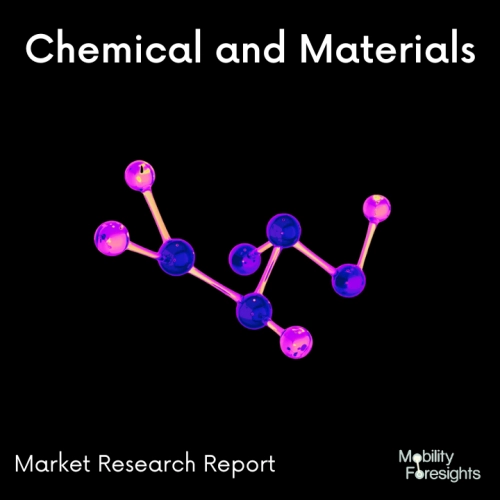
- Get in Touch with Us
Last Updated: Apr 25, 2025 | Study Period: 2023-2030
Magnesium-zinc alloys are a combination of two of the most commonly used light metals, magnesium and zinc. Magnesium is known for its strength, light weight, and corrosion resistance, while zinc has a wide range of uses due to its malleability and ductility. When combined, these two metals create an alloy that has unique properties that can be used in a variety of applications.
Magnesium-zinc alloys are used in a variety of industries including automotive, aerospace, and sporting goods. In automotive applications, the alloy is often used to make chassis components, suspension arms, and brake parts.
In aerospace applications, it is used for structural components, such as brackets and clamps, and in the construction of aircraft wings. In sporting goods, magnesium-zinc alloys are used for high-strength components, such as golf clubs, tennis rackets, and baseball bats.
The advantages of magnesium-zinc alloys include superior strength and wear resistance, high corrosion resistance, good impact strength, and good wear resistance.
The alloy also has excellent machinability, meaning that it can be easily formed into complex shapes. Additionally, magnesium-zinc alloys are generally more economical than pure magnesium or zinc.
The main disadvantage of magnesium-zinc alloys is that they tend to be more brittle than pure metals. This can lead to cracking and deformation when exposed to high stress. Additionally, the alloy is not suitable for applications that require high temperatures. Finally, the alloy is not suitable for welding due to its low melting point.
The Global Magnesium Zinc Alloy Market accounted for $XX Billion in 2022 and is anticipated to reach $XX Billion by 2030, registering a CAGR of XX% from 2023 to 2030.
As magnesium alloys are among the lightest structural materials available for commercial use, they have long been employed in spacecraft and aviation applications. Magnesium alloys also possess good machinability, a high specific strength, elastic stiffness, and a great damping capability.
Zinc is typically combined with aluminium, zirconium, rare earth elements, or thorium to create strong magnesium alloys that precipitate harden.Current energy-saving techniques encouraged attempts to minimise a vehicle's overall weight as well as the weight of its moving parts.
Because they may greatly reduce a vehicle's weight, wrought magnesium alloys have been looked into for use in automotive applications more and more recently.The alloys based on the Mg-Al system, like Mg-Al-Zn (also known as AZ) and Mg-Al-Mn (AM series), are the most often used alloys.
The low-melting Mg17Al12 phase that occurs in these materials is the reason for their inadequate creep resistance, which makes them unsuitable for uses over 120°C.
The presence of second phases from the systems Al-RE, Al-Sr, or Al-Ca at the grain boundaries, which are stable compounds with a relatively high melting point, characterises the microstructure of the Mg-Al-RE (AE series), Mg-Al-Ca-Sr (AXJ series), and Mg-Al-Sr (AJ series), which have better creep resistance. These alloys can operate at temperatures no higher than 180°C.
Iron and nickel impurities that may be present in the magnesium alloy are additional detrimental corrosives that zinc helps counteract. To lower the cost of manufacturing, rare earth metals are added either as "mischmetal compound."
A significant improvement in ductility and strength at high temperatures is achieved by adding rare earth elements.Among these, the magnesium-zinc system (Mg-Zn) shows the most promise for the creation of low-cost magnesium alloys with improved strength and resilient against corrosion.
To obtain a fair compromise between mechanical properties and corrosion performance, this thesis synthesised and investigated in detail low-Zn containing Mg-Zn alloys that were micro-alloyed with different ternary alloying components.
Sl no | Topic |
1 | Market Segmentation |
2 | Scope of the report |
3 | Abbreviations |
4 | Research Methodology |
5 | Executive Summary |
6 | Introduction |
7 | Insights from Industry stakeholders |
8 | Cost breakdown of Product by sub-components and average profit margin |
9 | Disruptive innovation in the Industry |
10 | Technology trends in the Industry |
11 | Consumer trends in the industry |
12 | Recent Production Milestones |
13 | Component Manufacturing in US, EU and China |
14 | COVID-19 impact on overall market |
15 | COVID-19 impact on Production of components |
16 | COVID-19 impact on Point of sale |
17 | Market Segmentation, Dynamics and Forecast by Geography, 2023-2030 |
18 | Market Segmentation, Dynamics and Forecast by Product Type, 2023-2030 |
19 | Market Segmentation, Dynamics and Forecast by Application, 2023-2030 |
20 | Market Segmentation, Dynamics and Forecast by End use, 2023-2030 |
21 | Product installation rate by OEM, 2023 |
22 | Incline/Decline in Average B-2-B selling price in past 5 years |
23 | Competition from substitute products |
24 | Gross margin and average profitability of suppliers |
25 | New product development in past 12 months |
26 | M&A in past 12 months |
27 | Growth strategy of leading players |
28 | Market share of vendors, 2023 |
29 | Company Profiles |
30 | Unmet needs and opportunity for new suppliers |
31 | Conclusion |
32 | Appendix |