time- and energy-consuming process of drying and hardening the electrodes used in conventional lithium-ion manufacture.
With more efficient production techniques is a significant industry priority as the demand for batteries is predicted to rise from 185 GWh in 2020 to over 2000 GWh in the future years. Coating active material on top of metal foil to generate the electrode is one of the key phases in the battery production process.
Electrochemical processes take place in this active substance, enabling the electrode to store energy that is later released during cell discharge. The electrodes are dried and squeezed after coating.
The overall drying operations account for around 39% of the energy used in the manufacture of lithium-ion batteries, with the electrode drying stage accounting for about 50% of that usage.
The Global Lithium-ion dry electrode market accounted for $XX Billion in 2023 and is anticipated to reach $XX Billion by 2030, registering a CAGR of XX% from 2024 to 2030.
To enhance the manufacturing of lithium-ion cells, a new electrode drying procedure. The EPIC project, which aims to enhance the electrode drying process for lithium-ion batteries, has received an investment from the German Federal Ministry of Research. By expediting the lithium-ion battery electrode drying process, the new EPIC project, led by Karlsruhe Institute of Technology (KIT), aims to lower the cost of battery manufacturing.
During discharge, lithium ions move through the electrolyte from the negative electrode (anode) to the positive electrode (cathode), producing an electric current. With MOISTURE, WATER, or STEAM, lithium reacts aggressively to produce heat, flammable and explosive hydrogen gas, and poisonous lithium oxide.The electrode layers that are employed for energy storage determine the performance of lithium-based battery cells.
Producing electrodes requires a lot of energy and might take a long time, which raises the cost of production. Now, the Thin Film Technology (TFT) group at KIT has created a novel coating method that allows for the fast production of lithium-ion battery electrodes.
Professor head of TFT: "It is vital to analyse the different process phases collectively and to take interactions into consideration." The project's overall goal is to cut the cost of drying the electrodes for batteries by at least 20%. While preserving the electrodes' quality and long-term stability, scientists from the EPIC project want to speed up drying by at least 50%.
The faster coating speeds are especially appealing when drying times can be shortened without having to lengthen the pricey drying line. Prior to electrolyte filling, KIT will investigate drying directly in the cell stack and adjusting the necessary cell moisture.
A joint investigation between KIT and Technical University of Braunschweig researchers will assess how drying intensity and duration affect cell characteristics. Recommendations for scaling up the process to an industrial level will be given after the project partners have evaluated the various production methods using appropriate process-cost models.
The Post Lithium Storage (POLiS) cluster of excellence, where KIT will work with Ulm University and ZSW to build future batteries, will immediately incorporate the most recent advancements in production technology.
Sl no | Topic |
1 | Market Segmentation |
2 | Scope of the report |
3 | Abbreviations |
4 | Research Methodology |
5 | Executive Summary |
6 | Introduction |
7 | Insights from Industry stakeholders |
8 | Cost breakdown of Product by sub-components and average profit margin |
9 | Disruptive Innovation in the Industry |
10 | Technology Trends in the Industry |
11 | Consumer trends in the industry |
12 | Recent Production Milestones |
13 | Component Manufacturing in the US, EU and China |
14 | COVID-19 impact on overall market |
15 | COVID-19 impact on Production of components |
16 | COVID-19 impact on the point of sale |
17 | Market Segmentation, Dynamics and Forecast by Geography, 2024-2030 |
18 | Market Segmentation, Dynamics and Forecast by Product Type, 2024-2030 |
19 | Market Segmentation, Dynamics and Forecast by Application, 2024-2030 |
20 | Market Segmentation, Dynamics and Forecast by End Use, 2024-2030 |
21 | Product installation rate by OEM, 2023 |
22 | Incline/Decline in Average B-2-B selling price in the past 5 years |
23 | Competition from substitute products |
24 | Gross margin and average profitability of suppliers |
25 | New product development in the past 12 months |
26 | M&A in the past 12 months |
27 | Growth strategy of leading players |
28 | Market share of vendors, 2023 |
29 | Company Profiles |
30 | Unmet needs and opportunities for new suppliers |
31 | Conclusion |
32 | Appendix |