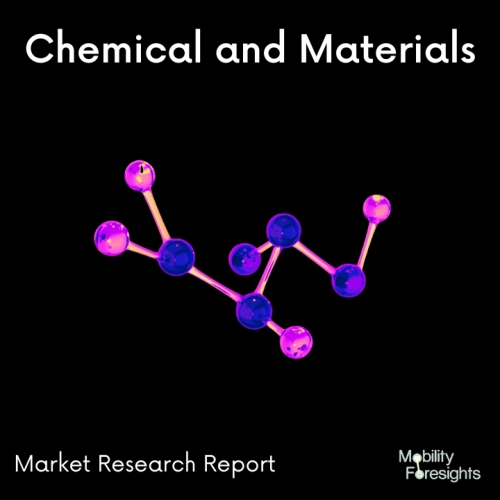
- Get in Touch with Us
Last Updated: Apr 25, 2025 | Study Period: 2024-2030
For different objectives, such as corrosion resistance, thermal insulation, and electrical insulation, a thin layer of magnesium oxide is deposited to the surface of a material and referred to as a magnesium oxide coating.
In sectors like aerospace, automotive, and construction where materials are subjected to extreme environmental conditions, magnesium oxide coating is frequently employed.
The coating serves as a barrier of defense against corrosion and erosion, halting the material's gradual deterioration.
Magnesium oxide coating is advantageous in high-temperature applications because to its outstanding thermal insulation qualities.
It can be used to insulate furnace linings, exhaust systems, and other high-temperature machinery. It can resist temperatures up to 2,000°C (3,632°F).
Additionally, the electrical insulation qualities of magnesium oxide coating make it beneficial in electronic and electrical applications where insulation is required.
Typically, a solution of magnesium oxide and a binder material is sprayed or painted over the surface to be coated with magnesium oxide. The coating is then heated through to generate a firm, long-lasting layer.
Global magnesium oxide coating market accounted for $XX Billion in 2022 and is anticipated to reach $XX Billion by 2030, registering a CAGR of XX% from 2024 to 2030.
Magnesium alloys can be shielded from corrosion and wear with magnesium oxide coatings. Along with titanium oxide and zirconium oxide coatings, magnesium oxide is one of the metal oxides that can be applied for this purpose.
Magnesium oxide coatings are insufficient for long-term protection of magnesium alloys due to several drawbacks, such as the fact that they absorb water or dissolve in a humid or acidic environment.
Researchers have created composite coatings with zirconium oxide particles to enhance the characteristics of magnesium oxide coatings.
These composite coatings have been demonstrated to improve biological responsiveness, corrosion resistance, and hardness.
In order to improve the wear and corrosion resistance of magnesium alloys, ceramic-like oxide coatings can also be created using the Microarc Oxidation (MAO) technology.
However, MAO coatings made mostly of MgO are less effective at shielding magnesium alloys than coatings made primarily of ZrO2 or ZrO2 with a compact microstructure Coatings for magnesium alloys can be applied using a variety of techniques.
One of the most often applied coating processes for magnesium alloys is conversion coating. In order to do this, the natural oxide that develops on magnesium alloys must be removed, and a nonporous, crack-free barrier coating must be applied.
Plasma Electrolytic Oxidation (PEO), a conversion coating process based on an electrolyte solution, is another technique for enhancing the performance of light metals and their alloys, including magnesium.
It has been demonstrated that PEO coatings are more efficient than traditional chrome-based conversion methods.
To complement its AdvanTech subfloor assembly and ZIP System building enclosure solutions with EXACOR Magnesium-Oxide (MgO) panels, Huber Engineered Woods has launched a new brand.
The MgO structural panels give contractors a technique to create flooring assemblies for multifamily and light commercial buildings that are both fire resistant and acoustically effective.
The self-levelling gypsum underlayment that is frequently used in these assemblies can be poured by existing frame workers without the assistance of a separate subcontractor because of the ability to install the panels.
EXACORTM panels, which are a part of flooring systems, give construction teams a simple-to-work-with panel design with a patented internal mesh fibre for structure and a magnesium-oxide formula for dimensional stability, fire protection, and sound dampening.
When compared to fire-rated floor assemblies that need gypsum underlayment, EXACOR, which is available in nominal thickness options of 1/2" (12mm), 5/8" (16mm), and 3/4" (20mm), can help cut down on both the amount of material needed and the amount of labour required.
It has been demonstrated, as part of specific tested assemblies, to meet or exceed code minimums for STC/IIC ratings for dwelling separations without the use of gypsum underlayment.
It can be used as a structural subfloor (UL 263 Design No. L601) as well as a subfloor underlayment over conventional OSB or plywood (UL 263 Design No. L528).
In fact, for certain 1-hour fire-rated floor/ceiling assemblies using EXACOR panels, builders can fully omit the extra step of including gypsum underlayment without sacrificing sound protection.
Building teams can save time, money, and resources by using EXACOR panels since they have structural qualities similar to those of wood and have fire- and sound-resistance ratings that can replace the requirement for gypsum underlayment.
They have listened to and taken advice from their dependable construction and design partners, who share the Huber concept of always wanting to know how to build better things. For the multifamily and light commercial project site, they're pleased to present yet another innovation.
The manufacture of highly active magnesium oxide has begun by Russian Mining Chemical Company LLC (RMCC), which is also expanding its selection of premium magnesium compounds.
The item is produced at the recently established third processing facility in Vyazma, Smolensk region, Russia, and is sold under the brand name MagPro®. Magnesium oxide in micronized forms is most frequently utilised to make synthetic rubbers that contain halogens.
MagPro® is specifically employed as an acid acceptor (HCl) and premature polymerization inhibitor during the manufacture of synthetic rubber. It serves as a thickener in premixes and prepregs used in the manufacturing of SMC and BMC.
With the use of this technique, it is possible to prevent the magnesium oxide from becoming contaminated with the byproducts of fuel combustion and to stop the product from overheating, both of which would
Sl no | Topic |
1 | Market Segmentation |
2 | Scope of the report |
3 | Abbreviations |
4 | Research Methodology |
5 | Executive Summary |
6 | Introduction |
7 | Insights from Industry stakeholders |
8 | Cost breakdown of Product by sub-components and average profit margin |
9 | Disruptive innovation in the Industry |
10 | Technology trends in the Industry |
11 | Consumer trends in the industry |
12 | Recent Production Milestones |
13 | Component Manufacturing in US, EU and China |
14 | COVID-19 impact on overall market |
15 | COVID-19 impact on Production of components |
16 | COVID-19 impact on Point of sale |
17 | Market Segmentation, Dynamics and Forecast by Geography, 2024-2030 |
18 | Market Segmentation, Dynamics and Forecast by Product Type, 2024-2030 |
19 | Market Segmentation, Dynamics and Forecast by Application, 2024-2030 |
20 | Market Segmentation, Dynamics and Forecast by End use, 2024-2030 |
21 | Product installation rate by OEM, 2023 |
22 | Incline/Decline in Average B-2-B selling price in past 5 years |
23 | Competition from substitute products |
24 | Gross margin and average profitability of suppliers |
25 | New product development in past 12 months |
26 | M&A in past 12 months |
27 | Growth strategy of leading players |
28 | Market share of vendors, 2023 |
29 | Company Profiles |
30 | Unmet needs and opportunity for new suppliers |
31 | Conclusion |
32 | Appendix |